Principiile procesului de sudare rezistență și o idee generală a soiurilor sale
Soiurile procesului de sudare a contactului
Spot Welding
Sudarea prin puncte este o metodă de sudare a contactului, în care piesele sunt sudate în zone separate de acces restricționat (pe un număr de puncte).
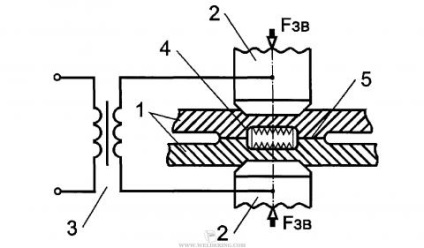
Când a fost colectat piese de sudură la fața locului 1 tur este comprimat între doi electrozi la care este conectată o sursă de energie electrică 3 (de exemplu, un transformator de sudura). Părțile sunt încălzite prin trecerea scurtă a curentului de sudură până la formarea unei zone de topire reciprocă a părților 4, numită miez. Încălzirea zonei de sudură este însoțită de o deformare plastică a pieselor metalice în zona de contact (în jurul miezului), unde se formează banda de etanșare 5, protejează fiabil metalul topit din plescăitul și aerul ambiental. Prin urmare, nu este necesară o protecție specială a zonei de sudură.
După oprirea curentului, metalul topit al miezului cristalizează rapid și se formează legături metalice între părțile care urmează să fie unite. Astfel, formarea unui compus în sudură la fața locului are loc prin topirea metalului.
Sudarea prin sudare
Sudarea prin sudare este o metodă de obținere a unei îmbinări etanșe (cusătura) prin formarea unei serii de puncte de suprapunere.
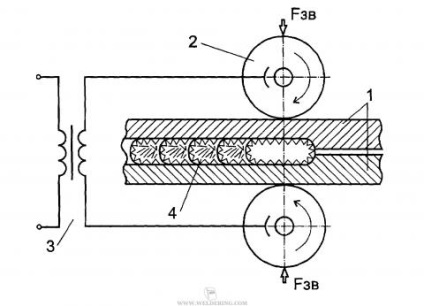
alimentarea cu curent și mișcarea pieselor se realizează prin rotirea electrozi disc - rola 2. Deoarece sudare, partea 1 este colectat și lap încălzit impulsuri tranzitorii pe sudura sursa de curent 3, formând astfel o serie de suprapunere puncte 4.
Scule de sudură
Soluția de sudură este unul dintre tipurile de sudare la fața locului.
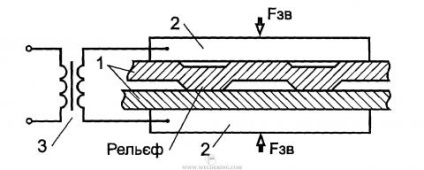
În același timp, o proeminență este preformată pe suprafața uneia dintre părțile 1, o relief care limitează zona de contact inițială a pieselor. Ca urmare, densitatea curentului și rata de eliberare a căldurii cresc în această zonă. Când se încălzește, relieful se deformează treptat; La o anumită etapă a procesului de sudare, se formează un miez, la fel ca la sudarea convențională la fața locului. Comprimarea pieselor 1 și a tensiunii de sudare la acestea se efectuează cu ajutorul plăcilor 2.
Butt Welding
Metoda de sudare prin sudură a contactului, atunci când piesele sunt conectate pe întreaga zonă de contact (pe întreaga secțiune).
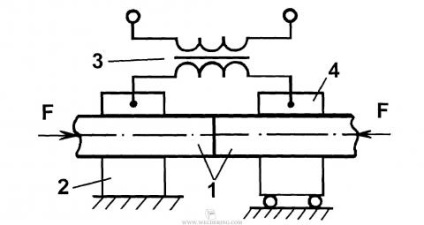
Părțile 1 sunt fixate în terminalele 2 și 4 care transportă curentul, dintre care unul (4) este mobil și conectat la acționarea forței de compresie a mașinii. Tensiunea la componente este furnizată de la sursa 3.
În cazul sudării cu cap de rezistență, piesele sunt comprimate preliminar prin forță și un transformator de sudură este inclus în rețea. Curentul de sudare curge prin părți și are loc o încălzire treptată a articulației pieselor la o temperatură apropiată de temperatura de topire. Apoi, curentul de sudare este oprit și forța pescajului este intens crescută, care se deformează la joncțiune. În același timp, filmele de suprafață sunt parțial extrudate din zona de sudare, se formează un contact fizic și se formează o conexiune.
La sudarea cap la cap prin refolosire, tensiunea din transformatorul de sudură este aplicată mai întâi pe partea respectivă și apoi sunt reunite. Când piesele intră în contact în contacte individuale datorită densității mari a curentului, metalul de contact se încălzește rapid și explodează exploziv. Încălzirea capetelor părților se face datorită formării continue și distrugerii contactelor - jumperi. La sfârșitul procesului se formează un strat continuu de metal lichid la capete. În acest moment, creșterea bruscă a vitezei de apropiere și a forței de tragere F a pieselor; capetele se închid, cea mai mare parte a metalului lichid, împreună cu peliculele de suprafață și o parte din metalul dur, sunt stoarse din zona de sudare, formând un strat de îngroșare. Curentul de sudură este oprit automat în timpul proiectării pieselor. Pentru o mai bună încălzire a părților de-a lungul secțiunii și obținerea unor proprietăți omogene ale îmbinărilor, în unele cazuri înainte de începerea refolosirii, capătul este încălzit de curent prin rezistența la sudură.
Șunt curent. Șuntare curent manifestată în parte a curentului care circulă în afara zonei de sudură, de exemplu, prin punctele anterior sudate pentru sudare cu două fețe sau printr-una dintre piesele cu sudura unilateral la sudarea cusătură, sudarea cap la cap a produselor cu o formă închisă. Măsurarea în mare măsură a simetriei câmpului electric poate conduce la o scădere a densității de curent. Curenții de șunt sunt de obicei reduse în timpul sudării prin încălzirea șuntului și reducerea rezistenței electrodului-electrod.
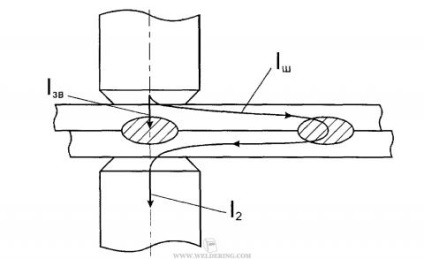
Rolul deformării plastice
Deformarea plastică a metalului este cauzată atât de factori externi, de forța pe partea electrozilor, cât și de solicitările interne care rezultă din expansiunea liberă a metalului zonei de sudare. Cu rezistență la sudură, cusătură, relief și sudură la cap, deformarea plastică a metalului este prezentă pe parcursul întregului proces de sudare: de la formarea unui contact rece la forjarea îmbinării. La sudare prin refolosire, deformarea are loc în timpul etapei de preîncălzire și precipitare.
Rolul principal al deformarea plastică a locului, sudarea cusătură și proiecția constă în formarea unui contact electric, în formarea unei centuri de plastic pentru reținerea metalului topit din plescăitul și limitele de răspândire a curentului de sudare în contactul interior, garnitura de metal în faza de răcire.
Principalul rol al deformării plastice la sudarea cap la cap este eliminarea oxizilor pentru a forma legături metalice în îmbinare (etapa a doua a ciclului de sudare) și contactele electrice (în special în timpul primei etape de încălzire). Deformarea este cauzată de acțiunea forței de compresie creată de antrenarea mașinii de sudură. Pentru a forma contactul electric inițial, este suficientă o mică presiune, la care are loc deformarea microplastică a reliefului de suprafață al capetelor. Pentru a elimina oxizii și a forma legături, este necesară o deformare plastică a volumului relativ mare a pieselor. Dar sudarea cap la cap în majoritatea cazurilor folosește o schemă liberă de deformare a volumului, în care fluxul de metal curge fără nici o restricție externă. În procesul de sudare la cap, magnitudinea deformării este judecată prin scurtarea părților cauzate de pescaj.
Defecte ale îmbinărilor și cauzele formării lor în sudură de contact
Principalele defecte ale sudării în puncte, cusături și reliefuri sunt:
- Lipsa de penetrare - apare ca o reducere sau absenta completa a unui miez de turnare, precum și păstrarea parțială sau totală a filmului de oxid sau stratul de placare în contact element cu element; stropiri, zona discontinuități sudare (fisuri, chiuvete), reducerea compușilor cu rezistență la coroziune, efectele adverse ale structurilor metalice. Lipsa totală a rațiunii de fuziune - pentru a schimba parametrii de sudare (scădere curent și de sudare de timp, creșterea forței de comprimare și diametrul electrozilor) precum și alți factori tehnologici (suprapunere mică, distanța dintre punctele, lacune mari), ceea ce duce la o scădere a densității de curent (generarea de căldură).
- Stropirea este evacuarea unei părți din metalul topit din zona de sudură. Stropirile sunt împărțite în exterior (din zona de contact a părții electrodului), intern (între părți), inițial (în prima etapă a formării conexiunii) și final (în etapa a II-a). Cauza generală a apariției acestui defect este întârzierea în viteza de deformare față de viteza de încălzire.
- Neconcordanțele zonei de sudare. crăpături externe și interne, cochilii. Fisurile sunt calde și se formează în principal în intervalul de temperatură a fragilității.
- Reducerea rezistenței la coroziune a articulațiilor - are loc ca urmare a transferului unei părți din metalul electrodului pe suprafața dentară și poate provoca o coroziune crescută în această parte a îmbinării.
- Modificări nefavorabile în structura metalului de sudură - apar ca urmare a ciclului de sudare cu deformare termică.
Principalele defecte ale sudării cap la cap:
- Dezghețarea este absența completă sau parțială a unei legături metalice. Motivul eșecului este prezența oxizilor în îmbinarea sau încălzirea insuficientă a capetelor.
- Curbura fibrelor în zona de îmbinare este observată de obicei cu o pantă excesivă.
- Laminările și crăpăturile (de obicei, la cald longitudinal) au loc și cu o pantă excesivă.
- defecte structurale (contaminare mare de cereale prin interfata incluziuni nemetalic, reducerea conținutului de elemente de aliere în joncțiune, etc ...) - poate fi cauzată de supraîncălzire a metalului, prin oxidare în timpul sudurii, elemente de aliere burnup.
Domeniile de aplicare ale proceselor de sudare a contactului și principalele probleme
Sudarea cu puncte și cusături conectează de obicei piesele cu o grosime de 0,5-6 mm. Grosimea pieselor care trebuie sudate poate fi aceeași sau diferită. Materialul pieselor poate fi omogen sau eterogen. Dacă nu este necesară etanșeitatea, se folosește sudarea la fața locului. Îmbinările strânse sunt realizate prin sudură cu cusături.
Cu acces limitat la locul de sudare, este utilizată o sursă de curent unică. Pentru a îmbunătăți productivitatea și a reduce rănirea, utilizați sudarea în mai multe puncte.
Sistemele de sudură prin sudură conectează, de obicei, părți dintr-o secțiune mică, de obicei rotundă (de exemplu, oțeluri cu conținut redus de carbon nu mai mari de 200 mm2).
Cu sudare prin sudare continuă până la 1000 mm2 (din oțel cu conținut scăzut de carbon) și sunt sudate părți ale unui perimetru mare (țevi, foi etc.).
Echipamente și accesorii
Pentru mașinile cu scop general GOST 297 -80 stabilește, în special, următorii parametri de bază.
- Cel mai înalt curent secundar. Acest curent curge în secundar (sudură) circuitul când scurtcircuitat la nivelul maxim de control pentru soluția nominală și circuitul de sudare de plecare.
- Forța nominală și (sau) cea mai mică și cea mai mare de compresie a electrozilor - pentru mașinile de punctat, sutură și de relief.
- Cerințe pentru parametrii geometrici ai electrozilor și console de mașină (dimensiuni de contur sunt cei mai importanți parametri ai mașinii, contururile sunt formate din elemente de transport al curentului rigide și flexibile care fac legătura între înfășurările secundare ale transformatorului la mașinile de sudură scule).
Echipamentul mașinilor include console, suporturi pentru electrozi, electrozi, bureți pentru transportul curentului și alte elemente ale căror dimensiuni și design pot varia în funcție de designul produsului. Pe aceste elemente, uneori atașamentele fixează sau susțin piesele sudate, încărcăturile sau mecanismele detașabile. Circuitul secundar este caracterizat de următorii parametri:
- rezistență activă;
- rezistență inductivă;
- impedanță în modul de scurtcircuit.
Compoziția mașinilor pentru puncte, relief, suturi, suspensii și multi-electrod include unități de comprimare. În timpul perioadei de curgere a curentului de sudură, aceste acționări formează forța de sudare constantă sau în funcție de timp pe electrozii. Acolo unde este necesar, aceste unități furnizează electrozii forță precomprimarea (pentru comutarea curentului) și forța de forjare (după scoaterea) în plus față de nivelul de forță de sudare. În majoritatea mașinilor, unitățile de comprimare sunt pneumatice, mai puțin adesea încărcate cu arc.
Mecanismul de rotație a rolelor mașinilor de cusut - asigură deplasarea pieselor sudate cu un pas de puncte. Rotirea rolelor poate fi continuă și intermitentă. Unitatea poate fi una dintre role, iar în unele cazuri cuplul este transmis direct la ambele role.
Dispozitivele de sudură prin electrozi și rolele de sudură constau în: o piesă de lucru, o parte care asigură conectarea la mașină și o parte intermediară (principală). Partea de lucru asigură un contact direct (electrice și mecanice) cu piesele de electrod sudate și are o suprafață de lucru, forma și dimensiunile care sunt caracteristicile tehnologice importante ale electrodului (cu role). În prezent, două forme ale suprafeței de lucru sunt cele mai obișnuite: plate (cilindrice în role) și sferice. Funcția principală a electrozilor și a rolelor este de a furniza curentul pieselor și de a transfera forța de sudare asupra lor. Interiorul celor mai multe electrozi de sudură pe loc are un canal pentru alimentarea apei de răcire. În interiorul canalului de răcire este un tub prin care intră apa.
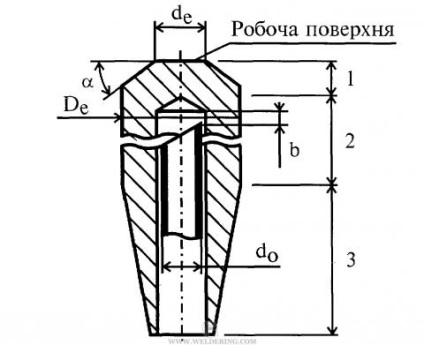
Parametrii modului de sudare
În funcție de rolul proceselor de disipare a căldurii și de eliminare a căldurii, se disting regimurile de sudare dure și moi.
Modul dur este caracterizat de o valoare ridicată a curentului de sudură și de un timp scurt de sudare. Modul dur este caracterizat de rate mari de încălzire și de răcire. Astfel de regimuri se utilizează la sudarea materialelor cu conductivitate termică ridicată și rezistență electrică scăzută.
Modurile modulare sunt caracterizate de o durată semnificativă a fluxului de curent relativ redus. În acest caz, schimbul considerabil de căldură are loc în interiorul pieselor și cu electrozi.
Ciclul punctului de contact și sudarea reliefului constă în comprimarea preliminară, încălzirea și forjarea.
Când rezistența la sudare parametrii de mod de bază sunt curent de sudare, sau densitatea de curent, timpul de curgere curent, forța de compresiune inițială și forța supărat, scurtarea pieselor de sudat, lungimea de instalare (distanța inițială dintre marginile interioare ale cablurilor de curent).
Setările de bază pentru fuziunea de sudură: rata de fuziune, densitatea curentului la topire, alocația fuziune, timp reflow, valoarea depresiunii și viteza, durata de precipitații sub tensiune valoarea curentului de precipitare, precipitare sau forță de presiune precipitații, lungimea localizarea pieselor. Acestea specifică și tensiunea de mers în gol a mașinii și programul de schimbare a acesteia.
Procesul tehnologic tipic pentru producerea ansamblurilor sudate constă în următoarele operații:
- fabricarea pieselor;
- pregătirea detaliilor;
- de asamblare;
- sudare;
- operațiuni de finisare;
- protecție anticorozivă;
- de control.
Articole similare
Trimiteți-le prietenilor: