Elemente de montare a atașamentelor. preforme de instalare pentru a produce o suprafață plană pe suportul principal (constant, reglabil și auto-aliniere) determinarea poziției piesei, iar suportul auxiliar (reglabil și auto-aliniere), utilizat pentru creșterea rezistenței rigiditate și vibrațiilor sistemului tehnologic.
suport permanent principal cu un cap sferic și randalinat folosit la instalarea blancuri mici cu baze netratate și plat cap - pentru setarea semifabricatelor menționate tratate cu bază. Pentru a asigura o precizie ridicată a instalației, înălțimea capului H este realizată cu o toleranță suficient de strictă.
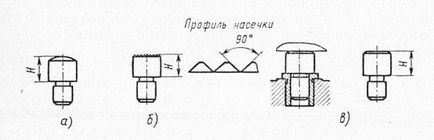
Fig. 1. Principalele suporturi permanente cu cap (a), înscris (b) și cap plat (în) sferic
Cu scopul de a îndepărta cel mai bine un bărbierit, un suport cu capul cusut se fixează pe verticală și se sprijină cu un cap sferic - pe pereții orizontali de adaptare.
În locul suporturilor cu capete plate, se aplică uneori plăci plate fără caneluri și cu caneluri. Groabele facilitează îndepărtarea chipsurilor atunci când piesa se taie. Plăcile de sprijin sunt utilizate la instalarea pieselor cu o bază prelucrată.
Suporturile trebuie să aibă o rezistență ridicată la uzură. Sunt fabricate din oțel de calitate U7A (suporturi diametru D până la 12 mm), marcaje de cusătură 20X (suporturi cu diametru mai mare și plăci). După tratamentul termic, duritatea suporturilor 56-61 HRQ. Suporturile cu cap de mortar sunt realizate din oțel 45 (duritate după tratament termic 41,5-46,5 HRC3).
Suporturile ajustabile sunt utilizate la montarea spațiilor libere cu baze netratate sau ca suporturi auxiliare.
Suporturile de auto-aliniere sunt utilizate pe scară largă ca elemente de bază și auxiliare pentru tragerea găurilor și pentru efectuarea altor operații atunci când se prelucrează spații de formă complexă.
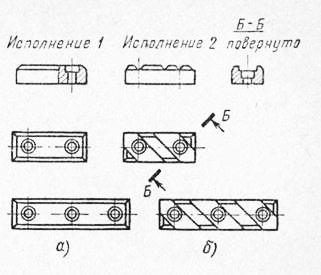
Fig. 1. Plăci de susținere fără caneluri (a) și caneluri (b)
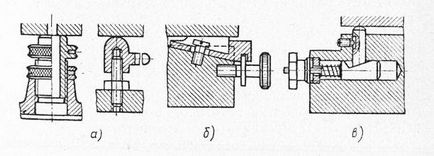
Fig. 2. Suporturi reglabile: a-șurub, b-wedge, c-wedge cu piston
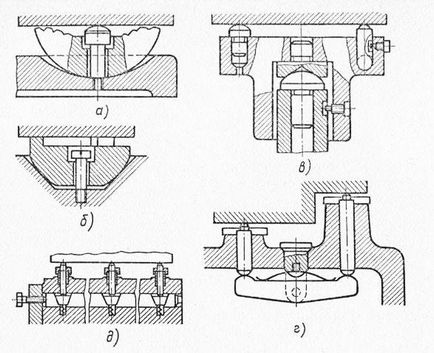
Fig. 3. Suporturi auto-aliniere: a, b, c - bila, d - piston, d - piston
Montarea plăcuțelor pe gaură se realizează cu ajutorul mandrinelor și a degetelor cilindrice de localizare. Atunci când se montează o piesă de lucru cu un spațiu, gaura de bază trebuie prelucrată până la a 7-a clasă de precizie. În acest caz, suprafața exterioară poate fi decalată în raport cu interiorul în interiorul spațiului.
O mai mare precizie a instalației (cu o abatere de la coaxialitatea de 0,005-0,01 mm) este asigurată de mandrine și mandrine conice prin presarea piesei de prelucrat.
Mandrinele de extindere a maxilarului sunt utilizate pentru prelucrarea semifabricatelor cu o gaură realizată la gradul de precizie de 8-13 grade.
Cea mai mare precizie a instalării (0,002-0,005 mm) este asigurată de mandrine cu un element elastic: o gheară (gaura este realizată de clasa de precizie 8-13); cu bucșe cu pereți subțiri și hidroplastice (gaura este realizată conform preciziei de calificare 7-8); ondulație ondulată (gaura este făcută conform clasei de precizie 7-8).
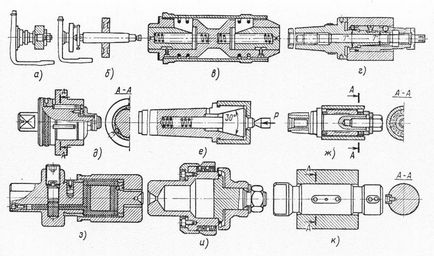
Fig. 4. Mandrină: A - pentru montarea pieselor cu b- clearance conice, c - Cam r - bile, etc - cu role, f, g - Collet, s - un manșon cu pereți subțiri și Gidroplast, și - cu mâneci ondulat, k - cu zapressovaniem piesa de prelucrat
Atunci când se montează părți ale corpului și plăci de dimensiuni medii pe două găuri, se asigură o precizie de orientare suficient de ridicată. Găurile din piesele de prelucrat trebuie prelucrate în conformitate cu clasa a 7-a de precizie. Una dintre degetele de localizare este cilindrică, cealaltă este tăiată. În acest caz, și cu distanța maximă posibilă între degete, este asigurată cea mai mică eroare în poziția unghiulară a piesei de prelucrat.
Axele, cilindrii, precum și semifabricatele situate pe dorn, sunt instalate în centre.
Instalarea plăcilor de-a lungul suprafeței cilindrice exterioare se realizează pe prisme, cartușe, bucșe. Prismele pentru fixarea scurgerilor scurte sunt standardizate. Dispozitivele utilizează prisme cu un unghi de 2a = 60; 90 și 120 ° (prismele cu un unghi de 2a = 90 ° au obținut cea mai mare aplicație).
Fixarea blanurilor în cartușe este o metodă universală, folosită pe scară largă. Eroarea la instalare este determinată de precizia fabricării cartușului, de precizia producerii bazelor tehnologice ale țaglei. Atunci când se fixează piesele ne-rigide cu o forță îndreptată de-a lungul razei, este posibilă îndoirea piesei de prelucrat, pentru a reduce numărul de fălci din cartuș.
Metode și elemente ale sculelor pentru instalarea acestora pe mașină. Echipamentul tehnologic este instalat pe unitatea de lucru a mașinii, care are un loc special (set de baze).
Pe strunguri mandrine grup și mandrine montate direct pe un ax centrat pe un element de fixare dispus pe (gaura conică) suprafața exterioară sau interioară disc; folosind o tranziție a mandrinei mandrină de centrare sau știftul instalat în gaura conică a axului.
Pe strunguri, atașamentele sunt de asemenea montate pe centre (cum ar fi mandrinele), în gaura conică a coamei, pe suportul de scule.
La frezare, în planul mesei, care are caneluri în formă de T, se montează dispozitive de găurit orizontal, de foraj și alte mașini-unelte. Pentru orientarea în raport cu alimentarea longitudinală, pe corpul dispozitivului sunt prevăzute două pivoze prismatice, care intră într-una din canelurile în formă de T ale mesei (de obicei, în mijloc, ca mai precise). Datorită uzurii și reparațiilor ulterioare, lățimea canelurilor mesei crește, astfel încât pentru a preveni posibilele viraje, dispozitivul este presat pe o parte a canelurii în timpul instalării.
Pentru fixarea pe masă în carcasa dispozitivului există ochete speciale pentru șuruburi. Cu forțe mici de tăiere, doi ochi sunt plasați în același slot în formă de T ca și cheile, în general - patru ochi sunt plasați simetric în canelurile adiacente.
În unele cazuri, pentru a plasa rațional dispozitivele pe masă și pentru a menține precizia bazelor de masă, acestea din urmă fixează rigid plăcile suprapuse cu o rețea de caneluri și găuri care sunt utilizate pentru a instala uneltele.
Dispozitivele de pe masă ale mașinii pot fi instalate fără aliniere (cu eroarea de instalare a dispozitivului) sau cu reglarea poziției de-a lungul suporturilor. În condițiile tehnice de pe desenul de asamblare al dispozitivului și în foaia tehnică pentru fabricarea piesei trebuie indicată eroarea permisă de reconciliere. Reglarea poziției dispozitivelor este utilizată pe scară largă pe uneltele de tăiere, șlefuire, strunjire, frezare și alte mașini-unelte.
Toate uneltele de tăiere au o piesă de fixare destinată montajului și fixării sculei de tăiere de pe echipamentul de procesare sau de scule.
La incisivi, setul de baze este alcătuit din mai multe planuri sau din suprafețe cilindrice și plate (cu fața). În cazul forajelor, consolelor, alezelor, frezelor, piesa de fixare este realizată sub formă de cot de formă cilindrică sau conică sau o gaură cilindrică sau conică. Pentru transferul momentului, canelurile de fixare sunt prevăzute în orificiu sau la capătul sculei.
Întreaga sculă, fixată pe axul mașinilor CNC pe mașinile de frezat, este echipată cu elemente pentru crearea forței axiale a fixării.
La re-ascuțirea sculei de tăiere, de regulă, se utilizează aceleași baze ca atunci când sunt instalate pe o mașină sau într-o unealtă. În același timp, mătururile, ghidajele, broaștele sunt așezate în centru și orientarea unghiulară este efectuată peste dintele sculei.
Când montați roți de șlefuire pe axul mașinii, utilizați o gaură și capete plate; capetele de rectificat sunt atașate la tija cilindrică.
Unele dintre instrumentele utilizate ca bază de partea lor de lucru (de exemplu, netezirea dornului trebuie să calibreze găurile din porțiunea filetată a robinetelor Cheie fixă cu o coadă curbată).
Dispozitive de prindere. Dispozitivele sunt destinate să trimită semifabricatelor la elementele de montare ale dispozitivului, asigurând un contact fiabil al piesei de prelucrat cu elementele de instalare și împiedicând deplasarea și vibrațiile în timpul prelucrării.
Necesitatea fixării piesei de prelucrat este eliminată dacă forțele care apar în timpul prelucrării nu pot deplasa piesa de prelucrat (de exemplu, în timpul procesului de coacere).
Dispozitivul de prindere constă, de obicei, dintr-un mecanism de acționare și un dispozitiv de acționare. În același timp, există dispozitive care constau doar dintr-un mecanism de putere (se numesc mecanisme de prindere manuală) și dispozitive constând doar dintr-o unitate (ele sunt numite dispozitive de acțiune directă).
Mecanismele de forță (șurub, pană, excentric, pârghie, balamale etc.) diferă în simplitatea fabricației, compactitatea, capacitatea de a schimba magnitudinea și direcția forței transmise. Mecanismele cu șurub și cu pană au capacitatea de auto-frânare, ceea ce este foarte important din punct de vedere al ingineriei de siguranță (în special în cazul dispozitivelor de prindere combinate cu un dispozitiv de acționare în caz de avarie de alimentare de urgență).
Mecanismele de prindere a șuruburilor sunt utilizate pentru fixarea directă a piesei de prelucrat cu un șurub de presiune.
mecanisme Wedge de prindere sunt utilizate pe scară largă în dispozitive au un unghi de pană de 6-15 ° (care asigură o rezistență semnificativă și fiabilitate ridicată de strângere) și unghiul de 45 °, atunci când pana este utilizată pentru a măsura direcția forței.
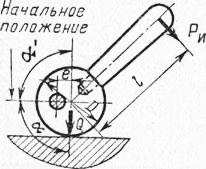
Fig. 5. Mecanismul excentric
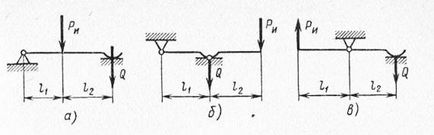
Fig. 6. Diagrame ale mecanismelor pârghiilor
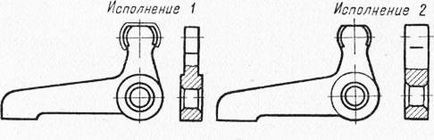
Fig. 7. Proiectarea manetei de unghi
Ca un exemplu, Fig. 7 prezintă proiectarea brațului unghiular. Aplicarea dispozitivului de antrenare (pneumatică, hidraulică, pneumohidraulică, electrică, magnetică, electromagnetică, vid) permite creșterea vitezei dispozitivelor de prindere și creșterea forței de fixare. În unele cazuri, mai multe dispozitive de prindere funcționează de la o singură unitate.
Cele mai comune unități pneumatice. Motoarele de aer cu piston (pneumocilindere) asigură o curgere mare a tijei; durata lor de viață este de obicei de 10-15 mii de cicluri. Motoarele pneumatice cu membrană sunt fabricate cu o membrană din material cauciucat; durata lor de viață este de 0,5-1 milioane de cicluri; dezavantaje - cursa mică a tijei și dependența forței de poziția barei datorită rezistenței variabile a diafragmei. Servomotorul pneumatic cu burduf nu prezintă scurgeri, este ușor de fabricație.
Actuatorul este simplu în construcție și de încredere în funcțiune, dar are o dimensiune mare (deoarece aerul comprimat este furnizat sub presiune joasă de 0,4 - 0,63 MPa,) și generează zgomot în emiterea de evacuare a aerului.
Transmisia hidraulică are următoarele avantaje față de pneumatice: utilizarea fluidului de lucru sub presiune ridicată (până la 15 MPa) permite reducerea mărimii cilindrilor hidraulici; o linie hidraulică poate servi un grup de mașini; Fluidul de lucru (uleiul) nu provoacă coroziunea elementelor sistemului și în același timp servește ca lubrifiant; Acționarea hidraulică funcționează fără probleme și fără zgomot. Dezavantajele sistemului de acționare hidraulică sunt costul inițial ridicat, cerințe sporite de funcționare pentru a preveni scurgerile de ulei.
Direcția pneumo-hidraulică are, într-o oarecare măsură, avantajele acționărilor pneumatice și hidraulice. Aerul comprimat este furnizat cilindrului pneumatic, a cărui tija este pistonul cilindrului hidraulic. Uleiul din cilindru prin conducta intră în cilindrul hidraulic al dispozitivului. Cursa de întoarcere a cilindrilor are loc sub acțiunea arcurilor.
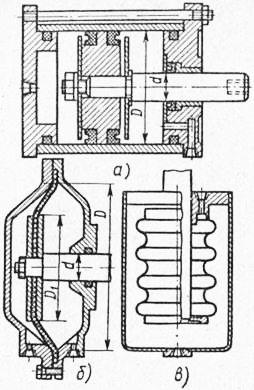
Fig. 8. Motoare pneumatice: a - piston, b - diafragmatice, ã - burdufuri
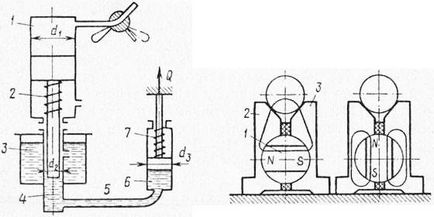
Fig. 9. Pneumohydraulic
Fig. 10. Unitatea de prisma magnetică
Fixarea barelor cu ajutorul unei transmisii electrice este promițătoare și este folosită pe scară largă în dispozitivele de prindere a liniilor automate. Pentru rotirea piuliței mecanismului de prindere al dispozitivului se folosește o cheie electrică fixă (cheie).
O aplicație largă pentru fixarea semifabricatelor pe măștile de suprafață a primit plăci și dispozitive electromagnetice și magnetice. În Fig. 10 prezintă schema prismei magnetice pentru fixarea pieselor cilindrice. În poziția orizontală a magnetului, fluxul de forță magnetică trece prin obrajii prismei, separat de o placă nemagnetică, și piesa de prelucrat. Cel din urmă, cu această poziție a magnetului, este presat împotriva prismei. Atunci când magnetul este rotit într-o poziție verticală, fluxul magnetic se închide prin obraji și piesa de prelucrat este eliberată.
Elemente de unelte pentru ghidarea și instalarea uneltelor de tăiere. Reglarea și ajustarea sistemului tehnologic la dimensiune cu ajutorul încercărilor și măsurătorilor durează mult timp și nu este posibilă în toate procesele de prelucrare. Cu ajutorul unor dispozitive precum șabloanele și instalațiile, acest proces poate fi accelerat. Utilizate în mod special pe scară largă sunt setările pentru reglarea dispozitivelor de frezat.
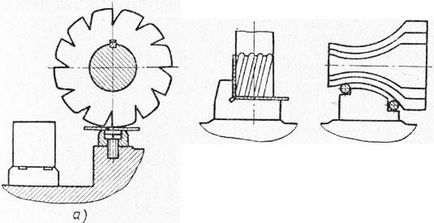
Fig. 11. Schema de instalare a unui sistem tehnologic de frezare a semifabricatelor cu sonde și instalații: a, d-înalt, b-unghiular, în formă de C
Prelucrarea pe mașinile de copiatoare se efectuează prin intermediul copiatoarelor. Ele sunt utilizate, de asemenea, în prelucrarea pe mașini de frezat, de strunjire, de frezat, de șlefuit și alte mașini. Copiatoarele și rolele sunt fabricate din oțel 20X; ele sunt cimentate și stingite până la o duritate de 56-61 HRC.
Bucșelor conductoare sunt proiectate pentru orientarea și direcția instrumentelor axiale (burghie, carote, alezoarelor, și așa mai departe. D.). Aplicați manșon fix-fix rapid, detașabil, și de construcții. manșon Constant (fără guler - tip I, cu guler - tip II) este utilizat în cazul în care dispozitivul în timpul utilizării este mai mică decât intervalul de timp în care se pot produce uzura manșon. Producția de serie și de masă este utilizat manșon interschimbabil. Schimbare rapidă manșon este utilizat pentru procesarea în serie (de foraj, frezat, scanare), o gaură cu o singură piesă de montare. procesare specială permite alezajul manșon într-un plan înclinat, o nișă sau găurile strâns distanțate.
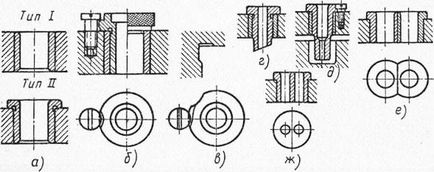
Fig. 12. Bucșe pentru dirijarea orificiilor cu ajutorul unei scule axiale
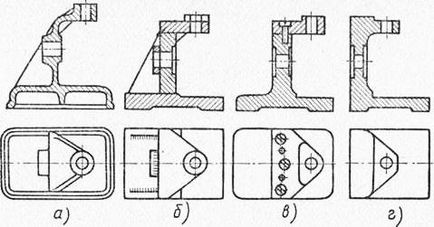
Fig. 13. Variante ale construcției corpului conductorului pentru diverse metode de fabricare a acestuia: a-turnare, b-sudura, c-asamblare, d - dintr-o țiglă turnată standard
Cazuri pentru aparate. Toate elementele dispozitivului sunt plasate și fixate pe corpul său. Deoarece corpul dispozitivului percepe toate forțele care acționează asupra piesei de prelucrat în timpul fixării și prelucrării sale, aceasta trebuie să aibă o rezistență suficientă, rigiditate și rezistență la vibrații. Aceste calități sunt oferite de alegerea unui design racțional al coca și, în primul rând, de introducerea rigidizărilor.
Diferite variante ale corpului conductorului sunt prezentate în Fig. 13.
Carcasele turnate și părțile corpurilor prefabricate se disting, de obicei, de fonta din MF 12 și MF 15. Turnarea oțelului este folosită mai rar. Pentru producția de corpuri sudate se folosește oțel.
Citește mai mult:
Articole similare:
Articole similare
Trimiteți-le prietenilor: