În prezent, scara metalică a cuptorului fierbinte desulfurarea încă crește pe măsură ce prelucrarea materiilor prime și de porc de fier în ateliere de sablare și turnătorii, înainte de turnarea în forme. Această tendință este tipic pentru fabricile din Europa de Vest, SUA, Japonia, China și altele. Acest lucru se datorează mai multor factori, dintre care cele mai importante sunt de a crește eficiența furnalul, creșterea volumului de livrări de înaltă calitate, fonta si piese turnate din ea, extinderea volumului de producție de oțel de înaltă calitate și de a le turnare în fugă.
Comparând tendința de dezvoltare vnedomennoy desulfurarea în 60-90 de ani, trebuie remarcat faptul că, recent, cea mai mare parte a investițiilor de capital se referă la metode de creștere și îmbunătățirea tratamentului polonic de fier. Cea mai mare atenție este acordată desulfurizers alegerii raționale, crearea unei baze industriale pentru producerea și dezvoltarea unor metode de introducerea lor efectivă a metalului. Deoarece un număr semnificativ de desulfurizers care au trecut teste extensive industriale (magneziu, reactivi care conțin magneziu, sodă calcinată, var, carbură de calciu, carbonat de calciu, etc.) Creșterea preferință magneziu granulară și, în unele cazuri, amestecuri industriale bazate pe mai multe desulfurizers. În plus, un reactiv destul de comun în SUA și Europa de Vest este încă carbidul de calciu. În același timp, anumite limitări în utilizarea carburii de calciu se datorează mai multor factori tehnologici și considerentelor de siguranță și de mediu.
Principalele motive pentru utilizarea magneziului în locul carburii de calciu sunt următoarele:
- scăderea consumului de reactiv (magneziu granulat cu un strat de sare este de 8-12 ori mai mic, amestec de magneziu și var de 3-4 ori mai mic decât carbidul de calciu);
- costuri scăzute specifice de prelucrare a fontei datorită consumului redus de magneziu;
- scăderea costurilor de capital ca rezultat al unei mai mari siguranțe a reactivului de magneziu, a zgurii formate și a fumului emis de colector;
- Creșterea gradului de desulfurare în prelucrarea fontei cu temperatură scăzută;
- posibilitatea de a obține un conținut final de sulf de 0,003%;
- reducerea duratei tratamentului secundar de aproximativ 2 ori;
- mai puțin efect negativ asupra căptușelii găleții;
- o scădere de 3-10 ori a cantității de zgură formată.
După tratarea cu carbură de calciu, zgura conține carbură nereacționată, care, atunci când reacționează cu umiditatea, formează acetilenă. Prin urmare, atunci când se desulfuriză fonta cu carbură de calciu, se utilizează echipamente speciale și precauții speciale. Când se lucrează cu magneziu granular, se folosesc tehnici și echipamente convenționale pentru tratarea fontei din fontă.
Aspectele tehnologice ale desulfurizării fontei prin magneziu depind în mare măsură de proprietățile sale fizice, dintre care cele mai importante sunt punctul de topire, punctul de fierbere și presiunea vaporilor. Temperatura de topire de magneziu este de 650 ° C Presiunea de vapori a pur p magneziu (mm Hg), în funcție de temperatura T este determinată, de exemplu, Bauer și Bruner din următoarea ecuație:
Punctul de fierbere al magneziu, calculat folosind ecuația (2.1) este de aproximativ 1107 ° C la presiune atmosferică până la 1200 ° C, la o presiune de două atmosfere și 1250 ° C, la o presiune de trei atmosfere. La evaluarea eficacității magneziu trebuie considerată ca o caracteristici termodinamice modificatoare ale reacțiilor interacțiunii sale cu componentele topiturii, condițiile cinematice ale reacțiilor, condițiile de evacuare a produselor de reacție din topitură și posibilitatea tehnologică a introducerii unui inoculant topit.
Condițiile termodinamice se aplică topiturii de magneziu pentru rafinare este determinată prin afinitatea ridicată la sulf și oxigen, care sunt impurități dăunătoare din fier. Căldura de formare a sulfurii de magneziu este de două ori mai mare decât cea a manganului. Reacția magneziului gazos cu sulful dizolvat în topitură se caracterizează printr-o schimbare semnificativă a energiei libere. Afinitatea chimică a magneziului la sulf scade rapid odată cu creșterea temperaturii și la 1600 ° C se apropie de afinitate mangan pentru sulf. Este posibil, cu un grad înalt de încredere presupune că etapa de limitare a vitezei cu desulfurarea adâncimea limitată este transferul de masă de sulf de la suprafață la volumul de metal se topesc pop bule de vapori de magneziu.
Magneziul are o afinitate chimică foarte mare pentru oxigen. Căldura de formare a oxidului de magneziu este destul de mare:
Reacția de magneziu gazos cu oxigen are loc cu o eliberare mare de energie liberă. În aliajele de fier-carbon, magneziul interacționează activ și cu oxigenul dizolvat. Cu toate acestea, dezvoltarea reacției dintre magneziu și oxigen depinde de prezența acestuia în fontă în formă dizolvată. Se știe că fonta industrială are un grad redus de oxidare, ceea ce sugerează că pierderea de magneziu din reacția cu oxigen este nesemnificativă.
Condițiile cinetice pentru reacțiile de interacțiune a magneziului cu componentele fontei sunt determinate de faptul că magneziul este în stare gazoasă. Gazul magnetic are o suprafață de contact extrem de dezvoltată cu un metal, ceea ce facilitează alimentarea unui reactiv pe suprafața de reacție. O cantitate mare de gaz generat la intrarea magneziu favorizează amestecarea intensă a topiturii și, prin urmare, îmbunătățește condițiile de furnizare convectivă a impurităților metalice dizolvate în zona de reacție.
Pentru procesele tehnologice asociate cu tratarea topiturilor de fier-cărbune cu magneziu, solubilitatea magneziului într-un aliaj solid și lichid este importantă. Solubilitatea magneziului în fierul solid este foarte scăzută, ceea ce se explică prin factorul de volum nefavorabil al magneziului în raport cu fierul. Volumul atomic de magneziu depășește de două ori volumul atomic de fier.
Pentru o manifestare mai completă a proprietăților magneziului ca reactiv desulfurizant, rafinat și modificator, metoda de introducere a acestuia în topitură este de mare importanță. În condiții industriale, magneziu se utilizează sub formă de lingouri, granule și pulbere. Cu toate acestea, în toate cazurile, dorința de a asigura o intrare controlată a magneziului în fluxul de gaz purtător este caracteristică pentru utilizarea eficientă a desulfuratorului.
Cel mai ieftin, convenabil (sigur) în depozitare și disponibil în aprovizionare este lingoul de magneziu, produs de întreprinderile de metalurgie neferoasă. Dacă dispozitivul submersibil pentru magneziu intrare (evaporator) pentru a realiza o tijă goală la interior și prin el un gaz de alimentare clopot, imersat evaporator fier în oala de turnare să nu se ridice deasupra deschiderilor clopotul. Acest lucru face posibilă plasarea unui distribuitor mecanic în partea superioară a vaporizatorului și furnizarea de magneziu în cantitatea necesară prin bara de clopot.
lingouri de magneziu (fig. 2.8, a) este conectat într-o ghirlandă, înainte de prelucrare, este pus pe cârlig și cu un tambur de antrenare dispus în carcasa etanșată este tras în tija vaporizator, astfel încât partea de jos a marginii lingou este de aproximativ nivelul de găuri în clopot sau mai mult de mai sus. Evaporatorul a fost imersat într-o oală de turnare din fontă, alimentarea se prin conducta de gaz (azot sau aer) la o viteză oferind o viteză de creștere a presiunii în interiorul carcasei și tija, rata corespunzătoare de creștere a adâncimii de imersie într-un evaporator metalic. După ce a atins o adâncime predeterminată de curgere a gazului de imersie din vaporizator și începe să se reducă treptat lingouri de magneziu furnizate pe suprafața metalică în interiorul clopotului evaporator. La dispozitivele reale rata de evaporare a magneziului este schimbat în intervalul 0,05-0,20 kg / s, care pentru lingouri de magneziu standard, cu o greutate de 8 kg și o lungime de 0,48 m este atins atunci când viteza de coborâre a 0,003-0,012 m / s. lingouri Dimensiune sarcină unică determinată de timpul de ședere autorizată a vaporizatorului în metalul topit, magneziul au primit rata de intrare și de obicei 3-4 lingou.
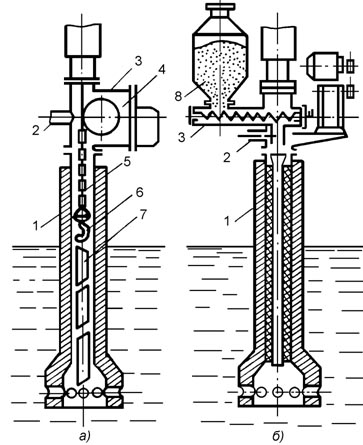
Figura 2.8 - Schema de introducere a lingoului (a) și granular (b) magneziu: 1 - evaporator; 2 - țeavă de ramificație pentru alimentare cu gaz; 3 - corpul dozatorului; 4 - un tambur; 5-lanț; 6 - cârligul; 7 - lingouri de magneziu; 8 - bunker pentru magneziu granulat.
Debit de gaz furnizat către evaporator în prelucrare, este ales dintre condițiile pentru a preveni posibilitatea pătrunderii vaporilor de magneziu în evaporator și după deplasarea acestor vapori la fier prin deschiderile din clopot. Când se utilizează azot și aer, debitul respectiv este de 20-40 și respectiv 40-80 m 3 pe oră.
Cu referire la magneziu granular, schema de bază pentru realizarea metodei "magneziu-gaz" este prezentată în figura 2.8, b. Procesul de desulfurarea în acest caz controlat mai flexibil de lucru simplificat pe dispozitivul de încărcare magneziu scade secțiune de braț și, în consecință, scăderea debitului de gaz introdus în evaporator. Rata optimă de intrare a magneziului este determinată în funcție de timpul de staționare admisibil al vaporizatorului în metalul topit, încărcătura de magneziu și gradul de umplere a găleată. În practică, atunci când se tratează fonta cu lingură de magneziu, este de obicei de 0,07-0,12 kg / s, granular - 0,01-0,2 kg / s.
Dezvoltarea metodei de desulfurare a fontei cu magneziu granular este utilizarea granulelor cu un strat special de sare. Din anii '80, magneziu granular a fost folosit în multe fabrici din Europa de Vest și Statele Unite. În Europa de Vest, peletele de magneziu au fost obținute cu o acoperire nehigroscopică dintr-un amestec eutectic de clorură de sodiu 40-50% și clorură de potasiu 50-60%. În Statele Unite pentru desulfurizare, reactivul Pelamag este utilizat pe scară largă, ceea ce reprezintă granule conținând 88-92% metal de magneziu cu un strat de sare dintr-un amestec de cloruri de magneziu, potasiu, calciu și sodiu. Utilizarea reactivului "Pelamag" a permis înlocuirea celor două fabrici uzate de "Armco" cu amestecul utilizat anterior de magneziu cu var. Intensitatea intrării sale în fontă este de 13 kg / min la umplerea cuvei de 200 de tone la 95%. Magneziul este introdus în metalul lichid într-un curent de azot printr-o lance, care este imersat la un unghi de 15-25 ° față de verticală, având un canal în formă de T la ieșire. Gradul de asimilare a magneziului în acest caz este de aproximativ 50%, iar durata purjării este de 8 minute. Rata de reducere a temperaturii fontei în timpul procesării este de 1-2 ° C pe minut.
Un exemplu de tip rațional de căutare desulfurizer poate provoca, de asemenea, companie de plante «Youngstown Steel» (USA), utilizat inițial magkokom metoda desulfurarea (amestec de magneziu și cocs). Din 1977 g. Desulfurarea la această plantă produc magneziu granulat acoperit cu un înveliș de clorură de sodiu 54%, 20% de clorură de magneziu și clorură de potasiu 13%.
France oras 1980 aplicat cu un reactiv de magneziu, dezvoltat de companiile franceze și USINOR SOFREM și este un amestec de 80% granule sferice de magneziu pur dimensiune 0.3-1.6 mm și 20% zgură granulată sol, aceeași distribuție a mărimii particulelor. Potrivit dezvoltatorilor, magneziu previne zgură de la lipirea reactantul secțiunea tuyere și îmbunătățește fluidității. Timpul de procesare este de 8-10 minute, iar intensitatea injectării reactivului este de 6-12 kg / min.
În plus față de magneziu granulat, un număr de fabrici folosesc tehnologia de injecție cu magneziu sub formă de pulbere. La scară industrială, injectarea de magneziu sub formă de pulbere a fost realizată pentru prima oară de către Institutul de Metalurgie Feroasă al Academiei Naționale de Științe a Ucrainei (Dnepropetrovsk) la Uzina de la Azovstal (Mariupol). Magneziul este injectat în fontă printr-un refractar căptușit cu un refractar căptușit cu un strat de calcar sau dolomită. Plăcuța protejează pulberea de magneziu de radiația termică a metalului lichid și ajută la curățarea orificiului de ieșire a lăncii din particulele de magneziu lipite (în acest caz nu există sudură metalică). Cel mai bun raport dintre amestecul de magneziu și umplutură este 1: 3. O diagramă schematică a instalației de desulfurare a fontei cu magneziu sub formă de pulbere este prezentată în figura 2.9.
Consumul de aer pentru transportul amestecului este de 70 - 120 m 3. Consumul de amestec este de 50 - 80 kg / min. Consumul specific de magneziu 0,7 - 0,95 kg / t asigură o îndepărtare suficientă completă a sulfului din fontă. Ulterior tehnologia a fost extinsă la mai multe fabrici din Ucraina.
Sunt cunoscute și alte variante de utilizare industrială a magneziului pulverulent într-un amestec cu umpluturi:
- un amestec de magneziu și carbură de calciu la uzina "Arbed Saarstahl" (Germania);
- amestec de compuși MgSi și MgAl2O3.
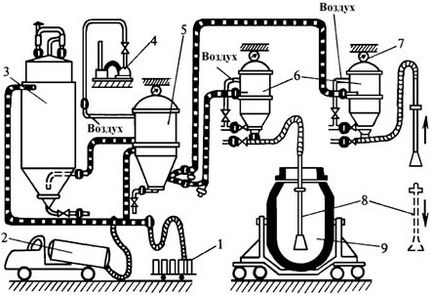
Figura 2.9 - Schema de desulfurare a fontei cu magneziu sub formă de pulbere: 1 - capacitate cu magneziu; 2 - cisternă pentru aprovizionarea cu var; 3 - bunker pentru var; 4 - instalarea compresorului; 5 - mixerul; 6 - rezervoare de aprovizionare; 7 - dinamometru; 8 - tuburi; 9 - o ladă de fontă.
Articole similare
Trimiteți-le prietenilor: