Amenajarea echipamentului.
3. Noțiunea de calibrare a rulourilor.
4. Calitatea produsului și deficiențele majore.
5. Perspectivele dezvoltării modului de producție.
6. Indicatori tehnici și economici.
Răcirea la rece, comparativ cu cea fierbinte, are două mari avantaje: în primul rând permite producerea de foi și benzi cu o grosime mai mică de 0,8-1 mm, până la câteva microni, care nu poate fi atinsă de laminarea la cald; în al doilea rând, asigură obținerea de produse de calitate superioară în toate privințele - precizia dimensională, finisarea suprafeței, proprietățile fizice și mecanice. Aceste avantaje ale laminării la rece au făcut-o la scară largă atât în metalurgia feroasă, cât și în cea neferoasă.
Cu toate acestea, trebuie remarcat faptul că procesele de laminare la rece este mai intens de energie decât procesele de laminare la cald, la un metal călit deformare la rece (naklepyvaetsya), prin aceasta pentru a restabili proprietățile materialului plastic trebuie să recoaceri. Tehnologia de producție a foilor laminate la rece include un număr mare de redistribuire, necesită utilizarea unor echipamente complexe și diverse.
În prezent, ponderea foilor laminate la rece în greutatea totală a oțelului subțire este de aproximativ 50%. Producția de foi, benzi și benzi laminate la rece continuă să se dezvolte intens. Cea mai mare parte (circa 80%), foi laminate la rece cu grosimea oțelului structural cu emisii reduse de carbon de 0,5-2,5 mm, o lățime de 2300 mm. Această foaie de oțel este folosită pe scară largă în industria automobilelor, deci este deseori numită autolist. Prin laminare la rece produce aproape toate staniu - produse care se extind în cantități mari, pentru fabricarea de recipiente pentru alimente, în special cutii. Materialul pentru tablă este, de asemenea, oțel cu conținut scăzut de carbon, dar în majoritatea cazurilor tabla este produsă cu un strat de protecție, cel mai adesea - staniu. Placa este laminată sub formă de benzi cu o grosime de 0,07-0,5 mm și o lățime de până la 1300 mm. Printre tipurile comune de produse laminate la rece includ, de asemenea, de decapare (decapare și oțel recopt utilizate în producția de ustensile emailate și alte articole cu acoperiri), o foaie de acoperire (de multe ori produse galvanizat), slab aliat oțel structural. De notat special, sunt două grupuri importante de oțel aliat - rezistent (inox) si electrice coroziune (dinam și transformator).
În metalurgia neferoasă, laminarea la rece este utilizată pentru a produce benzi subțiri, foi și curele din aluminiu și aliajele sale, cupru și aliajele sale, nichel, titan, zinc, plumb și multe alte metale. Folia are cea mai mică grosime. De exemplu, folia de aluminiu este produsă sub formă de benzi cu o grosime minimă de 0,005 mm, o lățime de până la 1000-1500 mm. Varietatea gamei de foi laminate la rece este asigurată de folosirea laminoarelor de diferite modele, cu caracteristici tehnice și niveluri de productivitate foarte diferite.
1. Fabricarea oțelului tablă electrotehnică
Oțelul electrotehnic este divizat în mod convențional din oțel dinamometric și transformator. Numai numele acestor oțeluri indică domeniile aplicației lor. Oțelul dinamos este utilizat în principal pentru fabricarea motoarelor electrice (generatoare) și a transformatoarelor pentru fabricarea transformatoarelor și a diverselor dispozitive electromagnetice. Oțelurile electrotehnice funcționează sub inversarea curentului alternativ și ar trebui să aibă pierderi scăzute de wați (histerezis) și inducție magnetică ridicată.
Rezistența deformării și ductilitatea oțelurilor electrotehnice depind puternic de conținutul procentual de siliciu. O creștere a cantității sale în oțel duce la o creștere a rezistenței la deformare și la o scădere bruscă a ductilității. Prin urmare, laminarea la rece a oțelului de transformare este mult mai dificilă decât dinamometrul de rulare.
2. Procesul tehnologic și echipamentul morii.
Amenajarea echipamentului.
Răcirea la rece a oțelului de transformator la uzinele de uz casnic se realizează pe morile continuă și multi-rolă reversibile cu o singură celulă (figura 1), cu trei colivii și cu cinci celoide.
la rece din oțel transformator de laminare compresie intens Acceptată în prima trecere (35-45%), datorită deformării semnificative a benzii de încălzire pentru a furniza 100-150 ° C, care afectează în mod favorabil procesul de laminare roll în treceri ulterioare, deoarece banda încălzită la o temperatură ( ca urmare a deformării) duce la o scădere semnificativă a rezistenței la deformare în timpul laminării.
Pentru degresarea benzii după laminare la rece, pot fi utilizate diverse metode, inclusiv electrolitice, chimice, cu ultrasunete.
În prezent, pentru degresarea bobinelor prin mijloace chimice, se utilizează soluții de următoarea compoziție, g / dm3:
Soda calcinată. 50
Soda caustică. 5
Emulgatorul OP-7. 3
Influența decisivă asupra calității oțelului de transformator laminat la rece are un tratament termic - recoacere preliminară, intermediară și finală la temperaturi ridicate.
Schimbările în caracteristicile magnetice ale oțelului transformator în timpul tratamentului termic sunt cauzate de: a) schimbarea formei de carbon (cele mai bune proprietăți se obțin atunci când carbonul este sub formă de grafit); b) arderea degazării carbonului și a metalelor; c) creșterea dimensiunii cerealelor; d) recristalizarea oțelului nitat (la care se îndepărtează tensiunile interne, modificările dimensiunii granulelor și orientarea acestora);
Reacția de recristalizare intermediară a oțelului de transformare la rece este necesară pentru a reduce duritatea benzii după prima secțiune laminată la rece. Experiența a arătat că o astfel de recoacere a oțelului transformator în cuptoare cu burdufuri cu atmosferă de protecție diferită nu influențează practic reducerea conținutului de carbon din oțel.
Reacția la temperaturi ridicate a transformatorului laminat la rece
oțelul este realizat în cuptoare cu burduf la 1100-1200 ° C într-un vid sau în hidrogen uscat.
La recoacerea la temperaturi înalte, granulele de ferită sunt lărgite, coagularea incluziunilor, modificarea formei de carbon și scăderea cantității de impurități nocive din oțel.
În ultimii ani, pentru decarburizarea și temperarea finală a oțelului transformator, au fost construite turnuri și turnuri orizontale, caracterizate printr-o productivitate ridicată, care permite o decarburizare considerabilă a metalului.
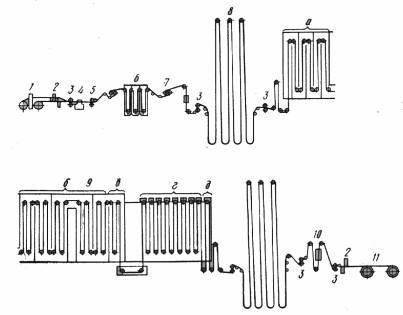
Fig. 21. Linia de tratare termică a oțelului transformator cu cuptor turnat;
a - camera de încălzire; b - camera de imbatranire; c - cameră de răcire controlată;
g - camera de răcire accelerată; д - camera de suflare; 1 - Stație de alimentare;
2 - foarfece de ghilotină; 3 - role de tragere; 4 - mașină de sudat; 5 - mașini cu perie cu jet; C - baie de degresare electrolitică; 7 - uscător;
8 - găuri de buclă; 9 - cuptor turn; 10 - instalare Pentru aplicarea unui strat de protecție; 11 - Coiler.
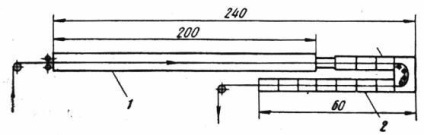
În Fig. 21-24 prezintă agregatele pentru tratamentul termic al oțelului transformator și în figura 132 separarea stratului de izolație electrică a laminatului la rece a oțelului transformator.
Fig. 22. Cuptor de întindere pentru normalizarea rolelor de oțel transformator:
1, 2 - camere de încălzire și răcire, respectiv.
În producția modernă de transformator
lingouri din otel redistribuire tehnologie oferă o masă mare în dale înflorite sau moară slabbing sau obține dale cu un oțel de turnare continuă, folosind oțel conținând 2,9- 3,2% Si. La producerea lingourilor dale laminate kolodtsevoy cuptor încărcare axial fierbinte cu suprafață temperatură lingou în timpul aterizării 800-950 ° C. Durata barelor de încălzire în funcție de raportul de încărcare de temperatură de 7-10 ore, ceea ce înseamnă că cel puțin 75% din timp va fi cheltuite lingoul care se topește la temperatura de distribuire. Plăci din fluxul laminor de debavurare supus curăța-up mașini: Scarificarea și apoi supus unui tratament termic (recoacere) la o temperatură de 750 ° C, cu o sarcină de dale în forța de tracțiune la cald cuptor. Răcirea după cuști de recoacere trebuie să fie menținută la o viteză de 40-50 ° C, modul de încălzire Reglementată și răcire placă de oțel siliciu previne formarea fisurilor datorită tensiunilor termice semnificative.
Dacă este necesară curățarea suplimentară a defectelor de suprafață pe plăci, se efectuează pe plăci răcite la adiacență.
Plăcile înainte de rulare pe o moară cu bandă largă sunt încălzite în funcție de compoziția chimică a oțelului de transformare la 1200-1400 ° C. Avantajul utilizării laminoarelor semi-continue pentru laminarea în role este posibilitatea
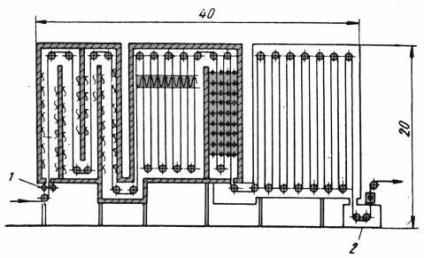
Fig. 23. Cuptor electric pentru turnare pentru decarburizarea și recoacerea oțelului de transformare prin camere de răcire încălzite, deținute și controlate:
1 - rulou; 2 - un rezervor pentru înmuiere în apă
reglarea numărului de treceri și mărimea reducerii în funcție de compoziția chimică a oțelului, temperatura plăcii și grosimea materialului rulant. Înainte de terminarea grupului de standuri, temperatura rolei cu grosimea de 18-25 mm trebuie să fie între 950-1050 ° C, temperatura de rulare la final nu este mai mică de 850 ° C, iar temperatura benzii atunci când se uită la coiler nu trebuie să depășească 600 ° C.
Grosimea unui material laminat laminat la cald laminat la cald este determinată de modul său de laminare într-o moară de laminat la rece și structura morii. De obicei, grosimea rolei este de 2,5 mm.
3. Materialul și profilarea rolelor de laminare la rece.
Rolele laminoarelor de laminare la rece sunt expuse la presiuni de contact foarte mari, care, de regulă, sunt de câteva ori mai mari decât tensiunea de întindere a metalului deformabil la temperatura camerei. În acest sens, rolele trebuie să aibă o rezistență și duritate adecvate. Cel de-al doilea lucru care trebuie luat în considerare este creșterea cerințelor față de calitatea suprafeței foilor laminate la rece. Pentru a le satisface, rolele trebuie să aibă un anumit microrelief de suprafață; cu cât sunt mai puțin permise deteriorările și defectele macroeconomice.
Rolele de lucru ale laminoarelor sunt fabricate din oțeluri cu conținut ridicat de carbon, aliate cu crom, vanadiu, tungsten și alte elemente. role de oțel 9X, 9HF, 9H2, 9H2V, 9H2SF, 9H2MF, 9H2SVF, 60H2SMF utilizate cel mai des. După turnare și forjare, rolele sunt supuse unui tratament termic complex, în etapa finală - călirea de suprafață cu temperatură. Duritatea cilindrului rolelor de lucru este de obicei în intervalul 90-102 HSD (Shore), duritatea gâtului este de 30-55 HSD. Grosimea stratului de suprafață întărit al rolelor trebuie să fie de cel puțin 3% din raza rolelor. Pentru rolele de lucru cu diametru mare (de ordinul a 500-600 mm), grosimea rațională a stratului întărit este de aproximativ 10-12 mm. In ultimii ani, cilindrii de lucru mnogovalkovyh mills destinate în special pentru material dur, panglici subțiri, uneori realizate din carbură solidă cimentat pe bază de carbură de wolfram (85-90% carbură de tungsten și 10-15% cobalt). Prin metoda presării la cald și sinterizării, este posibil să se obțină role unice cu un diametru de până la 80 mm, cu o lungime de până la 1500 mm. Duritatea acestor rulouri atinge 115-125 HSD. Rezistența lor la uzură este de 30-50 de ori mai mare decât cea a rolelor fabricate din oțeluri aliate. Datorită modului foarte ridicat de elasticitate, rolele de carbură-tungsten sunt aplatizate în zona de deformare de 3 ori mai puțin decât rolele de oțel. În același timp, trebuie avut în vedere faptul că rolele de carbură-tungsten au un cost ridicat și o fragilitate crescută. Acestea din urmă fac dificilă utilizarea acestora pentru încărcarea prin impact și deformări semnificative.
Rolele de sprijin sunt de trei tipuri: solid, turnat și compozit (bandă). Cele mai frecvente sunt rulourile de susținere. Sunt fabricate din oțel 9X, 9X2, 9ХФ, 75ХМ, 65ХНМ. Pentru producția de axe de rulouri compozite se utilizează oțeluri mai simple, mai puțin aliate: 70, 55X, 50XG, 45HNV, 45HNM. Bandajele în compoziția lor chimică corespund rulourilor solide. Duritatea ruloului de rulare este de obicei 60-85HSD.
În practică, sa stabilit că performanțele noilor role, în special lucrătorii care au suferit un tratament termic complex, crește semnificativ atunci când sunt păstrate timp de 5-6 luni; acest lucru ajută la ameliorarea tensiunilor interne din rulouri.
O operație importantă este pregătirea suprafeței rulourilor pentru laminare. Rolele de lucru sunt utilizate cu o suprafață lustruită, lustruită și acoperită. Cilindri de șlefuire la gradul de curățare a suprafeței de la 7 la 9 reprezintă cea mai comună operațiune; este efectuată pe mașini speciale de măcinat cu role. Uneltele de prelucrare sunt roțile de șlefuire din carbură de siliciu, carbură de bor, electrocorund, diamante sintetice și alte materiale. Atunci când măcinarea este efectuată mai întâi de stripare pentru a elimina defectele de suprafață acumulate, și apoi - finisarea cu profilarea cilindrului rolei și finisarea suprafeței la o anumită clasă de puritate. Îndepărtarea stratului de suprafață pentru o re-măcinare planificată (în absența deteriorării adânci) a rolelor de lucru este de aproximativ 0,05-0,1 mm pe diametru.
munca șlefuită role finisaj de suprafață 10-12 grade aplicate mnogovalkovyh mori, în special, în laminarea oțelului inoxidabil și sunt adesea în rularea anumitor tipuri de metale neferoase, cum ar fi o folie. Polizarea se efectuează, de asemenea, pe polizoarele de ruliu folosind cercuri de corindon cu granulație fină pe un liant de bachelită cu umplutură de grafit, roți de grafit și pâslă. Pe suprafața cercurilor de pâslă se aplică o pastă de lustruire de tip GOI.
Canelate, role de lucru rugoase utilizate în primele și ultimele standuri ale morilor continue: în primul stand - pentru a îmbunătăți condițiile de aderență în ultimul stand - pentru a preveni sudarea bobine suluri sau foi în pachete în timpul recoacere. Cilindrii tăiați sunt utilizați în alte cazuri când este necesar să se obțină o suprafață aspră a produsului. Operația de crestatare se realizează pe mașini speciale de sablare. Corpul de lucru este împușcat din fontă sau oțel cioplit, uneori tăiat din oțel (tăiat).
În prezent, eroziunea electrică cu scânteie și scânteie este din ce în ce mai utilizată pentru a obține o suprafață de rulouri de înaltă calitate, rezistentă la uzură, cu orice rugozitate necesară.
Sub acțiunea marilor forțe care apar în timpul laminării la rece, rolele suferă o deformare elastică considerabilă: ele se îndoaie și se îndoaie
Articole similare
-
Rezumat amulete ruse - site-ul rezumatelor, lucrărilor de curs, eseuri, rapoarte și teze
-
Abstract internet explorer - bancă de rezumate, eseuri, rapoarte, lucrări de curs și diplomă
Trimiteți-le prietenilor: