Una dintre condițiile necesare pentru a asigura precizia și durabilitatea necesare a mașinii este instalarea corectă și fixarea pe fundație. Tipul de fundație depinde de sarcina transferată la baza mașinii, de greutatea mașinii și de forțele de inerție care acționează în timpul funcționării mașinii. Fundațiile pentru mașinile de tăiat metale sunt de două tipuri: prima - fundația, care este doar baza mașinii, a doua - fundația, care sunt rigid conectate la mașină și dau mașinii stabilitate și rigiditate suplimentare. Strungurile sunt instalate, de regulă, pe fundamentele celui de-al doilea tip, în conformitate cu desenul de instalare, care este dat în manualul mașinii. Desenul indică dimensiunile necesare pentru fundație, precum și amplasarea mașinii în cameră, ținând seama de spațiul liber pentru părțile proeminente și mobile ale mașinii. Când instalați mașina pe o bază de beton, așezați cuibul în funcție de dimensiunile corespunzătoare găurilor de montare ale patului mașinii, iar apoi cuiburile sunt tăiate. După instalarea și alinierea mașinii la nivel, șuruburile de fundație sunt umplute cu mortar de ciment. Instalarea mașinii în plan orizontal este verificată cu ajutorul unui nivel instalat în mijlocul culisei paralel și perpendicular pe axa centrelor. În orice poziție a căruciorului pe ghidajul mașinii, abaterea nivelului nu trebuie să depășească 0,04 mm la 1000 mm. Dacă șuruburile de fundație sunt preumplute în fundație, atunci se face o reconciliere atunci când acestea nu sunt strânse. După instalare și reconciliere, o inspecție exterioară a mașinii este efectuată și testată la ieșire, sub sarcină, pentru acuratețe și rigiditate.
Testați mașina la ralanti. Direcția mișcării principale este verificată ulterior în toate etapele vitezei de rotație. Verificați apoi interacțiunea tuturor mecanismelor mașinilor; fiabilitate și oportunitate, pornirea și oprirea mecanismelor de la diferite dispozitive de comandă; activitatea organelor guvernamentale; serviceabilitatea sistemului de alimentare cu lichid de răcire și a echipamentelor hidraulice și pneumatice ale mașinii. În timpul procesului de încercare la mers în gol, mașina trebuie să funcționeze în mod constant în toate modurile, fără a bate și vibrații care generează vibrații. Mișcarea pieselor de lucru ale mașinii printr-o mișcare mecanică sau hidraulică trebuie să se desfășoare fără probleme, fără salturi și blocaje. Când se testează mașina la ralanti, sunt verificate și datele pașaportului (viteza arborelui, furaje, mișcări ale carierei etc.). Datele reale trebuie să corespundă valorilor indicate în pașaport.
Testarea echipamentului sub sarcină vă permite să identificați calitatea lucrărilor sale și efectuați în condiții apropiate de producție. Testul se efectuează prin procesarea eșantioanelor în astfel de moduri încât sarcina să nu depășească puterea nominală de antrenare în timpul timpului principal de încercare. În timpul încercării, mașina poate fi supraîncărcată temporar în capacitate, dar nu mai mare de 25%. Timpul de încercare al mașinii sub sarcină maximă trebuie să fie de cel puțin 0,5 h. În același timp, toate mecanismele și mecanismele de lucru ale mașinii trebuie să funcționeze corect; sistemul de alimentare cu lichid de răcire trebuie să funcționeze în mod fiabil; Temperatura lagărelor de alunecare și de rulare nu trebuie să depășească 70-80 grade C, mecanismele de alimentare 50 grade C, ulei în rezervorul 60 C.
Mașinile noi în timpul funcționării și, de asemenea, după reparații sunt verificate cu precizie geometrică în stare descărcată, cu precizia pieselor prelucrate și cu rugozitatea suprafeței tratate. Cerințele de precizie sunt stabilite în manualul de instrucțiuni al mașinii. La verificarea corectitudinii mașinii, verificați mișcarea longitudinală a suportului în plan orizontal; rotația în rotație a axului arborelui vagonului și axa găurii pintei în raport cu ghidajul patului în plan vertical; ieșirea radială a suprafeței de centrare a axului capului pentru instalarea cartușului; traversarea axială a axului vagonului, etc.
Straightness a mișcării longitudinale a suportului în plan orizontal este verificată cu un dorn cilindric fixat în centrele din față și tailand și indicatorul montat pe suport, figura de mai jos este a). Prin deplasarea coapsei în direcția transversală, se realizează faptul că citirile indicatoarelor la capetele dornului sunt aceleași sau diferă cu nu mai mult de 0,02 mm pe 1 m de cursa șaibei.
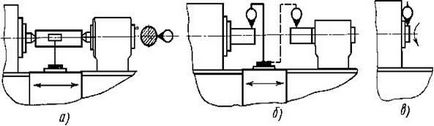
Odnovysotnost axa de rotație a axului traversa frontală și tailstock axa găurii în raport cu cadrul de ghidare într-un plan vertical, este verificată după îndepărtarea din față păpușa mobilă 1/4 din distanța maximă dintre centrele figura de mai sus - b). Realizată prin utilizarea dornuri cilindrice introduse în gaura de ax și condeiului tailstock și indicatorul montat pe etrier. Cel mai mare indicator citit pe generatoarea axului dornului determină o mișcare alternativă transversală a unui suport într-un plan orizontal în raport cu linia centrală. Fără schimbarea poziției indicatorului, indicațiile acestuia pe dornul de formare a coamei sunt determinate în același mod. Diferența dintre indicațiile indicatorului nu trebuie să depășească 0,06 mm pentru mașinile pentru prelucrarea pieselor cu diametrul cel mai mare de 400 mm. Este permisă numai depășirea axei orificiului de pe muchie deasupra axei axului vagonului.
Rulajul radial al suprafeței de centrare a axului capului pentru cartuș este verificat cu ajutorul unui indicator, figura de mai sus este c). În acest caz, tija de măsurare a indicatorului este montată perpendicular pe generatorul de gât de centrare a axului. Baterea radială a gâtului axului rotativ pentru cartușul cu diametrul cel mai mare al piesei de lucru 400 mm nu trebuie să depășească 0,01 mm.
Deblocarea axială a axului vântului se măsoară cu un dorn introdus în orificiul arborelui și un indicator montat pe mașină cu un ax rotativ, figura de mai jos este d). Tija de măsurare a indicatorului cu un vârf plat se sprijină pe bila, care este instalată în orificiul central al dornului. Îndepărtarea axială a axului pentru instalarea pieselor cu diametrul cel mai mare de 400 mm nu trebuie să depășească 0,01 mm.
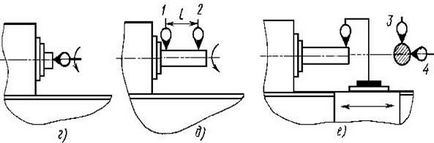
Radial hole runout conic al axului păpușii este verificată cu o lungime dorn L = 300 mm, introdus în gaura de ax și un indicator montat în mașină, la o rotire a axului portsculă, grafic de mai sus - d). Pentru mașinile cu cel mai mare diametru al piesei 400 mm radială bătaia fusului dornului la capătul axului (poziția 1) nu trebuie să depășească 0,01 mm și o distanță L = 300 mm de la suprafața frontală a axului (poziția 02 mm.
Paralelismul ax headstock deplasarea longitudinală a axei de rotație a unui dorn suport verificată printr-o lungime L = 300 mm, instalat în gaura ax și un indicator montat pe o mașină de suport, figura de mai sus - e). Măsurarea se face pe dornul de formare în planurile verticale (poziția 3) și orizontală (poziția 4). Astfel citiri ale indicatorului în două mandrine formând diametral aranjate (la 180 de grade de rotație a axului) prin deplasarea șa cu nasul indicator ax cu o distanță L = 300 mm. Apoi se determină media aritmetică a abaterilor măsurate de cele două generatoare (separat pentru planurile orizontale și verticale). Pentru mașinile cu cel mai mare diametru al piesei 400 mm nealinierea admisibilă direcția axei tijei de mișcare longitudinală a etrierului în planul vertical nu trebuie să depășească 0,03 mm (și paralelismul trebuie să fie îndreptate în sus) și într-un plan orizontal - 0,012 mm (paralelism trebuie să fie îndreptate numai în direcția suportului).
Precizia strungurilor este verificată la prelucrarea probelor. La mașinile cu diametrul cel mai mare al piesei de prelucrat 400 mm, precizia formei geometrice a suprafeței cilindrice este verificată prin prelucrarea eșantioanelor de 200 mm lungime. O probă pre-tratată cu trei curele situate la capete și în mijlocul specimenului este plasată în mandrină sau în centrele mașinii și este prelucrată de-a lungul suprafeței exterioare a curelelor. Verificați constanța diametrului în orice secțiune transversală, iar diferența dintre valorile maxime și cele minime măsurate nu trebuie să depășească 0,02 mm. Măsurarea se face cu ajutorul unui instrument de măsurare a treptei, a micrometrului sau a altor instrumente.
Nivelul de suprafață al suprafeței de capăt este verificat prin prelucrarea eșantioanelor cu diametrul d = 200 mm, instalat în mandrinele cartușului. Suprafața de capăt a eșantionului poate avea caneluri inelare (la periferie, în centru și în centru) și trebuie tratată prealabil. După canelura suprafeței de capăt, eșantionul nu este scos din mașină. Rezultatele tratamentului pot fi verificate printr-un indicator montat pe etrier, astfel încât vârful indicatorului să fie perpendicular pe suprafața măsurată. Măsurarea se efectuează prin deplasarea în direcția transversală a părții superioare a suportului cu o lungime egală sau mai mare decât D. Abaterea, definită ca jumătate din cea mai mare diferență de indicator algebric, nu trebuie să depășească 0,016 mm. Nivelul plat al feței de capăt poate fi verificat și prin atingerea vârfului indicatorului liniei de control atașat la capătul prelucrat al specimenului. Chinga este aplicată în diferite secțiuni axiale ale suprafeței testate, iar abaterea este determinată în același mod ca cel descris mai sus.
precizia de tăiere a firului se verifică pe eșantion (diametru aproximativ egal cu diametrul axului șurubului al mașinii), montate în centrele de mașini, când tăierea trapezoidal lungimea firului nu depășește 500 mm, cu un pas aproximativ egal cu mașina pas ax. În același timp, șurubul de plumb este conectat direct la ax prin rotițe interschimbabile, cu mecanismul cutiei de alimentare deconectat. După finalizare, verificați uniformitatea firului cu ajutorul unor instrumente și metode de testare adecvate. Rezultatele măsurătorilor determină eroarea acumulată de pasul filetului - diferența dintre distanța efectivă și predeterminată între oricare dintre același nume (nu adiacent) profilurile filetului în secțiunea axială, de-a lungul unei linii paralele cu axa șurubului. Valoarea erorii acumulate a pasului filetului nu trebuie să depășească 0,04 mm la o lungime de 300 mm.
Articole similare
Trimiteți-le prietenilor: