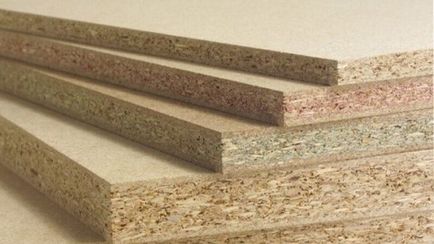
Astăzi se poate spune că EAF pentru ultima perioadă de timp a devenit cel mai comun și celebru material din lemn. Un astfel de material este considerat principalul material de construcție utilizat pentru producția de mobilier. Recent, panourile de particule au devenit în cerere atât în industria construcțiilor, cât și în producția de clădiri cu creștere joasă.
Tehnologie si echipamente pentru productia de PAL
Ca materie primă principală pentru producerea de deșeuri din industria fabricilor de cherestea este utilizată. Deșeurile de deșeuri pentru producerea de PAL sunt tăiate la așchii pe mașini de decupat special. Din chipsuri, așchii de rumeguș, așchii de așchii și așchii sunt fabricate pe mașini rotative speciale. În ceea ce privește cherestea rotundă, așchii sunt făcuți din bușteni pe mașini speciale care au arbori cuțite. Înainte ca jurnalul să fie introdus în moara de cipuri, acesta este tăiat în semne de măsurare, lungimea căruia este de un metru. Aceleași cipuri pentru producerea de plăci aglomerate trebuie să aibă anumite dimensiuni, și anume, lățimea trebuie să fie între unu și zece milimetri, de lungime de la cinci până la patruzeci de milimetri și o grosime de 0,2 până la 0,5 milimetri. Cipurile de dimensiuni mai mici sunt îndreptate spre stratul exterior al plăcii de particule. În plus față de respectarea dimensiunilor, este de asemenea necesar să se asigure că are o formă plană care trebuie să se potrivească cu o suprafață plană și o grosime uniformă. Pentru straturile externe de așchii după mașinile cu PAL, trebuie să se efectueze o măcinare suplimentară pe ciocane speciale. Sau mergeți în mori, unde trebuie să schimbați grosimea.
Producția de PAL în ultima operație are o importanță deosebită pentru producția de plăci laminate. În acest proces sunt impuse cele mai înalte cerințe, atât la suprafață, cât și la calitate. Rândurile brute finisate sunt depozitate în siguranță în recipiente speciale. Un transportor mecanic și un sistem de transport pneumatic sunt alimentate în aceste buncăre. După aceea, este trimis la uscător, în cazul în care este necesar să se usuce la umiditate de patru sau șase la sută. În ceea ce privește stratul exterior al EAF, ar trebui să fie între două și patru procente. În ceea ce privește producția de PAL cu straturi diferite, se efectuează o uscare separată pentru fiecare strat. În producție se folosesc numai uscătoare convective în conformitate cu regulile, dar cel mai adesea acestea sunt trimise la echipamentul de cilindri.
În uscător, este posibilă incinerarea atât a combustibilului, cât și a gazului, deoarece temperatura în astfel de echipamente este de 1000 de grade Celsius. La intrarea în tambur, temperatura agentului de uscare ar trebui să fie de 550 de grade Celsius, iar la ieșirea la 120 de grade Celsius. Tamburul are o lungime de zece metri, iar diametrul este de 2,2 metri.
După ce a fost complet uscat, acesta este sortat pe agregate mecanice speciale sau mașini pneumatice. Fabricarea de PAL pe astfel de mașini se realizează rapid, fiabil și calitativ. Pe astfel de mașini, așchii sunt împărțiți în anumite fracții, atât pentru straturile interioare, cât și pentru cele exterioare. În acest stadiu, producția de chipsuri de PAL se apropie de final, iar acum se poate observa că acest proces tehnologic poate determina cea mai bună performanță a următoarelor operațiuni, și anume, pentru a produce PAL.
Cipul pentru producția de plăci aglomerate trebuie să fie amestecat cu lianți într-o unitate specială, numită mixer. O astfel de operațiune este considerată a fi cea mai dificilă, deoarece tehnologia de producție va necesita procesul de acoperire a fiecărui rumeguș. Dacă chips-uri pentru PAL nu sunt osmolennye, ele nu pot fi lipite, în timp ce va exista o rășină suplimentară, care va duce la depășiri de costuri și slabă calitate a plăcilor viitoare. În ceea ce privește lianții, ele sunt furnizate sub formă de soluție, deoarece concentrația lor în stratul exterior este de 55%, iar în stratul interior este de 61%. Astăzi, mixerul cel mai obișnuit care utilizează lianții pulverizați este considerat o torță care direcționează un flux de chips-uri suspendate pentru a produce EAF în aer.
Datorită acestui flux, în timpul procesului de amestecare, lianții se așează pe suprafața cipului. Amestecurile trebuie să fie controlate fin și trebuie respectate cantități stricte între rășină, întăritor și așchii. După ce așchii de plăci aglomerate au fost măcinate cu o racletă sau bandă transportoare, acestea sunt trimise la mașina de formare. În cazul în care o astfel de mașină ar trebui să toarne în mod egal ștanțele pe tava de trecere sau pe transportor. Simplul concept al unui covor este ca o bandă continuă, care ar trebui să determine grosimea și lățimea. Covorul va fi împărțit în pachete, din care se formează ulterior plăcile în timpul presării la cald.
Aici este necesar să se țină seama de faptul că o umplere covor uniformă va afecta calitatea plăcii PAL, și anume grosimea și densitatea. În plus, mașinile de formare trebuie în mod necesar să toarne așchiile mici în stratul exterior.
Citiți de asemenea
Articole similare
-
Cum se face hidroizolarea fundației - dispozitiv și calcul, tehnologie de restaurare, hidroizolare
-
Sudarea acoperișului cu propriile mâini video, editare, echipament, tehnologie de depozitare
Trimiteți-le prietenilor: