Curățarea cerealelor de impurități este cea mai importantă metodă în prelucrarea cerealelor, ceea ce afectează în mod semnificativ stabilitatea calității cerealelor depozitate; îmbunătățirea calității livrărilor de cereale transferate la prelucrare; Creșterea eficienței și productivității echipamentelor tehnologice incluse în procesul de proiectare după curățare; Creșterea gradului de utilizare a cerealelor prin utilizarea deșeurilor dedicate pentru furaje.
În mașinile de curățat cerealele sunt utilizate diferite organe de lucru, ale căror lucrări se bazează pe utilizarea unei anumite trăsături a divizibilității masei de cereale.
Semne de divizibilitate a masei de cereale: dimensiuni (lungime, grosime, lățime); proprietăți aerodinamice (viteza de înfășurare); forma și suprafața (proprietăți de frecare); densitate (proprietăți gravitaționale); culoare, elasticitate, proprietăți magnetice etc.
Principii și metode de separare a boabelor și a impurităților, cele mai utilizate în practică:
- lățime - pe site cu găuri rotunde;
- grosime - pe site cu găuri alungite;
- de-a lungul lungimii - pe suprafața celulară;
- în formă - pe site cu găuri formate (de exemplu, găuri triunghiulare) sau pe o suprafață netedă înclinată;
- prin proprietăți aerodinamice - în canalele pneumatice de separare;
- prin forma și starea suprafeței - pe un plan înclinat păros;
- privind elasticitatea și coeficientul de frecare la impact - separarea cu vibrații;
- proprietăți magnetice - separare magnetică;
- prin densitatea și coeficientul de frecare - deplasarea vibrațiilor;
- densitate - în cazul auto-sortare pe suprafețe conice cu vibrații de translație circulară;
- prin dimensiuni, coeficientul de frecare, densitatea - pe sitele înclinate fixe.
Există o mare varietate de mașini de curățat cereale, în organele de lucru ale căror principii de separare a cerealelor sunt realizate unul sau mai multe principii. De exemplu: separatoare de ecran (pe ecrane), separatoare de sită de aer (ecrane și separare pneumatică în canale); triera (pe o suprafață celulară); coloane de aspirație, separatoare de aer (proprietăți aerodinamice); mașini de separare a pietrelor vibro-pneumatice, mese de sortare (mișcarea vibrațională în stratul gazos fără cernere); mașini de separare a pietrelor (suprafețe conice oscilante); sortatoare de diapozitive (pe site-uri înclinate fixe); separatoare magnetice (prin susceptibilitate magnetică) etc.
Cazuri tipice de aplicare a mașinilor de curățat cereale:
- separatoare de sită - pentru curățarea masei de granule de impurități mari și mici (pentru transportul pneumatic sunt utilizate într-un sistem cu separator pneumatic);
- separatoare aer-aer - pentru sortarea impurităților mari, mici și ușoare (aspiraționale), a cerealelor fragile, a prafului;
- triera - să izoleze ovăzul și aula de la masa grâului;
- Coloane de aspirație și separatoare de aer - pentru curățarea impurităților ușoare și a boabelor fragile;
- mașini de separare a pietrelor vibro-pneumatice, mese de sortare - pentru îndepărtarea impurităților minerale, separarea produselor de peeling al culturilor de cereale cu eliberarea miezului;
- mașini de separare a pietrelor - pentru curățarea impurităților minerale;
- separatoare magnetice - pentru a elimina impuritățile magnetice metalice.
Curățarea cerealelor trebuie efectuată în conformitate cu instrucțiunile din instrucțiunile pentru curățarea cerealelor și a mașinilor de curățare a cerealelor la întreprinderile care primesc cereale.
În procesul de funcționare este prevăzut modul de funcționare a mașinilor de curățat cereale, ceea ce face posibilă obținerea eficienței maxime a curățării cerealelor (nu mai mică decât pașaportul tehnic reglementat pentru mașină).
Linile tehnologice includ: pre-curățarea pe ceară sau separatoare înainte de uscare (pentru a elimina impuritățile grosiere și ușoare); curățarea unică sau dublă a cerealelor pe separatoarele de sită de aer (după uscare) pentru a aduce cerealele în condițiile necesare.
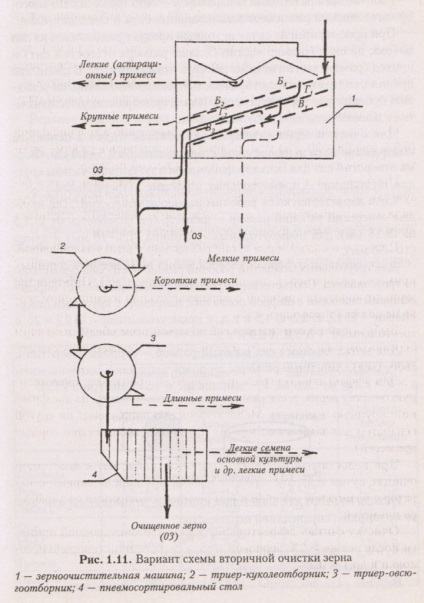
Controlul calității este efectuat de laborator.
Curățarea este condiționată de un "mediu de puritate" și de "buruieni" de alimente, expediate pentru uscare în uscătoare de cereale pentru cereale; dacă există semne de creștere a temperaturii peste normal pentru aceste condiții de depozitare (în afara rândului); infectate cu dăunători de stocuri de cereale; contaminate cu impurități cu un miros neobișnuit cu cereale (în afara rândului).
Pentru a stabili modul optim de funcționare a mașinii de curățat cereale, se efectuează o curățare de probă a cerealelor, cu determinarea efectului tehnologic (TE). TE se determină prin eliminarea echilibrului cantitativ-calitativ al fracțiunilor de masă de cereale (cereale și deșeuri).
Selectarea tuturor fracțiunilor se efectuează simultan timp de un minut (0,5 m la Q 20 t / h) pentru o funcționare la starea de echilibru a mașinii cel puțin de trei ori dintr-un lot cu o masă de cel puțin 5 tone.
Trial de purificare de cereale poate fi considerat încheiat dacă rezultatul modului de funcționare selectat trebuie curățit de separatorul de cereale cu o singură trecere, cel puțin 60% din impurități separate este retras la performanța de operare.
Modul selectat trebuie respectat de către întregul personal de întreținere și nu poate fi modificat fără ordinul șefului punctului (tehnician-șef).
Pentru separarea eficientă a impurităților, se efectuează curățarea fracționată a cerealei, adică cu separarea masei de granule în două fracții: grosiere și fine. Fracțiunea fină este trimisă unui alt separator pentru a separa impuritățile fine (nisip, semințe de buruieni).
Atunci când efectul de curățare este insuficient, se recurge la reciclare prin returnarea cerealelor de la santină la primul separator, cu înlocuirea posibilă a sitelor din acesta, în funcție de natura impurităților.
Organele de lucru ale separatoarelor de sită de ecran (site) Prin metoda de fabricație se disting sitele ștanțate și sitele metalice.
Atunci când se efectuează screening-ul pe site, produsul inițial este împărțit în două fluxuri într-o gură (dimensiunea particulelor este mai mare decât dimensiunea găurilor de sită) și trecerea (dimensiunea particulelor este mai mică decât dimensiunea găurilor de sită). În adunare, de regulă, există o anumită parte a particulelor de trecere care nu au reușit să cadă prin găuri. Masa lor, exprimată ca procent din masa coborârii, se numește subponderal.
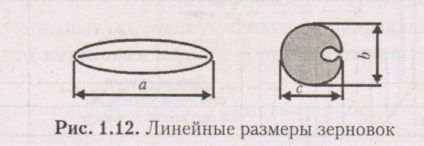
Sitele sunt caracterizate prin dimensiunile de lucru ale găurilor pentru găuri rotunde, dimensiunea de lucru fiind diametrul (variază de la 1,5 la 16 mm), pentru cele dreptunghiulare - lățimea (1,5-10 mm) și lungimea (10-50 mm).
Dimensiunile de lucru pentru deschideri triunghiulare - laterală a unui triunghi echilateral. Prin urmare, dimensiunea de lucru icoanelor reprezintă un anumit număr după ei, de exemplu, cu găuri rotunde - 12, 2.2, 1.5 etc. cu dreptunghiulare -. 2.2 20, cu triunghiulare - 5.0, 6.0 și așa mai departe. d.
Pentru sitele cu ecran metalic, dimensiunea de lucru este latura găurii în lumină (mm). Dimensiunile liniare ale cerealelor sunt exprimate prin relația și b c, unde a este lungimea, b este lățimea și c este grosimea (figura 112).
Datorită acestui fapt, pentru separarea impurităților care diferă de cereale în lățime, se menține următoarea inegalitate:
unde b3 și bpr sunt lățimea cerealelor și a impurităților, mm;
d este diametrul găurii de sită, mm.
Starea superioară: cerealele - prin convergență; impuritățile - prin trecere.
Starea inferioară: cereale - prin trecere; impurități - coborâre.
Pentru a izola impuritățile care diferă în funcție de grosime, utilizați următoarea relație:
unde c3 și спр - grosimea cerealelor și a impurităților, mm;
a este lățimea deschiderii dreptunghiulare, mm.
Starea inferioară: cereale - prin trecere; impurități - coborâre.
Starea superioară: cerealele - prin convergență; impuritățile - prin trecere.
Dimensiunile găurilor pentru primirea ecranelor pentru curățarea cerealelor:
- grâu, secară, orz alimentar, ovăz, mei, orez - cereale - 8-16 (18-20);
- hrana de porumb, mazare, soia, floarea-soarelui - 10-18.
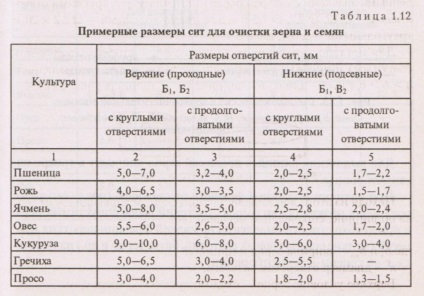
Dimensiunile orificiilor de sită pentru curățarea cerealelor și a semințelor de culturi diferite sunt prezentate în Tabelul. 1.12.
Pentru a izola impuritățile lungi, boabele sunt curățate într-un trireme - ovsyugorotornike.
. În prezența unei fracții mari de purificat (după separatoare) de semințe de cereale mici de buruieni peste limitele admisibile și, dacă este necesar, separate din fracția fină de impurități scurte (semințe minore de buruieni, cereale sparte, etc.) Obiective la blocul de curățare lor - neghină.
Copacii sunt cilindrici și discuri. Primul corp de lucru este un cilindru cu ochiuri pe suprafața interioară, cel de-al doilea are discuri cu ochiuri pe ambele părți. Dimensiunile celulei sunt date în Tabelul. 1,13 și 1,14.
Atunci când trierul funcționează, fracțiile de masă scurtă de granule intră în plasă și, la un anumit unghi de înclinare a suprafeței de lucru rotative, cad în jgheab și sunt scoase din mașină.
De exemplu, pentru curățarea grâului din impurități scurte, trierele sunt echipate cu următoarele discuri, numărând de la recepție: patru discuri de tip 1 cu o lungime și o lățime de celulă de 4,0 mm; trei discuri de tipul 2 cu lungime și
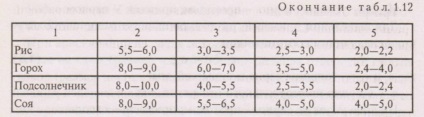
Unele reguli generale de funcționare - mașini de curățat cereale
Înainte de a porni mașina, personalul de service verifică starea sa tehnică și elimină orice neconcordanță cu reglementările tehnice.
În timpul funcționării mașinii de curățat cereale, personalul de întreținere trebuie:
- pentru a monitoriza funcționarea normală a tuturor componentelor mașinii, nu permite încălzirea excesivă a rulmenților. Dacă se încălzesc - opriți mașina, aflați cauza și eliminați-o; asigură o întreținere neîntreruptă și uniformă a mașinii cu cereale și curățarea cerealelor și a deșeurilor curățate;
- să efectueze controlul regulat al calității cerealelor curățate, împiedicând astfel impuritățile să treacă în granulele curățate sau în derivarea cerealelor principale în deșeuri;
- controlul calității deșeurilor.
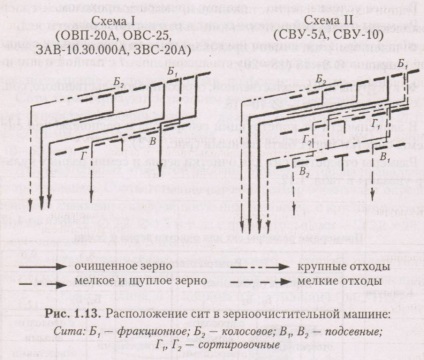
Dacă trebuie să opriți mașina, apoi timp de 3-5 minute înainte de oprire, aceasta oprește alimentarea cerealelor pentru a îndepărta resturile de cereale și deșeuri din aceasta.
La trecerea la curățarea unei alte culturi, este necesară curățarea temeinică a mașinilor, pentru care, după terminarea alimentării cu cereale, acestea ar trebui să funcționeze la ralanti până când cerealele sunt îndepărtate complet de ele.
Este necesară respectarea procedurii stabilite pentru punerea în funcțiune a mașinii și a mecanismelor. Acestea sunt activate secvențial de la mașina sau mecanismul final din circuit la prima. Deschiderea treptată a blocurilor instalate în buncărele de deasupra mașinilor, reglează performanța în conformitate cu caracteristicile tehnice ale acestei culturi.
La sfârșitul curățării cerealelor, mașinile sunt oprite după cum urmează: alimentarea cu cereale este oprită, apoi mașinile și mecanismele sunt oprite ulterior în ordine inversă până la pornire.
Funcționarea separatoarelor cu sită de aer:
În separatoarele cu mișcare alternativă a corpului ecranului, ecrane cu găuri alungite sunt atașate la cadru astfel încât axa lungă a găurilor să fie localizată de-a lungul ecranului (de-a lungul traseului de granulație). Cu mișcarea circulară de translație a corpului, această restricție nu există.
Sith trebuie să îndeplinească următoarele cerințe:
- aranjamentul orificiilor trebuie să fie uniform, fără a întrerupe liniștea rândurilor și omisiunilor;
- Dimensiunile găurilor de-a lungul întregului plan al ecranului trebuie să fie aceleași;
- Pe suprafața sitelor nu ar trebui să se afle niciun fel de zgârieturi și locuri proeminente;
- lenjeria de pat nu ar trebui să aibă crăpături, defecte pe margini, poduri deformate și rupte;
- Nu permiteți bavuri pe suprafața de lucru a ecranului.
Selectarea sitelor trebuie să aibă o atenție deosebită. Selecția necorespunzătoare a acestora este unul din principalele motive pentru curățarea insuficientă a cerealelor din impurități și sortarea slabă.
Atunci când separatorul funcționează, boabele integrale nu trebuie să treacă de la ecranele de recepție și ecranare la deșeuri, iar din cereale care provin din sita trebuie să existe impurități de origine organică și anorganică. Prezența cerealelor (peste 2,0% din masa deșeurilor) în deșeuri indică faptul că sitele nu sunt selectate corespunzător, iar boabele sunt turnate prin fante.
Este necesar să se asigure o livrare uniformă de grâu pe ecranul mașinii pe întreaga lățime a alimentatorului. Cerealele care intră în ecranul de recepție trebuie să fie distribuite într-un strat uniform și apoi să se deplaseze de-a lungul întregii lățimi a ecranelor de sortare și de însămânțare. Când mașina funcționează la capacitate maximă, ecranul de sortare trebuie să fie umplut cu granulație până la 2 / 3-3 / 4 din lungimea sa, numărând de la începutul ecranului.
Trebuie asigurată curățarea normală a sitei.
După o funcționare continuă a separatorului de sită de aer timp de 60-80 de ore, acesta este oprit, îndepărtează ecrane de sortare și de cernere, verifică starea pânzei, dimensiunea găurilor și le curăță cu atenție de particulele lipite în găuri.
Funcționarea trierului (BPS, TLG-8, 3, bloc TB-3O, ZTK-5I, ZTO-5L, A9-ZTK-6, A9-UTO-6)
Cerealele, trimise la triere, sunt pre-curățate pe separatoarele de sită de aer.
În discul trireme, stratul de granule trebuie să fie întotdeauna mai mare decât nivelul axei arborelui cu disc cu 50-100 mm.
Periodic, nu mai puțin de o dată pe schimbare, discurile de discuri eliberează aditivul mineral așezat în partea inferioară a mașinii.
Atunci când se curăță cerealele în triere, deșeurile nu trebuie să conțină mai mult de 5% din cerealele din KLT curățate prin raportul lor cu masa deșeurilor.
Funcționarea tabelelor de sortare pneumatice
Curățarea lotului de cereale se face după ajustarea și ajustarea preliminară a mașinii, ajustând panta planului de divizare în direcțiile transversale și longitudinale, în care întregul plan de divizare trebuie să fie acoperit cu un strat uniform de grâu. Deschiderea porților de evacuare și alimentarea cu cereale în planul de divizare sunt ajustate astfel încât grosimea stratului de granule pe ea să fie de aproximativ 2-3 cm.
Articole similare
Trimiteți-le prietenilor: