Articolul descrie tehnologia de fabricare a trunchiurilor de arme.
Partea 1. Tehnologia fabricării barilului
Probabil, mulți vor fi de acord. că partea principală a armei este trunchiuri. La urma urmei, ei trag. Eficacitatea focurilor de tunuri a provocat o persoană să facă o mică arma "de mână". Un astfel de tun, la mijlocul secolului trecut, a fost găsit în castelul Tanneberg din Hesse (Germania). A fost distribuită la sfârșitul secolului al XIV-lea. Desigur, era dificil și inconfortabil să-l împușcă din mână, iar curând o cutie de arbalestă se potrivea. Sa dovedit că acuratețea armei și acuratețea noilor arme, în mod serios inferioare celei bune de ceapă, deși este cu mult superioară în ceea ce privește energia și, prin urmare, în forța de penetrare. Sa dovedit repede că, odată cu creșterea lungimii trunchiului, focurile devin mai exacte. Din acest moment începe istoria armei de foc.
Astăzi, pușca noastră de vânătoare "de cotitură" are trei părți principale: trunchiul (sau trunchiurile care formează unitatea cu baril), pantoful, patul.
Etapele de pliere a unui tub dintr-un trunchi simplu. Deasupra - plăcuță-goală pentru portbagaj.
Trunchiul dă direcția la zborul de foc sau de glonț. Cu cât este făcut mai corect și cu mai multă atenție, cu atât este mai bine săritura și cu cât este mai mare precizia.
Blocarea încuietorează buza trunchiurilor, servind ca un element de legătură între trunchiuri și loji și este în arme principalul element inerțial care absoarbe puterea de dăruire. În pantofi, sunt montate mecanisme de blocare, de impact și de siguranță.
Cutia oferă avantajul de a arăta arma la țintă, naturalețea țintirii și înmuierea efectului forței de recul datorată transformării sale parțiale într-un moment de cotitură.
Înainte de a vă spune despre tehnologia actuală de fabricare a butoaielor de arme, aș vrea să îi familiarizez pe cititori cu o parte a istoriei armelor legate de îmbunătățirea fabricării acestei cele mai importante părți a armei. La urma urmei, pentru a produce un trunchi bun este o sarcină dificilă, chiar și cu nivelul actual de dezvoltare a ingineriei. Totuși, perseverența, diligența și ingeniozitatea strămoșilor noștri îndepărtați au găsit diverse soluții la această problemă. Nivelul de calitate al celor mai bune produse ale secolului al XVIII-lea pentru specialiștii de astăzi pare aproape misterios. Vrem să vă spunem cum stăpânul trecutului a creat o armă minunată, a arătat câteva exemple și a crezut împreună despre măreția spiritului lor, sperând că acest lucru ne va întări propriul.
În 1811, Henry Anshutz (dintr-o bine cunoscută dinastie de armură) a publicat o carte despre fabrica de arme din orașul Suhl. El scrie despre patru tipuri de tehnologii pentru producția de butoaie: rădăcini convenționale, răsucite și ranile din Damasc.
Schema de obținere a butoailor răsucite.
Un butoi convențional a fost obținut dintr-o preformă de bandă de 32 centimetri lungime, 4 inci lățime, 3/8 inci grosime. După încălzirea metoda de forjare a fost pliat benzi pe mandrină astfel încât marginile sale longitudinale sunt adiacente unul la celălalt capăt la capăt, paralel cu axa găurii. Această îmbinare a fost sudată printr-o metodă de forjare și a fost forjată cu atenție. Există indicii indiscutabile că ambele părți late ale țaglei rectangulare au fost uneori conduse "în față" și sudate nu în fund și suprapuse. După sudare și răcire Ceca au fost matura tetraedrică, un strung pentru a se pisa o suprafață exterioară care este apoi șlefuită manual pe un mare cerc cu diametrul de gresie moale de 1,75 m. Cu partea pelviană este înșurubat în țeava unui capac cu filet, care este, de asemenea, uneori, se fierbe. Bineînțeles, butoaiele tuturor armetelor de încărcare a mușchilor au fost înecate, indiferent de tehnologia primirii lor.
Tambur rotit. Cusătura sudată într-un trunchi convențional, situată paralel cu axa trunchiului, era adesea locul distrugerii în timpul tragerii. Pentru a evita acest lucru, un simplu butoi sudat a fost reîncălzit în partea centrală și răsucite de-a lungul axei de-a lungul întregii lungimi, astfel încât cusătura de sudură să aibă forma unei linii de șurub. Această tehnică a făcut cusătura mult mai puțin încărcată când a fost concediată.
Trunchiul de rănire a fost obținut prin înfășurarea treptată a benzii de oțel pe un dorn sub formă de tijă sau țeavă. Sudura asemănătoare șurubului a fost forjată succesiv de un ciocan forjat.
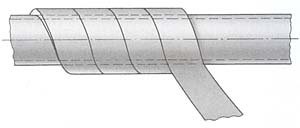
Principiul obținerii trunchiurilor de rănire.
Damasc trunchiuri.
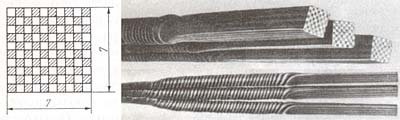
Dezvoltarea rapidă a metalurgiei la sfârșitul secolului al XIX-lea a dus la apariția oțelurilor de carbon cu proprietăți mecanice ridicate. Perspectivele utilizării lor pentru producția de trunchiuri păreau evidente. Cu toate acestea, chiar și în primul trimestru al secolului XX, mulți armuriști din Europa au continuat să producă butoaie în tehnologiile din Damasc. Astăzi este necesar să se înțeleagă că astfel de trunchiuri, deși sunt monumente pentru zelul fantastic al armeștilor din generațiile anterioare, sunt totuși inferioare în toți indicatorii importanți pentru butoaiele moderne aliate. Să reamintim compatrioților noștri că oțelul de 50A și chiar 50RA, din care se fabrică ambele trunchiuri de la Tula și Izhevsk astăzi, nu fac parte din butoaiele aliate. Și mai multe despre trunchiurile damascului. O sută de ani sau mai mult după fabricație, este foarte probabil ca sudarea forjată a elementelor să poată fi distrusă în mod semnificativ, iar rezistența trunchiurilor ar putea să nu fie suficientă pentru a asigura siguranța fotografierelor. Fii foarte atent dacă vrei să tragi dintr-o pistă veche cu trunchiuri damasc.
Introducerea crom oțel carbon, vanadiu, nichel, siliciu, mangan și alte elemente au condus la o creștere semnificativă în cele mai importante proprietăți ale oțelurilor baril - elasticitate, rezistenta la rupere, duritatea suprafeței, rezistența la coroziune. Mai mult, aceste tehnologii fac posibilă obținerea oțelurilor cu proprietăți predefinite. Toate acestea au permis producția de semifabricate omogene pentru butoaie. Acest proces a început în ultima treime a secolului al XIX-lea și a coexistat cu tehnologia "Damasc" timp de aproximativ o jumătate de secol.
Partea 2. Dezvoltarea tehnologiei pentru fabricarea butoaielor de pușcă.
O nouă etapă începe cu respingerea butoaie fabricate din benzi, iar trecerea la trunchiuri, canalul care a format găurire adâncă. Aceasta tehnologie este mult mai productivă, dar a fost nevoie pentru a rezolva o serie de probleme grave, spune-ne despre unde vrem să-l pună în aplicare, cititorilor moderni să-și imagineze ceea ce prețul obținut un pistol, are o luptă remarcabilă. Nou proces de fabricație preforme baril începe cu forjare, care nu numai că dă forma exterioară a piesei baril se apropie de butoi finit, dar oferă, de asemenea structură îmbunătățită de oțel prin reducerea granularitatea acesteia. De obicei, o bucată de oțel rotund cu un diametru de aproximativ 50 mm este tăiată pentru piese forjate. Lungimea acestei piesă depinde de lungimea viitoare a cilindrului. O bucată de lungime de 320 mm este suficientă pentru a extrage dintr-o bucată de lucru de 750 mm lungime, cu un diametru mediu de 30 mm. Desigur, după forjarea diametrului preformei în zona camerei este mult mai mare decât cea a botului. Aici este de remarcat faptul că, cu forjarea convențională, aproximativ 15% din oțel intră în scară. Fierari spun că metalul "arde".
Îndreptarea cilindrului
Pentru a elimina tensiunile interne ale tălpilor forjate, acestea sunt încălzite la (aproximativ) 850-860 grade și ținute timp de aproximativ o jumătate de oră. Parametrii exacți de încălzire depind de gradul de oțel al cilindrului și de grosimea piesei de prelucrat. Sarcina de a elimina solicitările interne este foarte importantă pentru toate etapele producției de butoaie. Este deosebit de important să nu existe nici un stres în tubul tubular finit, conceput pentru a forma blocuri de butoi de două sau mai multe trunchiuri.
Ideea este că lipirea cu aliaje moi și în special solide necesită încălzire considerabilă și asimetrică a trunchiurilor. Răcirea blocului sudat este, de asemenea, neuniformă. Prezența tensiunilor interne duce la o deformare vizibilă a trunchiurilor după lipire. Mai mult decât atât, o încălzire ridicată a suprafeței interioare a butoaielor în timpul fotografiei, în special intensă, poate provoca deformarea ireversibilă a butoiului, în cazul în care există tensiuni în el. După normalizare, se realizează întărirea. Esența sa constă în obținerea proprietăților optime datorită formării structurii fine a metalului.
Orice oțel este un sistem complex de faze care conține cel puțin două modificări ale cristalului de fier pur, carburi de fier, carburi de impurități metalice și soluții solide ale unora dintre aceste componente unul în celălalt. Modificarea temperaturii modifică starea de fază a acestui sistem complex și dimensiunile fazelor individuale, care afectează în mare măsură proprietățile de performanță.
Încălzirea este încălzirea uniformă a piesei la o temperatură care depinde de rețeta oțelului din care este fabricată. Blocurile din oțel Sk 65, care în Germania sunt adesea folosite pentru butoaie, este încălzită la 840 de grade. După aceea, se coboară într-un ulei având temperatura camerei. Apoi, piesa de prelucrat este "eliberată", pentru care este încălzită într-un cuptor de mufe pentru aproximativ 4 ore la o temperatură de 580-600 de grade. Un astfel de tratament termic complex poate afecta în mod semnificativ duritatea, vâscozitatea, elasticitatea și rezistența maximă la tracțiune.
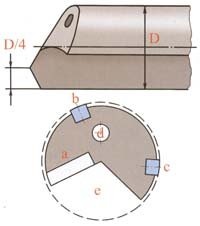
Arme de forare:
a este o inserție de tăiere,
b și c sunt ghidaje,
d - canal pentru alimentarea lichidului de răcire,
cavitatea de eliminare a cipurilor
Tocul tratat termic este îndreptat cu atenție. Acest lucru se face astfel încât, atunci când se găsește, atunci când piesa se rotește, aceasta nu vibrează. Puneți piesa de prelucrat pe orizontală în timp ce rotiți, ajustând forma cu rolele de presiune. După îndreptare, preforma este din nou încălzită pentru a ușura solicitarea internă, apoi este lovită de ambele părți și este cotată.
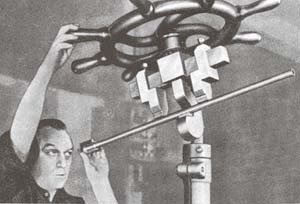
Îndreptarea cilindrului de-a lungul inelelor umbrite folosind o presă cu șurub
După aceasta, ei încep cel mai delicat proces de producție a forajului de trunchi. Adâncime de forare, mai ales într-un țagle lung, cu stabilitate longitudinală scăzută - un cântec special. În domeniul armei, pentru acest lucru sunt utilizate strunguri speciale. În ele, piesa de lucru fixă se rotește, iar burghiul special se mișcă înainte. În acest proces, două probleme majore: găuriți burghiul de pe axul piesei de prelucrat și îndepărtați chipsurile. Prima problemă poate fi rezolvată datorită omogenității structurii piesei de prelucrat și vitezei de avans relativ scăzute a burghiului și vitezei de tăiere pentru a exclude vibrația piesei de prelucrat. Desigur, aceste limitări măresc timpul de forare. Problema îndepărtării cipurilor, care, uneori, nu numai că răsfoiește suprafața canalului, ci și penează burghiul, este rezolvată prin tehnici speciale. În secolul al XIX-lea a folosit „burghie pușcă“, construcția ei au fost aproape de matura, adică, ele se bazează a avut un bar pe toată lungimea de lucru a sectorului cilindric care a fost selectat, cu un unghi de aproximativ 100 de grade. Proiectarea burghiului este destul de simplă și este bine înțeleasă din desen. Prin intermediul unei găuri mici în corpul burghiului, în zona de tăiere se introduce o emulsie de răcire, care îndepărtează așchii formate de-a lungul unei caneluri paralele cu axa burghiului. Astfel de mașini au devenit mult timp multi-ax și destul de automatizate. Acest lucru permite unui lucrător să controleze forajul pe mai multe mașini. Acest proces încă nu garanta un grad înalt de curățenie a tratamentului de suprafață al găurii de butoi. Asamblarea lemnului a fost adesea principalul motiv pentru aceasta. În plus, performanța de foraj nu a fost ridicată.
În 1937 Burgsmueller a schimbat calitativ schema de foraj. El a propus un aranjament vertical al pieselor de prelucrat și o direcție de găurire de la partea de jos spre partea de sus pentru o mai bună îndepărtare a cipurilor. Ca bază a burghiului, el a folosit o țeavă, pe capul de lucru al căruia au fost atașate trei plăcuțe de ghidare și sudate o tăiere. Procesul de tăiere are loc atunci când se răcește cu aer comprimat, care este alimentat în spațiul dintre suprafața burghiului și pereții găurii formate. Rândurile nu au intrat în contact cu pereții orificiului și au fost duse jos cu aerul. Cuplul de rezistență semnificativ mai mare al cuplului posedat de "conductă", comparativ cu bara profilate, permite, pe lângă obținerea unor suprafețe bune, să utilizeze viteze mai mari de tăiere și avansare la găurire.
În 1942, Baysner a îmbunătățit această metodă. El a întors poziția orizontală la mașina de găurit, a sugerat utilizarea uleiului ca agent de răcire și a perfecționat capul de foraj. Uleiul a fost alimentat sub presiune în spațiul dintre burghiu și suprafața cilindrică rezultată și a transportat rumegușul prin canalul central într-un colector special. Suprafața era foarte netedă, într-o oarecare măsură datorită lustruire de către ghizi. Totuși, după găurire, gaura cuțitului este prelucrată de o maturare.
Înainte de a începe să lucrați pe suprafața exterioară a cilindrului, acesta este îndreptat: verificați corectitudinea axei canalului și, dacă este necesar, îndreptați-l cu o presă cu șurub. Verificarea corectitudinii canalului este efectuată de inele de umbră, pe care fiecare vânător îl poate face. Dar procesul de editare necesită nu numai o viziune bună, ci și un mare sentiment de metal, care vine doar cu experiență. Faptul este că trunchiul are elasticitate. Prin urmare, dacă sub sarcină sa îndreptat, atunci după îndepărtarea sa va reveni parțial la starea inițială. Un maestru experimentat simte cât de mult trebuie să se "îndoaie" trunchiul, astfel încât, după înlăturarea încărcăturii, acesta să devină ireproșabil corect.
După formarea trunchiului de baril, apare o altă sarcină dificilă: să întoarcem trunchiul din exterior. În acest caz, principala dificultate este că centrul suprafeței exterioare coincide exact cu centrul găurii de butoi. Dacă acest lucru nu se face, receptorul va fi un tub diferențial. Mai mult decât atât, datorită valorii mari a raportului dintre lungimea baril la diametrul cilindrului în timpul suprafeței de cotitură este necesar să se stabilească două lunete, fiecare dintre acestea trebuie să fie pre-prelucrate gât. Pentru executarea corectă a acestei operații, la mijlocul lungimii trunchiului, este instalat un manșon special, care permite menținerea corectă a trunchiului pentru suprafața netratată cu canelura de gâturi pentru lunetă. Când gâturile sunt străpuns, ambreiajul poate fi îndepărtat și șlefuirea exterioară a trunchiului poate fi efectuată pe copiator. Aceste tratamente de strung poate duce la o anumită deformare a trunchiului. Prin urmare, trunchiul este din nou controlat de inele de umbră și, dacă este necesar, este îndreptat. Recoltarea și măcinarea se efectuează după ce gâturile pentru lunetă sunt măcinate individual. Etapa finală a producției de butoaie este o măcinare fină, numită honuire în industria de arme.
Progrese semnificative în fabricarea butoaielor de pușcă este forjarea lor pe un dorn. Desigur, echipamentul pentru acest proces nu este ieftin. Prin urmare, formarea butoaielor prin forjare este rentabilă doar pentru volume mari de producție. Cu toate acestea, economisirea banilor și a timpului este, de asemenea, semnificativă. În producția de butoaie prin metoda de forjare rotativă la cald, se folosesc piese cu lungimea de 260-280 mm și cu diametrul de 35 mm. În acesta, un burghiu Bisner face o gaură cu un diametru de 20,5 mm. Piesa este fixată pe un dorn întărit cu atenție, care are forma suprafeței interioare a cilindrului finit. După încălzirea prin inducție electrică a țaglei la temperatura dorită, aceasta este alimentată în zona de forjare, unde se rotește de-a lungul axei sale, sub impactul ciocanelor în formă de cruce. Timp de o jumătate de minut, piesa de preluare ia forma externă și internă a cilindrului cu camera. Încălcarea după astfel de forjare nu se efectuează. Forma exterioară a trunchiului se face prin strunjire și măcinare. Canalul cilindrului este desenat cu o mătură. Prelucrarea finală a orificiului tubului, incluzând închiderea camerei și a botului, se efectuează după asamblarea unității cilindrului.
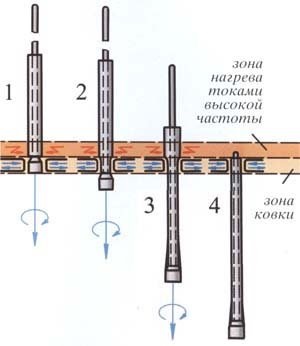
Schema de forjare rotativă:
1 - încălzirea cu curenți de înaltă frecvență,
2 - începerea forjării,
3 - proces de forjare,
4 - finisare forjare
O metodă și mai progresivă de a face butoaie este forjarea la rece a unui dorn. Unul dintre avantajele sale este că economisește aproximativ 15% din oțelul cilindric scump, lăsând în scară pentru forjarea la cald. Suplimentar, suprafața interioară a cilindrului este obținută printr-o copie exactă a dornului, astfel încât este posibil să se obțină butoaie complet pregătite (cu o cameră, o constricție a botului și o tăietură). Suprafața canalului de cerneală necesită numai lustruire. În plus, structura cilindrului cu miez rece îi conferă proprietăți mecanice ridicate. Adevărat, forjarea la rece necesită ciocane mai puternice și o durată mai lungă. Durata durează doar trei minute. Forma exterioară se termină prin șlefuire și lustruire. Verificarea corectitudinii axei canalului se efectuează și după această tehnologie și, dacă este necesar, este îndreptată. Etapa finală de producere a biletelor de butoaie individuale este fotografierea și branding-ul.
Articole similare
-
Proiect creativ privind tehnologia pe tema fabricării jucăriilor moi - îngeri pazitori
-
Productie de pungi de polietilena echipamente, tehnologie, materii prime, productie video
Trimiteți-le prietenilor: