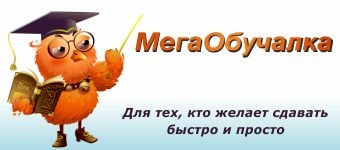
Acasă | Despre noi | feedback-ul
Supermarket în fabrică.
După ce a apărut în supermarket, sistemul de tragere a devenit bine stabilit în producție. Acest lucru se datorează faptului că vă permite să economisiți bani pentru completarea stocurilor. De ce să cumpărați exces și să păstrați în stoc, dacă nu există cerere. Când clientul comandă, linia de produse începe să funcționeze. În consecință, există o nevoie de materii prime sau de componente, iar furnizorilor li se dă un semnal. Sa dovedit a fi mai profitabil să cumpărați materii prime și componente în loturi mici. În acest caz, costul componentelor este crescut, dar fondurile înghețate sunt eliberate, cheltuielile pentru stocarea stocurilor, precum și a zonelor de producție sunt reduse.
Acest sistem a permis japonezilor, în special companiei Toyota, să evite multe probleme semnificative, inclusiv problema supra-producției. Există un semnal de pe piață - instalația funcționează, nu există semnal - sistemul a fost înghețat în anticipare. Desigur, plantele nu pot funcționa pe deplin doar în ordine. Există o prognoză și o planificare preliminară, dar sistemul de producție în ansamblul său este construit tocmai pe acest principiu. Mai mult decât atât, pre-planificare este direcționată mai degrabă decât resursele materiale și umane: cât de mulți lucrători, în ce perioadă va trebui să ridice o suplimentare, dacă este necesar, extinderea producției în legătură cu dezvoltarea în continuare a companiei.
Introducerea unui sistem de tragere presupune, de fapt, principiul Jast-in-time (exact la timp), care este folosit pentru prima oară pe plan intern. Toate procesele sunt depanate, în care site-ul anterior de producție este furnizorul, iar ulterior - clientul. Dacă acest sistem este configurat în cadrul companiei, acest lucru va oferi avantaje evidente. Alinierea fluxului va reduce rezervele inter-operaționale, ceea ce va reduce timpul de producție, va crește cifra de afaceri a fondurilor.
Cu toate acestea, acest sistem de tragere nu este complet liber de stoc. Deoarece este necesar să se răspundă rapid la semnalul de pe piață, întreprinderea are încă un stoc sub forma unei lucrări în curs. La sosirea comenzii, debitul este imediat activat, producând cantitatea potrivită de produse.
Practic, toate întreprinderile care funcționează în conformitate cu schema tradițională sunt aranjate în conformitate cu principiul unui sistem de flotabilitate. Este o practică obișnuită de a oferi un program de lucru de sus pentru fiecare loc de producție pe baza unui plan general. Fiecare loc de producție tinde să obțină singuri indicatorii stabiliți: este necesar, produsul nu este necesar în stadiul actual al produsului, acesta este împins în etapa următoare de prelucrare. În plus, metoda de linie în cazul în care nu a organizat (a făcut un detaliu - trece de-a lungul liniei), iar produsul este prelucrat loturi, timp pentru a crea unitatea de produs, în funcție de mărimea partidului, este în creștere exponențial.
Pentru claritate, puteți efectua un simplu experiment. Sarcina este de a produce un lot de cinci produse. În acest caz, va fi de cinci bucăți de hârtie, fiecare dintre acestea trebuie să fie scrise în numele fiecăruia dintre cei trei participanți la experiment. Prima variantă a organizării producției noastre experimentale: primul participant, la rândul său, primește cinci foi. El trebuie să-și scrie propriul nume pe fiecare dintre ele și numai apoi să transfere setul mai departe. Și așa, până când partidul este în mâinile fiecăruia dintre participanți. A doua opțiune este din nou pe cele cinci foi ale experimentului, participanții scrie numele lor, dar trec reciproc foile la un moment dat (numele scris pe o singură coală - io întinse la alta). Se măsoară timpul de producție al unui lot de hârtie cu nume în ambele cazuri. Evident, ca rezultat, procesul care are loc în conformitate cu al doilea plan este realizat de mai multe ori mai repede.
Echipament Dezechilibrul duce la faptul că există, pe de o parte, întârzieri din cauza lipsei de materii prime, ca urmare a funcționării rapide a unei porțiuni, pe de altă parte, o porțiune mai puțin eficientă nu poate face față cu tratarea produsului format de aprovizionare interoperabilă, costurile de resurse. În cele din urmă, acest lucru duce la pierderi nerezonabile, care în cele mai multe cazuri nu sunt nici măcar luate în considerare. Fiecare locație deține o apărare circulară, declarând că se confruntă cu implementarea planului, dar întreprinderea în ansamblu nu funcționează eficient, ducând pierderi mari.
Lucrul cu unitățile de produs de pe un sistem de tragere accelerează fluxul produsului. În plus, pierderile din timpul de producție, stocurile excedentare care fac multe produse, sunt necunoscute și dacă acest lot va fi necesar la sfârșitul procesării, dacă acesta va fi revendicat de client.
Kanban și configurarea sistemului
În procesul de implementare a sistemului de tragere, a apărut întrebarea: cum să raportați că componentele se epuizează și că aveți nevoie de reaprovizionarea stocului. A devenit evident că este necesar să se dezvolte un anumit sistem de semnalizare care să permită monitorizarea acestuia, în ce domenii de producție și în ce cantitate este necesar. Apoi a fost dezvoltat sistemul Kanban, care în japoneză înseamnă "carte". (Cuvântul este dat în transcripția latină). De fapt, fabricile japoneze au folosit cărți, pe care au fost înregistrate informații despre reaprovizionarea stocurilor.
În timp, Kanban sa transformat, luând o varietate de forme. Acesta poate fi doar un container gol, așezați delimitat pe podea, o cutie în cazul în care sunt plasate aplicația corespunzătoare, sau la nivelul indicat în containere sau cutii, realizarea acestui nivel înseamnă că este timpul pentru a aduce componente sau materii prime.
După introducerea Kanban în interiorul întreprinderii, Kanban a fost dezvoltat pentru furnizor. Materiile prime sau componentele au început să fie furnizate numai printr-un semnal de la producție, ceea ce a permis reducerea semnificativă a stocurilor de materii prime și stocurile de produse finite din depozit pentru a se reduce la aproape zero. În consecință, resursele au fost eliberate, eficiența companiei a crescut, profitul a crescut. Cifra de afaceri a fondurilor a crescut datorită reducerii stocurilor și timpilor de execuție, deoarece timpul de nefuncționare datorat lipsei de componente a fost eliminat.
Pentru organizarea sistemului Kanban în întreprindere, este necesar, în primul rând, pentru a construi un flux care este o stare a tuturor unităților atunci când produsele fără întârziere transferate de la o zonă la alta, și în al doilea rând, să se găsească un echilibru de echipamente și fiecare individ proces în acest thread. În plus, este necesar să se organizeze procesul de creare a unui produs astfel încât rezervele inter-operaționale să nu se acumuleze. Am făcut un detaliu - treceți-l! Acest lucru va ajuta la reducerea timpului de trecere a produselor prin secțiuni de două sau de mai multe ori.
Nu toate întreprinderile au posibilitatea de a construi imediat o linie neîntreruptă între locurile de producție. Există probleme cu reglarea echipamentului pentru fabricarea altor produse sau cu echipamente vechi, care nu pot fi reconfigurate adesea.
Unele fluxuri depind de materiile prime, de la topirea în cazul producției metalurgice, unde există anumite procese tehnologice, ceea ce reprezintă o limitare a capacității de a construi un flux. De exemplu, producția tuturor produselor fabricii de anvelope Yaroslavl depinde de magazinul în care cauciucul este gătit printr-o tehnologie destul de complicată. La astfel de site-uri, se creează un depozit bine controlat, numit în mod convențional un supermarket, care păstrează o aprovizionare optimă a materiilor prime, produse intermediare, sau în curs de execuție, astfel încât sistemul poate funcționa fără întârziere (în cazul nostru, această porțiune poate fi în etapa de ambalare a produsului, în cazul în care vor exista tot felul de ambalaje). Debitul este construit de la locul unde începe producția unui produs.
Există anumite limitări privind caracteristicile tehnologice ale echipamentului. De exemplu, dacă comandăm recipiente de sticlă, echipamentul poate produce o cantitate minimă de 50.000 de sticle. Dacă vorbim despre procesul de asamblare, desigur, putem construi un flux și acest lucru va da rezultate tangibile. Un exemplu perfect de organizare a producției în unele plante „General Electric“, fluxul de companie este aranjată prin intermediul Snap-in, care este ca o formă de potcoavă. Primul lucrător ia o clipă, se trage pe element, își desfășoară activitatea, și transmite următoarea parte cu lucrător clipă. Când elementul trece întregul ciclu, produsul a fost retras și transferat la etapa de ambalare, conducta de transport și fixați înapoi la partea de sus a fluxului. Nu există trafic excesiv. Cutii cu detaliile sunt pe cutiile de carton pentru detaliu a fost la un nivel confortabil pentru mână, să nu fie distras de la proces și petrece timpul minim pe ea (aceasta se referă la organizarea efectivă a locului de muncă, importanța și punerea în practică). Compania lucrează la acest sistem timp de opt ani. Perfecțiunea producției este continuă. Zona de lucru a fost redusă cu 70%, iar volumul producției a crescut.
Articole similare
Trimiteți-le prietenilor: