SUDURA DE DIFUZARE ÎN VACUUM
Suflanta difuză se realizează în stare solidă a metalului la temperaturi ridicate, cu aplicarea unei forțe de strivire la locul de sudare.
Metoda a fost dezvoltată în anii '50 de către NF Kazakov (Premiul Lenin în 1984).
Legarea prin difuzie - un procedeu de preparare a unui compus din materiale monolitice datorită formării de legături la nivel atomic, cu cea mai apropiată abordare suprafețele de contact care rezultă în deformarea plastică locală și încălzire simultană, asigură difuzia reciprocă a atomilor în straturile superficiale ale materialelor fiind unite. (NF Kazakov)
Tehnologia materialului sudura prin difuzie a fost aplicată pentru mai mult de 850 de întreprinderi și institutele de cercetare științifică a țării, atunci când vă conectați mai mult de 750 de perechi, nu numai materiale omogene, dar diferite, coeficienții termici ai care sunt foarte diferite de la ei 630 - sunt dificil sau imposibil să se combine în alte moduri. Industria are mai mult de 860 de instalații specializate de sudură.
Acest mod poate fi implementat:
Sudarea pieselor bimetalice (fontă + oțel + fontă) pentru plăcuțele de frână și discurile de frecare.
Sudarea metalelor-ceramice cu metale (plăci cu cap de carbura cu suporturi pentru scule de tăiere).
Sudarea aluminiului cu alte metale: cupru, nichel, fonta, etc.
Sudarea pieselor din oțeluri și aliaje rezistente la căldură și titan unul cu celălalt.
Sudate metale diferite, cum ar fi titan și cupru, titan, Kovar, titan și platină, și sticlă Kovar, titan și compuși de molibden, care sunt imposibil de aplicat alte metode de sudură și lipire.
Suflanta prin difuzie este folosită în mod eficient în producția de masă și în producția de masă într-o serie de industrii: automobile, tractor, electrice, chimice,
Cu ajutorul sudurii prin difuziune în vid (DSW), sunt produse următoarele:
aparate pentru industria chimică, placate cu argint și cupru;
noduri diferite de cermete;
cilindri pentru cilindri de motor;
elemente de senzor elastice etc.
În cazul sudării prin difuziune, nu există emisii de energie radiantă, gaze, praf fin, adică procesul de sudare este ecologic, nu provoacă poluarea mediului.
vă permite să primiți semifabricate (piese) cu cantități minime de procesare a produsului, inclusiv configurație complexă;
vă permite să obțineți conexiuni de precizie care se potrivesc exact cu dimensiunile de proiectare specificate ale structurii;
asigură crearea unor structuri în care îmbinarea are toate proprietățile materiei prime, inclusiv forța.
Procesul de sudare prin difuziune în vid
Procesul de sudare a metalului în stare solidă la temperaturi ridicate se desfășoară în mod fundamental în același mod ca și în cazul sudării la rece.
Utilizarea temperaturilor ridicate în timpul sudării prin difuzie conduce la o scădere a rezistenței metalului la deformările plastice.
Îndepărtarea peliculelor de suprafață și prevenirea formării acestora în timpul sudării se realizează cu ajutorul protecției prin vid și prin curățarea preliminară a suprafețelor sudate.
La sudarea cu difuzie în vid, suprafața materialului este protejată nu numai de contaminare ulterioară, ci și purificată ca urmare a disocierii, sublimării și difuziei oxizilor.
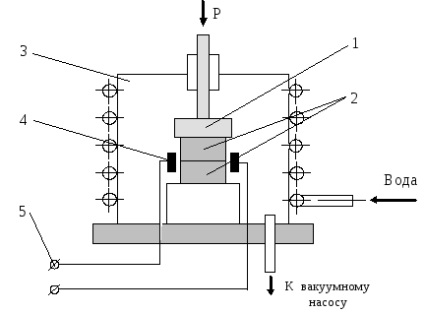
1-mecanism de compresie; 2-piese sudate; Cameră 3-vid;
4-încălzitoare; Sursă de 5 surse
Fig.1. Schema de sudura prin difuzie in vid
În procesul de sudură prin difuziune se pot distinge două etape consecutive:
Prima etapă a procesului de sudură prin difuzie se bazează pe formarea legăturilor metalice pe suprafețele metalice sudate atunci când sunt încălzite într-un vid cu ajutorul unei forțe de strivire.
A doua etapă este legată de procesele de difuzie reciprocă a atomilor metalelor sudate. Aceasta conduce la formarea de straturi intermediare, crescând rezistența îmbinării sudate.
În prezent, nodurile și piesele din diverse metale, aliaje și materiale nemetalice sunt fabricate prin sudură prin difuziune. Compozițiile de materiale sudate sunt extrem de diverse.
Sudarea are loc într-un vid de 10 -3 ¸ 10 -5 mm Hg. După evacuarea aerului din cameră, produsul este încălzit la temperatura de sudare.
Încălzirea pieselor se poate face prin metode diferite. Cele mai frecvent utilizate sunt:
Încălzirea prin radiație se realizează prin radiație dintr-un încălzitor amplasat în interiorul corpului camerei de vid. Particularitatea încălzire prin radiație, în care piesele sunt încălzite prin sursa externă de căldură, este posibilitatea de piese de încălzire realizate din orice material cum este bine-conductoare (metale și aliaje) și semiconductori și dielectrici.
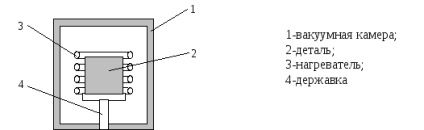
Fig.2. Diagrama de încălzire prin radiație a piesei
Încălzire electrică. În cazul încălzirii prin contact, încălzirea părților se produce datorită acțiunii termice a curentului electric care trece prin piesele înseși. În acest caz, eșantionul este conectat direct la o sursă de curent direct sau alternativ. Valoarea limită a temperaturii părții este limitată numai de posibilitatea topirii acesteia.
Încălzire prin inducție. În cazul încălzirii prin inducție, proba încălzită este plasată într-un câmp electromagnetic în schimbare rapidă, creat lângă conductor. Încălzirea se produce datorită căldurii generate în timpul circulației curenților turbionari induse în părți. Incalzirea prin inducție este cea mai des utilizată în instalațiile industriale.
Parametrii principali ai procesului DSW
Valorile acestora depind de proprietățile fizico-chimice și mecanice ale materialului, de starea suprafețelor îmbinate, de structura îmbinării sudate.
Temperatura de sudare trebuie să asigure o rată ridicată de deformare plastică și dezvoltarea proceselor de difuzie. Temperatura de sudare este determinată din relația: Tcb = 0,7 Tm (pentru aliajele de temperatură ridicată și oțelurile metalelor refractare poate fi oarecum mai mare).
Valoarea optimă a vidului este aleasă luând în considerare proprietățile materialelor care urmează să fie sudate și rezultatele studiilor. Cu vidul insuficient, oxidarea materialelor sudate crește. Vacuumul înalt reduce semnificativ productivitatea procesului, conduce la aprecierea acestuia.
Rezistența articulației (oțelul 45) crește în mod semnificativ până la un vid de 10-1 mm, cu o creștere suplimentară, rezistența este mărită la 10 -2 mm.rt.t. Creșterea suplimentară a debitului nu are un efect mare asupra rezistenței.
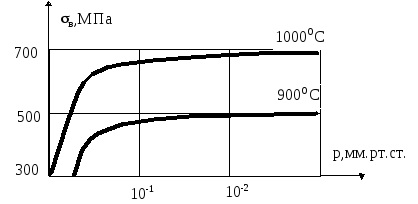
Figura 3. Graficul puterii conexiunii
de la gradul de vid într-o cameră de vid
S-a stabilit că gradul de vid în camera de vid este de 10 -2 ± 10 -5 mm.t.t.t., este foarte posibil să se asigure o curățenie a suprafețelor care trebuie îmbinate și să se obțină o conexiune uniformă.
Pentru a obține o îmbinare de bună calitate, este necesar să se asigure o încălzire uniformă a articolului sudat pe toată secțiunea.
Forța de compresie este aplicată după egalizarea temperaturii și este menținută constantă pe tot parcursul procesului.
Durata expunerii la presiune depinde de proprietățile materialului care trebuie sudat, presiunii și încălzirii și poate ajunge la zeci de minute.
Presiunea depinde, de asemenea, de proprietățile metalului, temperatura de sudare și variază în intervalul de 0,3-10 kgf / mm2 (3,100 MPa) pentru diferite materiale.
Efectul temperaturii asupra rezistenței unei îmbinări sudate a oțelului 50 la presiuni diferite poate fi reprezentat după cum urmează:
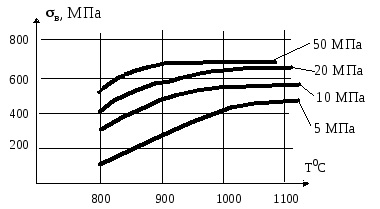
Figura 4. Graficul puterii conexiunii
de temperatură de sudare
Creșterea temperaturii cu o durată constantă de sudură și alte condiții egale mărește rezistența articulației.
Cu o creștere a duratei de sudare, rezistența îmbinării sudate crește la o valoare optimă, iar creșterea suplimentară practic nu afectează rezistența îmbinării sudate (figura 5).
Modalitățile de pregătire și prelucrare a suprafețelor pieselor sudate au o mare influență asupra rezistenței articulației în timpul sudării prin difuziune în vid. Cu cât este mai mare clasa de curățenie a suprafeței, cu atât este mai puternică legătura.
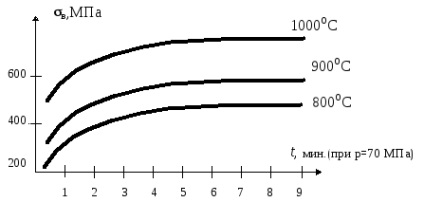
Figura 5. Graficul puterii conexiunii
de timp de sudare
Mașini de sudura pentru sudura prin difuzie
Instalațiile de sudare pentru DSV au următoarele componente:
Mecanismul presiunii (acționarea hidraulică).
Sistem de control de la distanță și control.
Sursa de încălzire a pieselor sudate
În prezent, industria noastră produce o serie de instalații pentru sudarea prin difuzie.
Problemele legate de sudarea cu difuzie a metalelor în vid sunt deja abordate la Moscova în Laboratorul de Cercetări al Problemelor de Sudură prin Difuziune în Vacuum (PNLLDSV). Dezvoltat peste 100 de tipuri de sisteme de sudură folosind diverse surse de sisteme de încălzire și de încărcare, inclusiv sTLDs-26 sTLDs-40 sTLDs-60, 70-sTLDs și colab., MAC-3, MAC-4.
Volumul producției de instalații industriale pentru instalația DSV la Uzina de echipamente de sudură Pskov Heavy Electric este de 20 ¸ 25 unități. pe an. Numărul de bază al instalațiilor de plante este produs independent de desene (PNLLDSV).
Au fost dezvoltate dispozitive cu încălzire prin radiație.
Tip UDS-1. Forța maximă aplicată este de 5 tone. Temperatura maximă de încălzire este de 1500 ° C. Instalarea funcționează pe principiul transferului energiei radiante a elementelor de încălzire a tungstenului pe piesele sudate situate în centrul spațiului de lucru. În UDS-1 este posibilă sudarea pieselor cu un diametru de până la 120 mm, cu o înălțime totală de până la 300 mm.
Există, de asemenea, un număr de SDU-3k, SDVU-4m, SDVU-7 și așa mai departe.
SDTU-6m (unitate de vacuum cu difuzie de sudură) cu dimensiuni ale camerei de lucru 250'250'280 mm. Instalația folosește încălzirea prin inducție. Este proiectat pentru sudura prin difuziune de niobiu, tungsten, molibden si alte metale refractare.
Pentru piese de sudură și dispozitive electronice folosind instalarea nodurilor A 306-04 care permite sudarea în vid și atmosferă controlată încălzite cu frecvență înaltă.
Camera de lucru: diametru 350 mm, înălțime 440 mm.
Compresie de până la 10 tone.
Temperatura maximă de încălzire este de 1300 ° C.
Presiunea reziduală este de 2 × 10 -4 mm.
Unitate imbunatatita A 306-06 - Aceasta cu două poziții pentru sudarea metalice si metaloceramice ansambluri dispozitive electronice. Instalația constă din două unități care funcționează independent una de cealaltă. Utilizarea a două camere permite creșterea productivității instalației, folosind coeficientul generatorului de înaltă frecvență.
Articole similare
Trimiteți-le prietenilor: