Pe baza vitezei de tăiere găsite, numărul estimat de rotații ale axului (rpm) este determinat de formula:
unde D este diametrul piesei de lucru, mm.
Apoi alegeți cel mai apropiat număr de rotații mai mici sau egale ale mașinii n, conform pașaportului mașinii. Numărul de rotații ale mașinii depinde de numărul de turații: pentru modelul de strângere cu șurub modelul 1K62 este determinat în figura 4.1.
Figura 4.1 - Schimbarea graficului mașinii de tăiat prin șuruburi
Determinați viteza reală de tăiere
unde este viteza reală de tăiere, m / min.
În calculele suplimentare, utilizați viteza reală de tăiere și numărul de rotații conform pașaportului mașinii.
Forța de tăiere P (H) este de obicei descompusă în componente de forță direcționate de-a lungul axelor mașinii (tangențial Pz radial Py și axial Px).
Componentele forței de tăiere sunt calculate prin formula:
unde este un coeficient care ține cont de materialul care trebuie prelucrat și de materialul sculei de tăiere;
- adâncime de tăiere, mm;
- viteza reală de tăiere, m / min;
x. , n - exponenți.
În practică, calculul este efectuat pentru componenta tangențială a forței de tăiere, care are cea mai mare valoare. Valorile coeficientului Cp și exponenții puterii lui x. . n pentru componenta tangențială a forței de tăiere PZ sunt prezentate în tabelul 4.4.
Tabelul 4.4 - Valorile coeficientului și exponenților
în formula pentru determinarea forței de tăiere tangențială PZ la
strunjire longitudinală exterioară
Puterea de tăiere N (kW) se calculează prin formula:
Determinați puterea necesară a motorului electric al mașinii
unde - puterea motorului electric al mașinii, kW;
- eficiența mașinii de acționare, care este în intervalul de la 0,8 la 0,9.
Dacă se dovedește că puterea necesară pentru pornirea motorului depășește masina de putere (mașină pentru 1K62 putere elektrodvigakVt), reduce valoarea forței de tăiere, prin creșterea fluxului și pentru a reduce adâncimea de tăiere, și un calcul cu noii parametri.
Determinați cuplul. necesare pentru procesul de tăiere
Determinați cuplul pe ax
Comparați valorile cuplului furnizate de mașină cu cuplul necesar tăierii. Dacă valoarea lui Mk. Art. <Мк..р. то необходимо уменьшить силу резания. Целесообразно уменьшать силу резания за счет увеличения подачи и уменьшения глубины резания, соблюдая условие
Timpul principal (tehnologic) (min) este determinat de formula
unde este lungimea calculată a suprafeței tratate, mm;
5 CONCEPTUL TEHNOLOGIEI CONSTRUCȚIEI
Proiectarea tehnologică a produsului este o caracteristică complexă complexă, care este estimată prin indicatorii tehnici și economici ai unei anumite metode de fabricare a acestei părți. Cei mai importanți indicatori sunt consumul material, intensitatea forței de muncă și costul de producție [9, 13]. De obicei, compara două sau mai multe părți de opțiuni de producție, ținând seama de condițiile specifice de producție: - tipul de producție unice sau de serie, disponibilitatea bazei de producție - turnare, zone de sudura, zone de prelucrare, etc ...
Piese de oțel și fontă, ștanțare și diferite profile de rulare sunt utilizate ca semifabricate. Pentru o singură producție se recomandă să se producă semifabricate și obiecte prin metoda turnării sub formă unică sau prin sudarea de semifabricate din produse laminate. Pentru producția în masă și pentru producția în masă, este cel mai eficient să se utilizeze un tratament sub presiune, mărind în același timp reproductibilitatea dimensiunilor acelorași părți și creșterea productivității.
Pentru a estima consumul de material al materialului, se folosește factorul de utilizare al materialului, care arată cât de mult material din țaglă este utilizat în piesă și se calculează cu formula:
unde mdet este masa piesei conform desenului, kg;
mzag este masa de țaglă, kg.
Valoarea acestui raport este în intervalul de la 0 la 1. mai aproape de valoarea 1, cu atât mai eficient materialul utilizat în articol (cu alte cuvinte, mai puțin material a intrat în jetoane). Cea mai mare valoare a factorului de utilizare a materialului (aproximativ 1) furnizează metode de formare, fără prelucrare ulterioară, piesa de prelucrat atunci când volum egal cu volumul piesei finite. La utilizarea laminate pentru fabricarea diferitelor componente pentru mașini unelte pentru prelucrarea resturilor constituie 10 la 40%, în timp ce rata de utilizare a materialului este 0.6-0.9, ceea ce înseamnă că utilizarea rațională a materialului. În fabricarea pieselor turnate cu prelucrare ulterioară prin tăierea valorii Kisp. în general, mai mici decât atunci când se utilizează semifabricate laminate și, mai mult decât atât, materialul consumat în sistemul alergător, care pot fi neglijate, deoarece sprues topit și a revenit la următoarea umplere. Fabricarea produselor prin sudare asigură o rată de utilizare ridicată a materialului.
Cu toate acestea, valoarea factorului de utilizare a materialului nu permite estimarea laboriosității metodei de fabricare alese. Pentru evaluarea obiectivă, se calculează costul fiecărei opțiuni de fabricație selectate. O estimare aproximativa aproximativa a intrarii de forta de munca poate fi facuta prin numarul unitatilor de echipamente sau a locurilor implicate in fabricarea acestui produs.
Atunci când se compară variantele, trebuie considerate cele mai preferate metode de fabricare în care valoarea factorului de utilizare a materialelor este de aproximativ 0,7 și mai mare, este necesar echipament pentru prelucrarea și echipamentele de sudare. deoarece aceste parcele sunt disponibile în aproape fiecare producție. De obicei, tratamentul sub presiune oferă o valoare mai mare a ratei de utilizare a materialului, dar necesită crearea unor matrițe speciale scumpe. Prin urmare, în absența unei secțiuni de tratare a presiunii la locul de producție sau a matrițelor gata preparate, această metodă ar trebui să fie preferată față de o turnare într-o singură matriță.
6 EXEMPLU DE CALCUL DIMENSIUNILOR DE FORMARE ȘI SELECȚIE
METODA RĂCIANTĂ A DETALIILOR DE FABRICAȚIE
Sarcină. Figura 6.1 prezintă desenul piesei finite și proiecția axonometrică a acesteia. Materialul piesei este St 3 (oțel cu conținut redus de carbon). necesită:
a) selectați toleranțele pentru prelucrarea și calcularea dimensiunilor piesei de prelucrat pentru a obține piesa prezentată în figură prin turnare; Selectați poziția turnării în matriță; calculează elementele sistemului sprue;
b) să calculeze dimensiunile și să selecteze piesele de prelucrat pentru producerea părții indicate în figură prin metoda tratamentului sub presiune;
c) selectarea semifabricatelor pentru fabricarea piesei prezentate în figură prin metoda de sudare;
d) se calculează modurile de tăiere pentru suprafața specificată în timpul răsucirii, luând în considerare admisia pentru prelucrarea din (a);
e) să evalueze parametrii tehnici și economici ai fabricației piesei descrise în figură, folosind turnarea, sudarea, presiunea și tăierea și să aleagă metoda cea mai rațională.
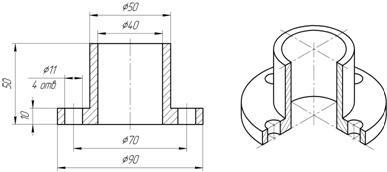
Figura 6.1 - Montaj
6.1 Selectarea cotelor, calculul dimensiunilor turnării
și parametrii sistemului de poartă
Acest semifabricat poate fi turnat în pământ, în scopul economisirii de metal pentru a crea o gaură centrală Ø40, se recomandă utilizarea unei tije, iar găurile de fixare pentru șuruburile Ø11 sunt realizate prin găurire. Deoarece turnarea nu asigură precizia dorită a dimensiunilor și curățenia suprafețelor, turnarea după curățare trebuie să fie prelucrată pe un strung, în acest scop fiind necesar să se permită alocarea tuturor suprafețelor care trebuie tratate.
În scopul certificatelor trebuie să selecteze poziția de turnare în forma și suprafața de separație a recomandărilor prezentate în literatura de specialitate [4] și secțiunea 1. Acest element are o configurație simplă și poate fi orice poziție (de exemplu, așa cum se arată în figura 6.1, întregul detaliul este plasat într-o jumătate de mucegai). Pentru părți simetrice ale suprafeței corpului conector tip revoluție se recomandă plasarea de-a lungul axei de simetrie - cu modelarea necesită doar un singur model care reprezintă jumătate din piesa turnată.
Suprafața conectorului trebuie să fie orizontală, astfel încât partea din formă să fie localizată, așa cum se arată în figura 6.2.
Alegem cote pentru prelucrarea pentru oțeluri în conformitate cu tabelul 1.2:
- în dimensiune diametrală Ø40 suprafețe, Ø50 și Ø90, care sunt aranjate prin turnarea de sus, laterală și inferioară, să ia cea mai mare alocație simetrică - 3,5 mm (care este pe alocația Ø40 interior);
- pe suprafețele de capăt ale părților situate la turnarea din lateral, acceptăm toleranțe de 3 mm.
Pentru a putea extrage modelul fără a distruge matrița, este necesar să asigurăm pante de turnare pe suprafețele verticale ale turnării. Prin recomandările pe care le luăm pentru capetele Ø57 și Ø97 o pantă de 0 ° 45 '. Conform recomandărilor pentru a preveni apariția solicitărilor interne, este necesară o tranziție lină de la un perete gros la unul subțire, în acest scop realizăm o pantă și o rază de rotunjire R3 a două suprafețe perpendiculare.
Schița piesei de prelucrat cu toleranțe, poziția turnării în matriță și suprafața conectorului matriței sunt prezentate în figura 6.2.
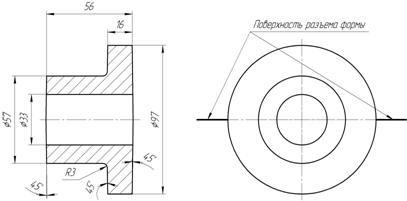
Figura 6.2 - Schița piesei de prelucrat și poziția turnării în matriță
Conform schiței, determinăm volumul și masa turnării.
Pentru a determina volumul, turnarea ar trebui să fie defalcată în figuri elementare geometrice (în cazul nostru - butelii). Atunci când se calculează volumul prin pantele și razele de rotunjire, neglijăm din cauza valorii mici a volumului acestor componente.
unde V1. V2. V3 - simboluri pentru volumele cilindrilor Ø57, Ø97
și, respectiv, Ø33.
Greutatea turnării este determinată de expresia:
unde # 961; - densitatea metalului turnat, determinată prin referință. (Pentru oțel # 961; = 7800 kg / m3, pentru fontă # 961; = 7000 kg / m3).
Vom calcula elementele sistemului de poartă [4].
Masa de turnare cu litri și profituri este determinată prin recomandări, deoarece dimensiunile exacte ale acestor elemente sunt încă necunoscute. Conform recomandărilor (a se vedea 1.1), greutatea sistemului de turnare din oțel este cuprinsă între 60 și 80% din masa turnării. Acceptăm 70%. apoi:
Greutatea de turnare cu sistemul de închidere
Lungimea umpluturii formei este determinată de formula (1.6).
Coeficientul este luat egal cu 1,5.
Grosimea medie a pereților turnării = (57-33) / 2 = 12 (mm).
Se determină secțiunea transversală totală a alimentatoarelor prin formula (1.7)
Coeficientul de corecție pentru fluiditatea pentru oțelurile cu conținut scăzut de carbon este de 0,97.
Coeficientul de turnare viteza de turnare este determinată densitatea relativă. Formularul Cilindree determină provizoriu o distanță admisibilă prestabilită pentru masa de turnare la 5 kg de modele de top la partea superioară a vasului la 40 mm de la partea inferioară a modelului la fundul balon - 40 mm, de la modelul la pereții vasului - 30 mm. atunci
Secțiunea transversală a alimentatoarelor este
Zona elementelor rămase ale sistemului poartă este determinată din relația (1.5):
Secțiunea de secțiune a dispozitivului de captare a zgurei
Suprafața secțiunii transversale a șinei (mm2).
6.2 Calcularea și selectarea semifabricatelor pentru fabricarea pieselor
metoda de tratare prin presiune
Se determină toleranțele pentru prelucrarea piesei obținute prin tratarea sub presiune [9]. Aproximativ, valorile cotelor pentru prelucrarea suprafețelor cilindrice exterioare sunt selectate conform tabelului 2.1, pentru finisarea capetelor - conform tabelului 2.2. Valorile cotelor vor fi: 4 mm pentru Ø50 cu o lungime de 40 mm, 5,5 mm pentru Ø90 cu o lungime de 10 mm; pe suprafețele de capăt, adaosul este de 0,8 mm la Ø90, 0,7 mm la Ø50.
Având în vedere cotele, determinăm dimensiunile exterioare ale piesei de lucru:
diametre 50 + 4 = 54 (mm); 90 + 5,5 = 95,5 (mm);
lungime 10 + 0,8 + 0,8 = 11,6 (mm); 50 + 0,8 + 0,7 = 51,5 (mm).
Alegerea semifabricatului pentru ștanțare se va face luând în considerare dimensiunile obținute din seria standard de oțel rotund format la rece (a se vedea tabelul 2.3). Tija cea mai potrivită este un diametru de 55 mm și 95 mm.
Pentru o alegere rezonabilă de semifabricate, să luăm în considerare căile posibile de fabricare a detaliilor prezentate în figura 6.1 din produse lungi:
1) ca semifabricatul poate selecta tija 95 mm în diametru (cu tăiere adaosuri de prelucrare) suprafața exterioară strung pisa la dimensiuni predeterminate, găuriți gaura interioară și dalta-l la un diametru de 40 mm, apoi foraj mașină pentru a efectua cele 4 găuri cu un diametru de 11 mm;
2) ca diametrul tijei de preforme poate fi ales de 55 mm, să îndeplinească aterizare sa de a forma o îngroșare de 95 mm diametru local și o înălțime predeterminată pentru a face cote pentru transformarea strungului, centrale fabricarea alezaj și găurile de bolț, ca în metoda anterioară;
3) să efectueze un diametru tijă preforme aterizare de 55 mm, ca în metoda anterioară, apoi - orificiul central firmware 40 mm diametru, urmată de tratarea suprafețelor exterioare pe un strung și care produc orificiile șuruburilor în burghiului.
Atunci când analizează metodele propuse de piese de fabricație prin utilizarea unui tratament de presiune, observăm următoarele. Prima metodă este cea mai simplă pentru a efectua și distribuite în practică necesită doar porțiunea de prelucrare (strung și mașină de găurit). Cu toate acestea, cea mai mare parte a metalului în timpul acestei merge în chips-uri, t. E. Va fi factor redus de utilizare a materialului. A doua metodă deasupra primei porțiuni necesită în plus prezența de lucru la cald și crearea unei ștampile, dar are un material mai mare de utilizare. A treia metodă are cel mai mare factor de utilizare a materialului, dar necesită adăugarea la prima și a doua operație EEPROM închisă, ceea ce complică procesul de fabricație și crește costul unei singure piese având o grosime a peretelui subțire de 5 mm.
Astfel, cel mai simplu și cel mai rațional mod de a alege al doilea tratament de presiune, adică. E. Aterizare Diametrul spațiu liber de 55 mm la un diametru de 95,5 mm, urmată de prelucrare și de foraj o gaură centrală. Schița piesei care rezultă din debarcarea, este prezentată în figura 6.3.
Pentru a efectua această metodă, este necesar să se determine volumul și lungimea părții plantate a piesei de prelucrat [16].
Volumul părții plantate a țaglei este determinat de formula (2.2):
în care volumul forjării este determinat de schiță:
Volumul de contracție este considerat egal cu 1,5%, adică,
Pierdere de metal pentru monoxidul de carbon în timpul încălzirii electrice de 0,5% din volumul ghilotinei:
Luând în considerare contracția și fumul, care nu prevăd o retragere la oblak, determinați volumul părții plantate a țaglei:
Articole similare
Trimiteți-le prietenilor: