Echipamente montate și reparate pentru verificarea calității lucrărilor de reparații și instalări care fac obiectul testelor individuale: inerți (mașini, mecanisme și dispozitive cu unitate); pe densitate și putere (capacitate și aparat).
Partea de sus a testelor individuale care urmează să fie finalizate lucrări de construcții civile, acțiunile executate prevăzute norme de siguranță prevăzute de alimentare cu energie electrică, apă, abur, aer comprimat, iar lucrul terminat pe salubrizarea aparatelor și a sistemului de protecție (împământare și celălalt). Testarea individuală a echipamentului în gol se realizează pe baza unui program special, cu participarea unui reprezentant al clientului și a unor organizații specializate de reparații și instalare.
Rezultatele testării echipamentului inactiv și a densității și rezistenței sunt formalizate prin acte speciale.
Principalele tipuri de aparate de testare pentru rezistență și densitate sunt testele hidraulice și pneumatice (Figura 11.1).
Înainte de a efectua aceste teste, este necesar să umeziți toate racordurile și trapele care nu sunt conectate la racordul la pompa de test. La efectuarea unui test hidraulic, în partea superioară a aparatului se montează un aerisitor și un manometru, iar conductele de alimentare cu apă și drenaj sunt conectate la aparat. Apoi, aparatul este umplut cu apă, eliberând complet aerul și închizând aerisirea. Al doilea manometru este amplasat lângă pompă pentru monitorizare. După aceasta, pompa este ridicată la presiunea de lucru și apoi la test. Presiunea de încercare este menținută timp de 10 minute, după care presiunea este redusă la presiunea de lucru, menținută pentru timpul necesar pentru inspectarea îmbinărilor și a compușilor de etanșare (tabelul 11.1). Când este vizualizat sub presiune de lucru, este permisă atingerea îmbinărilor sudate și nituite ale aparatului cu un ciocan care cântărește între 0,5 și 1,5 kg, în funcție de grosimea peretelui.
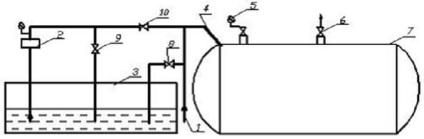
Fig. 11.1. Verificarea hidraulică a aparatului pentru rezistență:
1 - conducta de alimentare cu apă; 2 - pompa; 3 - un rezervor pentru pompă; 4 - conducte pentru umplerea aparatului cu apă; 5 - manometru cu macara cu trei căi; 6 - aerisire; 7 - aparate de testare; 8 - supapă pentru umplerea rezervorului cu apă; 9 - supapă pentru reducerea presiunii în aparat; 10 - supapă de închidere
La crimparea hidraulică a aparatelor cu coloane înalte, trebuie luată în considerare coloana hidrostatică a apei sub presiune; prin urmare, înainte de verificarea pasaportului sau a calculului, se verifică valabilitatea încercării hidraulice în poziția de lucru. Aceasta poate fi efectuată dacă sarcina de pe peretele curelei inferioare a aparatului de la suma presiunii de încercare și presiunea din coloană a lichidului nu depășește 0,8 din valoarea rezistenței la încovoiere a metalului carcasei la temperatura de criptare.
Tabelul 11.1. Presiunea de încercare pentru testarea hidraulică a dispozitivelor sudate
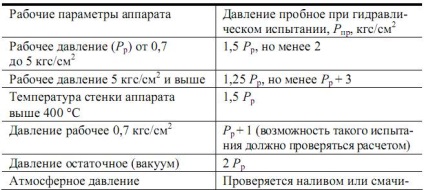
În cazurile în care aceste condiții nu sunt îndeplinite sau nu există pericolul de a supraîncărca fundației mașinii, și rezoluția în prezența unui inspector poate efectua turnarea Gosgortechnadzor aer pe coloană sau gaz inert.
La testarea îmbinărilor sudate ale aparatelor care funcționează sub presiune atmosferică, umezirea sudurilor cu kerosen, timpul de menținere pentru încercare este dat în tabelul. 11.2.
Tabelul 11.2. Timpul de menținere a aparatelor de testare cu kerosen
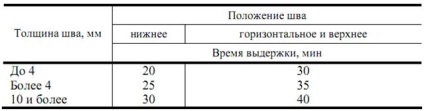
Urmați aspectul petelor de pe cusătura spate (de obicei externă) a cusăturii. După terminarea presării hidraulice, este necesar să deschideți robinetul de aer înainte de a scurge apa din aparat. Aceasta protejează dispozitivul de deformarea carcasei, în legătură cu crearea unui vid în interiorul dispozitivului.
Cele mai periculoase sunt testele pneumatice, deoarece, în caz de încălcare a integrității peretelui aparatului, se poate forma un val de șoc de aer. Trebuie avut în vedere faptul că testele de rezistență pneumatică nu pot fi efectuate în atelierele existente, pe trepte și în canalele unde sunt amplasate conductele de lucru.
Testarea pneumatică este cea mai convenabilă pentru a efectua utilizarea unui sistem central. Uneori, acestea trebuie efectuate cu ajutorul compresoarelor mobile. Compresorul trebuie să aibă un receptor și să fie amplasat de la echipamentul testat la o distanță de cel puțin 10 m. Creșterea și scăderea presiunii se realizează fără probleme și încet. După o expunere adecvată, presiunea este redusă la valoarea de funcționare, iar echipamentul testat este supus unei examinări aprofundate (Tabelul 11.3). Inspectarea și evaluarea în timpul creșterii sau scăderii presiunii nu sunt permise. Eliminarea defectelor în echipamente se efectuează după eliberarea presiunii. Numărul de persoane angajate în proces ar trebui să fie minim.
Tabelul 11.3. Mod de testare pneumatică
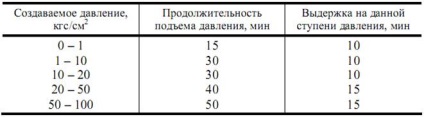
Testul pneumatic se efectuează în cazurile în care pot exista o suprasarcină pe suportul mașinii, sau fundație și rezoluția și în prezența unui aparat de formare inspector Gosgortechnadzor poate produce aer sau gaz inert. Împingerea pneumatică este de asemenea utilizată atunci când prezența apei în aparat poate cauza un accident în condițiile procesului tehnologic atunci când acesta părăsește modul de funcționare.
Împingerea pneumatică necesită și precauții speciale. În special, înainte de îndoirea cu aer, este necesar să se asigure că nu există lichide, vapori și gaze explozive și inflamabile în aparat. Pentru a face acest lucru, dispozitivul este curățat anterior cu un gaz inert sau cu abur. Dispozitivul, sub presiunea aerului, nu poate fi lipit; Cusăturile de sudură sunt lipite înainte de începerea crimpării. În momentul creșterii presiunii, este interzisă staționarea în apropierea aparatului.
Coloanele de vid sunt supuse unui test hidraulic pentru o presiune de încercare de 0,2 MPa sau un test pneumatic pentru o presiune de 0,11 MPa. Aparatele care funcționează la presiune atmosferică, de regulă, sunt supuse unui test prin turnarea apei. La temperatură negativă, adică mediu, testele hidraulice ale aparatelor sunt efectuate prin aplicarea încălzirii cu abur cu apă sau soluții apoase speciale având un punct de îngheț scăzut. De obicei, în aceste scopuri, se utilizează soluții de clorură de calciu sau clorură de sodiu (sare comuna). După testare, aparatul trebuie clătit cu apă caldă.
11.2. Mașini și mecanisme de spargere
Mașinile, mecanismele și aparatele cu agitatoare se execută în conformitate cu indicarea proiectului, a condițiilor tehnice sau a instrucțiunilor din capitolele relevante ale SNiP. Durata testării mecanismelor care se efectuează ar trebui să corespundă celei prezentate în tabelul. 11.4.
Tabelul 11.4. Durata mecanismelor de testare
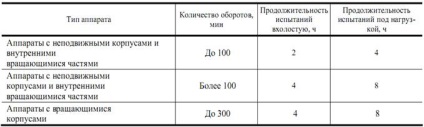
Testarea individuală a mașinilor și a mecanismelor se efectuează pe baza unui program special, cu participarea reprezentantului clientului și a organizațiilor specializate de reparații și instalare. Rezultatele echipamentului de testare sunt formalizate prin acte speciale.
Atunci când testarea este inactivă la început, fiecare mașină este supusă unei încercări de încercare, în care se efectuează ajustarea și reglarea interacțiunii părților și ansamblurilor sale la ralanti. Apoi, mașina este testată cu o încărcătură crescătoare treptată, verificând în același timp conformitatea caracteristicilor sale reale cu normele specificate în pașaportul, specificațiile sau standardele vehiculului.
Înainte de o încercare a mașinii, trebuie să:
1) verificați poziția și fixarea corectă a pieselor și componentelor care alcătuiesc utilajul, precum și pentru mașinile automate - și acțiunea corpurilor de lucru în conformitate cu diagrama;
2) dispozitive de lubrifiere pentru curățare și unsoare și cartușe de ulei cu lubrifiere corespunzătoare;
3) înainte de a începe pentru a defila lumină și mașină de mediu manual sau cu un mecanism special de restricționare a motorului deconectat de la un ciclu de lucru pentru a verifica dacă există blocaje locale, atinge piesele mașinii în mișcare între ele și cu obiectele din jur; verificați valoarea mișcărilor locale și a nodurilor corespunzătoare mișcării cu mișcare alternativă; în acest scop piesele sunt agitate manual, iar în mecanisme precise, mișcările moarte sunt măsurate cu instrumente speciale;
4) instalați și verificați toate gardurile, dispozitivele de tensiune și de siguranță, dispozitivele de încălzire, releele, întreruptoarele, etc;
5) pentru a face prima pornire a mașinii de ralanti cu eliberarea ei de orice sarcină, avertizând personalul de reparații și instalare despre pornirea mașinii;
6) pentru a face pornirea inițială a mașinii cu incluziuni scurte și, în cazul în care constată deficiențe semnificative de reparație sau de instalare, opriți-o imediat; Mașinile de pornire cu un dispozitiv de comandă a vitezei trebuie pornite de la cea mai mică frecvență;
7) pentru rularea mașinilor și a mecanismelor, este necesar să se verifice direcția de rotație a motorului deconectat de la mecanism și să se pornească motorul timp de 40 până la 60 de minute.
Atunci când mașina sau mașina se află în ralanti, se dezvăluie: natura generală a muncii (calm, fără răsturnare, lovituri și vibrații); încălzirea lagărelor, ghidurilor și a altor părți de frecare; baterea arborilor, scripeti, roti dintate; Stabilirea corectă a scaunelor pe arborele cuplajelor, scripeților, uneltelor, rulmenților; corespondența dintre direcția de rotație și numărul de rotații conform datelor pașaportului.
Aceste cerințe de bază, comune diferitelor tipuri de mașini, pot fi completate de cerințe tehnice speciale referitoare la această mașină și specificate în documentația tehnică.
După sfârșitul mașina se oprește de rulare, dezvăluie rulmenți și alte componente de fricțiune, precum și locuri cu decalaje minime între piesele în mișcare și staționare și verificați dacă există urme de frecare, scuffing. Defectele detectate sunt eliminate, aparatul este colectat și reglat, după care este supus unor teste tehnice. În acest scop, mașina este inclusă în lucrul cu încărcătura de proiectare completă, la atingerea căreia sunt verificați principalele indicatoare de performanță ale mașinii: productivitatea, calitatea produsului etc.
Acceptarea echipamentelor din reparații se efectuează în două etape - preliminare și finale. Mașină de pre (unitate), după repararea ia comisie formată reprezentative mecanici de conducere OGM echipa de reparații reprezentative efectuarea de reparații de reglare care deservesc această mașină (unitate), prin inspecție și testare de mers în gol. În final, mașina (ansamblul) are aceeași comandă după încercarea la încărcare în condițiile de producție.
Pentru fiecare tip de reparație se stabilește perioada de încercare a mașinii (unității) sub sarcină; reparații curente - 8 ore, capital - 24 de ore.
Acceptarea echipamentelor din reparații este formalizată printr-un act de acceptare și livrare a echipamentului, aprobat de inginerul șef al întreprinderii. În cazul în care reparația se realizează în condiții de calitate proastă, echipa de reparații care efectuează reparații este obligată să elimine defectele detectate.
Articole similare
-
Inspecția și testarea echipamentelor după reparații - manualul chimic 21
-
Repararea echipamentelor de gaz în ramblee, prețul serviciilor de diagnosticare, instalare și
Trimiteți-le prietenilor: