Repararea morilor de bile cu tuburi. Caracteristicile reparației lor.
Vedeți întrebarea 31.
După curățare, piesele sunt verificate și sortate (defecte).
Defect-determinarea stării tehnice a pieselor; sortarea lor în formă, necesitând reparații și inutilizabile; Determinați ruta pentru piesele care necesită reparații.
Piesele potrivite sunt cele în care abaterile de mărime și formă se află în limitele uzurii admise specificate în condițiile tehnice pentru repararea mașinii.
Sub rezerva reparării sunt părți ale căror uzuri sunt mai mari decât cele admise sau există alte defecte recuperabile.
Detaliile necorespunzătoare sunt cele a căror recuperare este imposibilă sau impracticabilă din punct de vedere economic din cauza uzurii ridicate și a altor defecte grave (deformări, fracturi, fisuri).
Motivele pentru sacrificarea pieselor sunt, în principal, diferite tipuri de uzură, determinate de următorii factori:
constructiv - schimbarea limita a dimensiunilor părților este limitată de forța lor și cu schimbarea constructivă a cuplării;
Tehnologică - limitarea detalii limitate redimensionare performanțe nesatisfăcătoare ale funcțiilor sale de serviciu, în ansamblul sau unității (de exemplu, uzura Angrenajele pompei nu furnizează presiune sau performanța de descărcare și altele.);
calitativ - modificarea formei geometrice a pieselor în timpul uzurii afectează funcționarea mecanismului sau a mașinii (uzura ciocanelor, obrajilor de concasoare etc.);
economice - reducerea admisibilă a dimensiunilor pieselor este limitată de o scădere a productivității mașinii, o creștere a pierderii puterii transmise prin frecare în mecanisme, o creștere a consumului de lubrifiant și alți factori care afectează costul lucrării.
Defectele detaliilor echipamentului se efectuează în conformitate cu condițiile tehnice, care includ: caracteristicile generale ale piesei (material, tratament termic, duritate și dimensiuni de bază); Posibile defecte, admisibile fără dimensiuni de reparații; dimensiunea maximă admisă a părții pentru reparații; semne de căsătorie finală. În plus, în condițiile tehnice sunt date indicații ale abaterilor admisibile față de forma geometrică (ovalitate, conic).
Condițiile tehnice ale defecțiunii sunt realizate sub formă de cărți speciale, în care, pe lângă datele enumerate, se indică metode de reparare și reparare a pieselor.
Datele din specificațiile tehnice referitoare la valorile admisibile și limită ale uzurii și mărimii trebuie să se bazeze pe
Studiul uzurii, luând în considerare condițiile de lucru ale pieselor.
Părțile sunt defecte și monitorizate vizual și cu ajutorul unui instrument de măsurare și, în unele cazuri, cu ajutorul dispozitivelor și al instrumentelor de măsură. Verificați vizual starea tehnică generală a pieselor și identificați defectele externe vizibile. Pentru o mai bună detectare a defectelor de suprafață, se recomandă curățarea temeinică a suprafeței și apoi etanșarea acesteia cu o soluție de acid sulfuric de 10-20%. În plus, în metoda vizuală, defectele sunt detectate prin atingerea și simțirea detaliilor.
Controlul defectelor ascunse se realizează de ani de zile hidraulice, pneumatice, magnetice, luminescente și ultrasonice, precum și de raze X.
Metodele defectelor hidraulice și pneumatice sunt folosite pentru a verifica detaliile și ansamblurile pentru etanșeitate (etanșeitate la apă și gaze) și pentru a descoperi fisuri în părțile corpului și în vase. Pentru a face acest lucru, utilizați standuri speciale echipate cu rezervoare și sisteme de pompare.
Metoda magnetică de defectare a pieselor se bazează pe apariția unui câmp de dispersie magnetică pe măsură ce trece printr-o parte defectă de flux magnetic. Ca urmare, direcția liniilor câmpului magnetic se schimbă de-a lungul acestor suprafețe sub aceste defecte (Figura 22) datorită permeabilității magnetice inegale.
/ Controlul proceselor - detectarea defectelor de suprafață a părții acoperite cu pulbere feromagnetică (calcinat oxid de fier-Crocus) sau o suspensie formată din două părți de kerosen, o parte din ulei de transformator și 35-45 g / l melkodroblenogo pulbere feromagnetică (scorii (Fisuri, etc.) ). Pentru detectarea mai precisă a perturbațiilor câmpului magnetic asupra detaliilor ușoare, se recomandă utilizarea pulberilor magnetice negre, pe suprafețe întunecate - roșii. Acest tip de control este mai sensibil în detectarea defectelor interne ale piesei și este utilizat pentru caracteristici magnetice necunoscute ale materialului piesei.
2 metodă de control - identificarea fisurilor de suprafață și a părților mici și mijlocii, realizate numai din oțeluri cu conținut ridicat de carbon și aliate. Este mai eficientă și mai convenabilă decât prima metodă. Pentru o mai bună detectare a defectelor, se folosesc diferite tipuri de magnetizare a pieselor. Crăpăturile transversale sunt mai bine identificate când
magnetizarea longitudinală și longitudinală și amplasată la un unghi - cu magnetizare circulară.
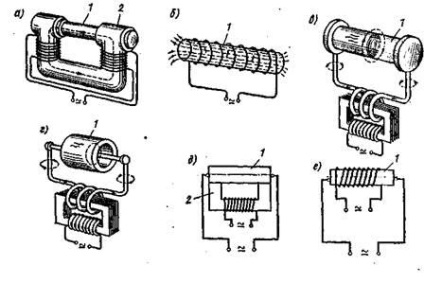
Fig. 23. Scheme de metode de magnetizare a pieselor:
După detectarea defectelor magnetice, piesele trebuie clătite într-un ulei de transformare curat și demagnetizate. Schema defectoscopului magnetic este prezentată în Fig. 24. Dispozitivul constă dintr-un dispozitiv de magnetizare 2, un starter magnetic 3 și un transformator 4.
Dispozitivul pentru magnetizarea circulară este un raft la care este fixată o masă cu o placă de cupru inferioară de contact și un cap mobil cu un disc de contact care se deplasează de-a lungul coloanei. Poz. 1 este strâns strâns între placa de contact și placă și include un transformator (sau acumulator). Curentul de transformator de tensiune înfășurarea secundară 4-6 V este aplicată pe placa de cupru și discul de contact și în contact cu piesa de prelucrat 1 se produce magnetizare, care dureaza 1-2 secunde. Apoi, partea este imersată într-o baie cu suspensie timp de 1-2 minute, scoasă și examinată pentru a determina locațiile defecțiunii.
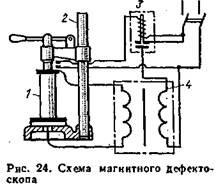
La întreprinderile de reparații, magnetice universal
detector de defecte de tipul M-217, care permite efectuarea magnetizării circulare, longitudinale și locale, controlului magnetic și demagnetizării.
Defectoscopul constă dintr-o unitate de alimentare care creează un câmp magnetic, un dispozitiv de magnetizare (contacte și un solenoid) și o baie pentru o suspensie magnetică.
De asemenea, industria produce și alți detectoare magnetice: staționare - MED-2 și 77 PMD-ZI, precum și portabile 77MD-1SH și PPD semiconductoare.
Detectoarele defectuoase portabile vă permit să controlați piese direct pe mașini, în special părți mari, care sunt dificil sau imposibil de îndepărtat și de a investiga folosind instalații staționare.
Prin metoda detectării defectelor magnetice pot fi controlate numai componente din oțel și fontă, instalând defecte externe și interne de până la 1-10 microni.
piese luminescente Metodă de control bazată pe capacitatea anumitor substanțe fluorescențe (absorbi) energia radiantă și eliberați-l sub formă de radiație luminoasă pentru un timp sub excitare cu raze ultraviolete ale substanței invizibile.
Această metodă dezvăluie defectele de suprafață, cum ar fi fisurile părului, asupra detaliilor materialelor nemagnetice. Pe suprafața părții cercetate se aplică un strat de lichid fluorescent care penetrează în toate defectele de suprafață într-o perioadă de JO-15 minute. După aceea, lichidul în exces este îndepărtat de pe suprafața piesei. Apoi
un strat subțire al pulberii în dezvoltare se aplică pe suprafața șters, care atrage din fisuri și alte defecte lichidul fluorescent care pătrunde în acesta. După iradierea suprafeței părții cu lumină ultravioletă, locurile de la care a fost aspirat lichidul fluorescent încep să strălucească, indicând localizarea defectelor de suprafață.
Ca un lichid fluorescent, un amestec de 85% kerosen și 15% ulei mineral cu viscozitate redusă cu adăugarea a 3 g pe litru de emulgator OP-7 și care prezintă pulberi constau din oxid de magneziu sau selikogelya. Sursele de lumină ultravioletă sunt mercur tip lampă de cuarț PRK-1, 4-PRK, 77PLU SVDSH-2 și cu un filtru special de culoare UFS-3. De asemenea, se aplică
instalare portabilă LYUM-1 și detector defect staționar LDA-3.
Cu ajutorul metodei luminiscente, este posibil să se determine defectele de suprafață cu dimensiuni de 1-30 μm.
Metoda de inspecție cu ultrasunete se bazează pe reflectarea vibrațiilor cu ultrasunete de la defectele interne existente ale piesei când acestea trec prin metal datorită unei schimbări bruște a densității mediului.
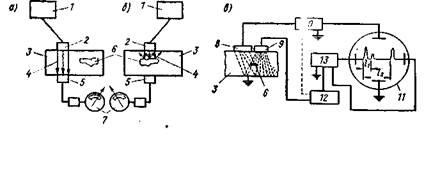
Fig. 25. Scheme de acțiune a detectoarelor de defecte ultrasonice:
a-o metodă de umbră (un defect nu este detectat); b-metoda de afiare (defect detectat);
• - metoda de reflecție
În industria de reparații, există două moduri de detectare a erorilor cu ultrasunete: umbra de sunet și reflexia impulsurilor (semnale). În metoda acustică (figura 25, a, b), generatorul ultrasonic / acționează pe placa piezoelectrică 2, care în
rândul său, acționează pe partea investigată 3. În cazul în care defectul este 6, acestea se vor reflecta nu cad pe placa piezoelectric a primit 5, ca urmare a unei umbre defect va apărea, care marchează dispozitivul de înregistrare pe calea undelor ultrasonice 4 7. "
În metoda de reflexie (Fig. 25c) de la generatorul 12 prin piezoelectric emițător val de ultrasunete 9 sunt transmise la elementul 3, trecându-l și reflectată de la capătul opus, revenind la sonda receptoare 8. Când defect 6, impulsuri reflectate ultrasunete inainte. Atașat la stiloul de recepție
8 și convertite în semnale electrice, impulsuri sunt alimentate printr-un amplificator 10 la tubul catodic 11. Cu generatorul mătura ajutor 13 include un generator 12 simultan, semnalele obținute fasciculului de scanare orizontală pe ecranul tubului 11 unde pulsul inițial are loc într-un vârf vertical. Reflectat de la defect, undele se întorc mai repede și un al doilea impuls apare pe ecran, la o distanță / j de la primul. Al treilea impuls corespunde semnalului reflectat de partea opusă a părții. Distanța / 2 corespunde grosimii piesei, iar distanța / t corespunde cu adâncimea defectului. Măsurarea timpului din momentul trimiterii impulsului la momentul primirii ecoului vă permite să determinați distanța la defectul intern.
Pentru scopuri de întreținere defect ultrasonic îmbunătățit SPL-7H configurat prin schema de impulsuri și permite un control al articolelor prin metoda semnalelor reflectate precum și metoda prin transiluminare (umbră acustic).
Adâncimea maximă de penetrare pentru oțel este de 2,6 m pentru plat și 1,3 m cu sonde prismatice, adâncimea minimă fiind de 7 mm. Mai mult, industria noastra produce ultrasunete defect DUK.-5B, 6B-CRF, SPL-YM et al. Cu o sensibilitate ridicată, care poate fi utilizat în industria de reparații.
Controlul razelor X se bazează pe proprietățile undelor electromagnetice, în moduri diferite, absorbite de aer și corpuri solide (metale). Radiațiile care trec prin materiale își pierd ușor intensitatea, dacă în calea lor există goluri în partea controlată sub formă de fisuri, cochilii și pori.
Razele de ieșire proiectate pe ecran vor afișa locuri întunecate sau mai luminate, care diferă de fundalul general.
Aceste spoturi și benzi de luminozitate diferită indică defecte în material. În plus față de raze X, raze de elemente radioactive - raze gamma (cobalt-60, cesiu-137, etc.) sunt utilizate pentru detectarea defectelor. Această metodă este complicată și, prin urmare, este rar utilizată în întreprinderile de reparații (pentru controlul cusăturilor în cazul cuptoarelor și laminoarelor rotative etc.).
Piese de depanare vopsea utilizate pe scară largă în practică în repararea echipamentelor de reparații la locul de instalare sau în condițiile sale starea de echilibru în controlul unei mari părți, cum ar fi rame, juguri, etc. carter.
Esența metodei constă în faptul că elementele de benzină suprafață de încercare degresate pătat .zhidkostyu luminos roșu special având higroscopicitate bună și penetrarea în cele mai mici defecte (timp de 10-15 min). Apoi, se spală părțile, iar ultima este vopsită cu un email nitro-alb, care absoarbe vopseaua care pătrunde în defectele piesei. Lichid, vorbind pe un fundal alb de detalii, indică forma și amploarea defectelor. Acest principiu se bazează pe definiția defectelor care utilizează stratul de kerosen și stratul de cretă.
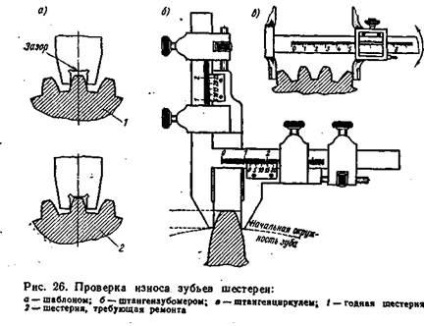
Axe. Cel mai des întâlnit defect al arborilor este curbura, uzura suprafețelor de fixare, canelurile cheii, firele, șanțurile, firele, gâturile și fisurile.
Îndoirea arborilor este verificată la centrele strungului sau strungului special pentru bătăi, utilizând în acest scop un indicator montat pe un suport special.
Ovalitatea și conicitatea gâturilor cotite sunt determinate prin măsurarea micrometrului în două secțiuni separate de fille la o distanță de 10-15 mm. În fiecare centură, măsurarea se face în două planuri perpendiculare. Dimensiunile limită ale scaunelor, canelurilor, canelurilor sunt estimate folosind brațele, șabloanele și alte instrumente de măsurare.
Fisurile din arbori sunt detectate de inspecție externă, detectoare de defecțiuni magnetice și alte metode. Axurile și axele sunt respinse dacă se constată fisuri de peste 10% din diametrul axului. Reducerea diametrului gurilor arborilor în canelură (șlefuire) în cazul unei sarcini de șoc este permisă nu mai mult de 5% și cu o încărcare liniștită, nu
mai mult de 10%.
Roți dințate. Adecvarea roților dințate pentru muncă este judecată în principal pe uzura dintelui în grosime (Figura 26). Dinții sunt măsurați în grosime prin intermediul barelor de măsură, danturii tangențiale și optice și a modelelor. Grosimea unui dinte de roată cilindrică
măsurată în două secțiuni. Fiecare roată dințată măsoară trei dinți situați unul la un unghi de 120 ° față de celălalt. Înainte de măsurare, cele mai uzate dinți sunt marcate cu cretă. Uzura maximă a grosimii dinților (pe cercul inițial) nu trebuie să depășească: pentru uneltele deschise (clasele III-IV). Pentru monitorizarea rulmenților de rulare, diferite tipuri de dispozitive sunt utilizate pentru a determina jocul radial și axial în rulmenți. Radial a)
Jocul este verificat utilizând dispozitivul prezentat în Fig. 27. Verificați setul inelului interior al lagărului de pe dorn și fixați cu o piuliță. Deasupra un capăt al tijei de 4 se reazemă inelul exterior al suprafeței de rezemare, iar celălalt - în minimeters picioarelor de control 5. sub un capăt al barei 2 se sprijină pe suprafața portantă a inelului exterior, iar celălalt capăt este conectat cu un sistem de pârghii. Tija 4 se extinde în tubul 3, iar tija 2 - în cap. Tubul 3 și tija 2 prin intermediul pârghiilor sunt conectate printr-o linie de 1-a lungul căreia se deplasează o încărcătură de marfă P. Dacă P este pe partea dreaptă, tubul 3 prese pe inelul exterior care poartă pe partea de sus - inelul este deplasat în jos, prin care tija 4 este de asemenea deplasat în jos și minimeters 5 fixați indicarea săgeții. Dacă sarcina P se deplasează spre partea stângă, tija 2 se apasă pe inelul exterior al lagărului - inelul se va deplasa în sus. Tija 4 se va deplasa, de asemenea, în sus, în timp ce citirea minimeterului este fixată din nou. Diferența dintre citirile acelui minimeter și va fi distanța radială în rulmentul care trebuie verificat.
Articole similare
-
Forța necesară este calculată pentru presarea pieselor asamblate conform formulei: industrie,
-
Cerințe de securitate pentru utilizarea scărilor de scară - stadopedia
Trimiteți-le prietenilor: