De la lansarea și începutul utilizării controlorilor logici programabili (PLC) ca dispozitiv de înlocuire a releelor, utilizarea controlorilor mici, autonomi pentru automatizarea proceselor a devenit larg răspândită și a schimbat aspectul și chiar arhitectura sistemelor de monitorizare în sine. Dezvoltarea computerelor personale (PC) și transformarea lor evolutivă într-un dispozitiv universal de monitorizare a transformat controlerele logice programabile (PLC) într-o categorie de sisteme de control mai mici și mai simple. În prezent, puteți găsi diferite forme de calculatoare: controlori, emițătoare și dispozitive încorporate, controale industriale, computere industriale și chiar dispozitive mobile în mediul industrial.
Evoluția controlerului de automatizare
După ceva timp, controlere logice programabile (PLC) au devenit mai mult din puterea lor de calcul și de memorie sunt crescute, opțiunile de configurare pentru I / O, canale a crescut, ceea ce a făcut în cele din urmă posibilă pentru a efectua operații matematice în blocuri funcționale în loc de programarea releului utilizat anterior.
Se credea că sistemul cu mai multe etape poate fi tradus cu ușurință într-un limbaj de programare care simulează circuite de releu-contact pe care fiecare electrician le poate citi. Câțiva ani mai târziu, au fost stabilite cerințe suplimentare pentru controlerii logici programabili de bază (PLC), prevăzuți în standardul IEC 61131-3, care descrie limbile de programare pentru controlerele logice programabile. Din păcate, versiunile standardului 61131-3 ale majorității furnizorilor nu sunt interschimbabile și nu pot interacționa unul cu celălalt.
În acest sens, utilizarea de controlere logice programabile (PLC) pentru astfel de algoritmi de control complexe și avansate drept control PID este restricționat, ceea ce face dificil de a transfera programe de la un brand controler logic programabil (PLC) controlerului de un alt brand.
La începutul anilor 1980. ca un dispozitiv de calcul de uz general a fost dezvoltat de un mic calculator „personal“, care este planificat pentru a face low-cost și la prețuri accesibile pentru toată lumea și, în același timp, este suficient de puternic pentru a fi utilizate pentru astfel de proiecte de calcul de înaltă performanță, cum ar fi foi de calcul, care tocmai a apărut.
După ce IBM a lansat IBM PC, ubicuitatea "calculatorului personal" a fost predeterminată. În primele zile ale PC-ului furnizori independenți de software a început să producă add-in card de date de intrare-ieșire și software-ul pentru achiziția de date. Computerele au reușit să efectueze colectarea de date de mare viteză, ceea ce a permis utilizarea PC-ului în laborator. Cel mai vechi produs de software, computerul lumea anterioară Windows, a fost „Software Wedge“ Compania TAL, care a fost proiectat pentru a colecta date de la orice dispozitiv I / O și punerea lor într-o foaie de calcul (mai întâi în VisiCalc, apoi SuperCalc și în cele din urmă în Excel)
Problema a fost că PC-ul nu a fost conceput pentru uz industrial în fabrică sau fabrică. Avea o carcasă detașabilă, deschideri de ventilare pentru răcire și un ventilator deschis. Un astfel de dispozitiv PC a făcut viața sa de proiectare în condiții industriale scurte.
Desigur, acest lucru a condus la reambalarea imediată a PC-ului într-o locuință mai robustă, utilizarea specificațiilor militare și producerea de plăci cu un interval de temperatură mai ridicat. Una dintre primele utilizări ale unor astfel de computere industriale a fost colectarea de date de mare viteză pentru industria aerospațială, dispozitivele de control al mișcării și sistemele de vizionare pe calculator.
Ca urmare, costul economiei de scară, calculatoare industriale au devenit este semnificativ mai mic, iar dezvoltatorii de platou au calculatoare cu placă audio, cunoscut sub numele de controlere embedded cu dispozitive de intrare / ieșire, memorie, o unitate centrală de procesare (CPU) și un sistem de operare (OS) într-o constantă memorie (ROM). Astfel de dispozitive au început să fie utilizate într-o varietate largă de comenzi mecanizate, de la centrale industriale CNC / CNC în fabrici pentru a controla unitățile de refrigerare și mașinile de spălat.
Controale programabile pentru automatizarea proceselor de producție Rezicon combină caracteristicile unui PC industrial bazat pe un PC cu capacitățile de management inerente unui controler logic programabil convențional (PLC) (fig. 1). El a menționat că un controler programabil pentru automatizarea proceselor de producție (PAC) ar trebui să combine fiabilitatea unui controler logic programabil (PLC), puterea de procesare și software-ul disponibil pe piață, precum și capacitățile software-ului sistemului de operare și PC.
In prezent, automate programabile pentru automatizarea proceselor (PAC-uri) sunt utilizate pentru controlul proceselor de producție, de colectare a datelor, monitorizare la distanță, viziune mașină și de control al mișcării (fig. 2). Deoarece automatele programabile pentru automatizarea proceselor (PAC-uri) sunt versiunea PC de destinație specială, acestea au aceeași built-in conectivitate la rețele, cum ar fi Ethernet la caracteristicile desktop. Cele mai multe controllere programabile PAC a integrat caracteristici pentru un astfel de standard de protocoale de interfață de rețea, cum ar fi TCP / IP, SMTP și protocol de comunicare Microsoft, tehnologia Object Linking and Embedding OLE pentru controlul procesului, prescurtat ca OPC (facilități de legare și includ pentru Process Control) . Controleri de programare PAC poate integra o mulțime de protocoale de rețea depășite industriale, cum ar fi Modbus, RS232 / 422, RS485, CANbus, DeviceNet, Profibus, Fieldbus Foundation, si altele, bazate pe rețele Ethernet standard, cu fir sau fără fir.
Controleri de programare pentru producere automatizată (PAC-uri) poate funcționa ca un cu drepturi depline, noduri de calcul complexe într-o rețea distribuită, iar în această formă ar putea estompa linia dintre dispozitive de control programabile și dispozitive funcționale, cum ar fi controlere de câmp și terminale la distanță DCS SCADA (RTU).
Un controler PAC programabil convențional oferă:
• Funcționalitate în mai multe domenii, inclusiv gestionarea logică, continuă și de mișcare pe o singură platformă
• O arhitectură deschisă, modulară, cu standarde de comunicare universale acceptate, neautorizate de organizația de standardizare pentru interfețe sau protocoale de rețea
• O singură platformă de dezvoltare multidisciplinară care include etichetarea comună și o singură bază de date
• Software care permite proiectarea fluxurilor de proces pentru mai multe unități de echipament sau unități de proces
Comprimarea modelului de producție: Automatizarea devine mai ușoară.
Creșterea rapidă a capacităților controlorilor programabili pentru automatizarea proceselor de producție (PAC) a făcut posibilă compresia modelului standard de producție pe mai multe niveluri.
NIVELUL 5: Întreprindere
NIVELUL 4: Planificarea afacerii pentru producție și logistică
NIVELUL 3: Activități generale de producție și
NIVELUL 2: Lucrați într-o zonă separată de producție
NIVELUL 1: Controlul / siguranța de bază
NIVEL 0: Procesul de producție
Modelul inițial de producție Pedyu a avut cinci niveluri, începând cu procesul de producție la nivelul sistemului de întreprindere de afaceri. Progresele în instalațiile de producție și de gestionare la nivelul 1 atunci când combină controlori de câmp și sistemele de control distribuit, care au fost atribuite controlerului programabil PAC, au redus nivelurile 1, 2 și 3 la același nivel, lăsând nivelul de control al instalației și a operațiunilor și nivelul ERP ( Planificarea Resurselor Enterprise (Enterprise Resource Planning) / MES (Sistemul de Management al Producției), așa cum se arată în figura de mai jos. Controlul de bază și, în unele cazuri, chiar și un control critic de siguranță, interfața cu operatorul, precum și funcțiile de nivel superior HMI (operare „Machine Man») / SCADA (Supervisory Control și achiziție de date la) au fost integrate într-o singură platformă bazată pe controler programabil PAC .
"Comprimarea platformei de automatizare"
PAC: platformă unificată de management
Sistemul PAC include monitorizarea, prelucrarea informațiilor, precum și lucrul la rețea pe un singur controler. Deoarece controlerul PAC este un calculator industrial, stabilită pe baza caracteristicilor de proiectare ale controlerului logic programabil (PLC), are toate caracteristicile unui PC complet funcțional, inclusiv o memorie de mare, hard disk, sistem de operare, și, opțional, un procesor multicore. Indiferent dacă instalația este un sistem "batch", un sistem de producție continuă, un sistem hibrid; de control de mare viteză, a instalațiilor industriale sau sistem de computer vision, controlerul PAC prevede un sistem de control unic, care poate face față tuturor acestor provocări - și, în unele cazuri, mai multe sarcini simultan.
Controleri de programare PAC pot fi integrate în interfețele locale „Om-mașină» interfață (HMI) HMI sau un panou de afișaj local poate fi poziționat în apropierea instalației PAC. Programabil PAC poate funcționa ca un server de date mobile cu un sistem de gestionare a bazelor de date relaționale built-server care acceptă structurat SQL limbaj de interogare, și tehnologia de stocare a datelor, în acest caz, datele pot fi supuse unor pre-tratament utilizat pentru a controla controlerele PAC și transmise bazei de date Intreprinderilor . Următoarele reprezintă un exemplu de funcționalitate a manipulării datelor cu un controler PAC convențional:
Server mobil încorporat al sistemului SQL de gestionare a bazelor de date relaționale a controlerului programabil PAC
Rețineți că dispozitivul de programare conform standardului IEC 61131-3 este dispozitivul central care oferă caracteristici operaționale ale controlerului PAC - precum și alte standarde de comunicații universal acceptate și standarde deschise, cum ar fi OPC. Trebuie remarcat faptul că, cu serverul SQL încorporat, datele pot fi transferate în formatul de bază de date SQL direct de la controlerul PAC la baza de date Enterprise sau la MS Access pentru a efectua funcții locale de gestionare.
O problemă în controlerele PAC a fost întotdeauna lucrarea nedeterministă a Windows și a derivatelor acesteia, precum și Ethernet și derivatele sale. Advantech, de exemplu, a testat platforma controlerului PAC pentru posibilitatea de funcționare deterministă (în timp real) și a arătat că timpul de actualizare a datelor este de 1 ms pentru 32 module I / O digitale. Acest lucru confirmă faptul că utilizarea continuă a controlorilor PAC pentru colectarea de date de mare viteză, aplicațiile de gestionare a mișcării și viziunea pe computer, în care rata de actualizare a datelor este mai mică de 20 ms este foarte importantă pentru monitorizarea performanțelor.
Noi domenii de utilizare
Versatilitatea platformei controlerului PAC poate fi văzută clar în numărul mare de aplicații în care este utilizat - în producție și în afara industriilor tradiționale.
Integrarea Management, Interface „Machine Man» (HMI), funcția de procesare a informațiilor și crearea de rețele într-un sistem de control unic face posibilă utilizarea platformei în astfel de domenii disparate de aplicare, ca managementul a pompei de benzină (benzinărie), la o stație de gaz, un sistem GPS mobil pentru transportul rutier. platforma de testare automată a unităților individuale de echipamente electronice, inspecția produsului final, identificarea frecvenței radio (RFID) și chiar de gestionare a activelor, în plus față de utilizarea de controlere într-un sisteme discrete de control de fabricație tradiționale și.
În ramurile tradiționale ale industriei prelucrătoare, funcționalitatea largă a controlorilor PAC poate fi văzută atunci când se utilizează în sistemele de control ale procesului de amestecare a betonului. Înlocuirea controler programabil logic (PLC) și o arhitectură PC la o singură platformă industrială de control Advantech Apax PAC existent rezolvat toate problemele legate de transferul de date între programabil controler logic PLC (care este utilizat pentru comunicații de date seriale) și PC-uri industriale, care a folosit Ethernet. Acest lucru a permis ca programul de control SoftLogic și programul Interfață om-mașină (HMI) să funcționeze simultan în sistemul de control PAC integrat (fig. 6).
Software-ul de interfață HMI include o opțiune de setare a parametrilor, monitorizarea pornire / oprire și preluarea datelor de proces și o prezentare generală a funcționalității, în timp ce programul de control SoftLogic oferă o ponderare în timp real în timp real. În plus, utilizarea controlerului PAC permite utilizarea limbajului de programare a textului structurat pentru algoritmul de determinare a greutății în loc de logica lanțului sau de programarea blocurilor funcționale.
Controlerul PAC include o funcție de gestionare a datelor la distanță în timp real direct din centrul de control, utilizând standardul deschis al protocolului Modbus / TCP atunci când se utilizează standardul 100Mb Ethernet.
Este important ca în interior.
Controlerul PAC nu este doar un computer personal sau un computer cu o singură placă, plasat într-o incintă robustă. caracter
Procesul de automatizare de aplicații industriale, cum ar fi dozarea cimentului discutat mai sus, înseamnă că controlorii PAC trebuie să fie proiectate astfel încât să fie supuse unor standarde înalte de proiectare și de echipament decât un PC standard sau chiar un PC standard industrial. Caracteristici cum ar fi o abatere puternic de la modul standard, software-ul de rețea de filtrare, de protecție la supratensiune, protecția împotriva o oprire în cazul în care vă supraîncălzirea protecție împotriva unui opritor atunci când supracurent și protecție scurt-circuit sunt standard pentru controler PAC moderne, dar acestea nu pot fi incluse
în proiectul unic de bord adoptat. In timp ce controlerul PAC este mai mult multifuncțional decât un controler logic programabil (PLC), PAC controler de proiectare trebuie să îndeplinească standardul IEC-61131-2, tip 1 ... același standard design, care se aplică la controler PLC.
Controlerul modern PAC este, în general, mai fiabil decât controlerul PLC și, desigur, aparține unei clase comparabile cu PC-urile industriale și sistemele OEM cu o singură placă. Cu o certificare strictă ca controler PLC și având o arhitectură duală de comandă, o putere dublă de intrare și o funcție de redundanță a sistemului, controlerul este robust, durabil și are o mare funcționalitate.
Controlerul modern PAC are o topologie flexibilă. Aceasta înseamnă că arhitectura fizică deschisă permite extinderea nelimitată a funcțiilor I / O și a funcțiilor de control. Unele modele de controler PAC vă permit chiar modificarea și creșterea
procesorul central fără intervenția în modulele de intrare / ieșire și, pe de altă parte, permite înlocuirea la cald a modulelor I / O. Faptul că proiectarea controlorilor PAC se bazează pe un mic computer cu propunerea
Aceasta înseamnă că îmbunătățirea design mic calculator și să o doteze procesor mai rapid, o rată mai mare de transfer de date, capacitățile de calcul mai mare, mai multă memorie, proprietăți de economisire a energiei și așa mai departe. Permite o mai buna schimba controlere PAC, ceea ce le face controlere prezent și viitor.
Vizitatorii au citit de asemenea:
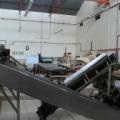
Seria de controlere Mitsubishi Electric MELSEC L este concepută pentru a rezolva sarcini de automatizare medie, pentru care resursele controlorilor de monobloc nu sunt suficiente, iar soluția de comandă modulară mare este costisitoare
Articole similare
-
Complexe robotizate (HPC) destinate procesului tehnologic de asamblare - abstract,
-
Complexe complexe complexe (HPC) destinate procesului tehnologic de asamblare
Trimiteți-le prietenilor: