Punctul de topire al cuprului este 1080-1083 ° C. În intervalul de temperatură 300-500 ° C, cuprul are o fragilitate la cald. Cuprul în stare lichidă dizolvă gazele - oxigen și hidrogen, ceea ce face dificil sudarea. Cu oxigenul, cuprul formează oxid de cupru (Cu2O), care dă cuprului un aliaj intermediar Cu + Cu2O situat de-a lungul granițelor granulelor. Deoarece punctul de topire al aliajului intermediar este cu 20 ° mai mic decât punctul de topire al cuprului pur, el promovează formarea fisurilor fierbinți în timpul cristalizării sudurii.
Atunci când cuprul topit care conține oxid de cupru se solidifică, se formează fisuri mici în prezența hidrogenului. Acest fenomen, numit „boala de hidrogen din cupru“, se produce datorită compusului hidrogen cu oxigen și formarea oxidului cupros de vapori de apă, care la temperaturi ridicate tinde să se extindă, provocând fisuri în metalul de sudură. Dificultatea se datorează sudarea cuprului și conductivitatea termică ridicată (de 6-7 ori mai mare decât conductivitatea termică a oțelului) și fluiditatea în stare topită.
Mai puțin oxigenul sub formă de oxid cupros este conținut în cupru, cu atât mai bine poate fi sudat. Impuritățile arsenicului, plumbului, antimonului și bismutului fac ca sudarea cuprului să fie dificilă. Cel mai bun sudabilitate este posedat de cupru electrolitic, conținând nu mai mult de 0,4% impurități. Cuprul de cupru, conținând până la 1% impurități, este sudat mai rău. Cromul, manganul, fierul, nichelul și tantalul măresc rezistența metalului de sudură la sudarea cuprului.
Arc sudare. Având în vedere conductivitatea termică considerabilă a cuprului, sudarea prin arc necesită utilizarea unui curent mărit.
Fluxul de fluid al cuprului este mai mare decât oțelul, astfel încât marginile foilor sudate trebuie să fie îmbinate strâns, fără goluri. Unghiul de deschidere a muchiilor trebuie să fie de 90 °. Uneori marginile sunt oarecum deranjate, îngroșându-le pentru forjarea ulterioară și pentru lucrul la rece pentru a sparge granulele metalice ale îmbinării sudate. Cuprul cu o grosime mai mare de 6 mm este sudat cu preîncălzire. Foi de grosime de la 1 la 3 mm sunt sudate cu flanșe de margini, fără metal de umplere.
Foile subțiri (mai puțin de 6 mm) după sudare sunt forjate în stare rece și groasă la o temperatură de 200-300 ° C. Metalul sudurii și zona de tranziție sunt supuse forjării. Pentru a da vâscozitatea metalului de sudură și plasticitatea după forjare trebuie să fie recoace, încălzită la o temperatură de 550-600 ° C și răcită rapid în apă. În acest caz, metalul de sudură și zona de sudură dobândesc o structură cu granulație fină. Pentru a preveni fisurile, forjarea nu trebuie efectuată la temperaturi de peste 300 ° C, deoarece cuprul la această temperatură devine fragil. Sudarea este realizată cu un electrod de carbon sau metal folosind fluxuri și acoperiri.
Modurile de sudare a cuprului cu un electrod de carbon sunt după cum urmează:
Sudarea cu un electrod de carbon conduce un arc lung (10-15 mm) la un curent direct de polaritate directă la o tensiune de 40-55 V.
Pentru a evita formarea oxidului de cupru, sudarea trebuie efectuată rapid, fără opriri și întreruperi, la o viteză de cel puțin 0,25 m / min. Capătul tijei de umplere trebuie să se afle între capătul electrodului și baia topită a metalului de bază, fără a se imersa în el. Electrodul este ținut la un unghi de 70-80 °, iar tija de umplere - la un unghi de până la 30 ° față de foaia sudată.
Sârma de topire ar trebui să cadă în bazinul de sudură. Ca metal de umplutură, se utilizează un fir fabricat din cupru pur (electrolitic) sau bronz fosforos. 009-0,3, constând din cupru 90,2%, staniu 9,27%, fosfor 0,25%. Pentru protejarea metalului de oxidare și îndepărtarea oxidului cupros se utilizează următoarele fluxuri:
La sudarea cu br. 009-0,3, un amestec de 94-96% borax, 6-4% metal de magneziu în pulbere poate fi utilizat ca flux.
La sudarea cuprului cu un electrod metalic, utilizați electrozi de cupru din fire Ml, M2 și M3 sau bronz Br. CMC-3-1 cu straturi a căror compoziție ca reductori introduse feromangan, ferosiliciu, siliciu și al cuprului. Pentru a proteja cusătura laterală inversă de oxidare în canelura sub cusătura suport turnat flux de aceeași compoziție ca acoperire. Acoperirea aplicată flux MMP-2, având următoarea compoziție: 43% simanala (aliaj de siliciu, mangan și aluminiu) 30% fluorină și 14% feldspat, 8% din grafit, 5% carbonat de potasiu, 45% de silicat de sodiu la greutatea uscată amestec. Grosimea stratului de acoperire pe o parte este de 0,35-0,8 mm. Curentul este constant, polaritatea inversă este de 50-60 A la 1 mm din diametrul firului. Arcul ar trebui să fie cât mai scurt posibil. Sudarea este rapidă. Cu o grosime de metal de până la 4 mm, nu este făcută muchia conică. Pentru o grosime mai mare de 4 mm, unghiul de înclinare este de 30-35 °. grosimi de metal mai mari de 4 mm sunt sudate cu preincalzire la 200-300 ° C, după căldura de sudură este folosit pentru 550-600 ° C și răcirea rapidă în apă. Pentru etanșare, cusătura este prefabricată conform indicațiilor de mai sus.
Cupru cu conținut de oxigen nu este mai mare de 0,01%, este posibil să se sudeze electrozi Ml filmate „Komsomoletz“ următoarea compoziție de cupru: 50% feromangan, ferosiliciu 8%, 10% fluorină și 12% din feldspat, sticlă de apă de 20% (până la greutate partea uscată a stratului de acoperire). Modurile de sudare ale electrozilor Komsomolets-100 sunt următoarele:
De asemenea, electrozii folosiți ET, dezvoltați de către uzina baltică din Leningrad, cu un nucleu de Br din bronz de siliciu-bronz. CMC-3-1, conținând 3% siliciu, 1% mangan, iar acoperirea constând din 17,5% din minereu de mangan, iar 13% fluorină și 16% din grafit cu argint, 32% ferosiliciu 75% concentrație, 2,5% aluminiu în pulbere. Acoperirea este amestecată pe un sticlă lichidă și aplicată pe un strat de 0,2-0,3 mm pe o tijă de 4-6 mm în diametru. Sudarea este efectuată printr-un arc scurt pe un curent direct cu polaritate inversă; curentul este selectat din calcularea a 50 a pe 1 mm din diametrul tijei electrodului.
Cuprul este, de asemenea, sudat cu un electrod tungsten într-un mediu de protecție de azot.
Sudare cu gaz. Cuprul cu o grosime de până la 10 mm este sudat cu o flacără de 150 dm 3 / h de acetilenă la o grosime de metal de 1 mm.
La sudarea foi mai groase de alimentare cu flacără a fost crescută la 200 dm 3 / h acetilenă la 1 mm, în acest caz, este mai bine să se aplice simultan sudarea a două arzătoare, fiecare cu o capacitate de 100 dm3 / h acetilenă la 1 mm grosime de foaie. Flacăra trebuie să fie doar reductivă; apariția în flacără a unui exces de oxigen conduce la oxidarea cuprului. Cu un exces de acetilenă în amestec este restaurat oxid cupros cu hidrogen și monoxid de carbon conținut în flacără, prin care în metalul de sudură având pori și fisuri. Miezul flacării trebuie ținut la un unghi de 90 ° față de suprafața foilor, la o distanță de 3-6 mm de suprafața băii. Sudarea este rapidă, fără întreruperi. Sunt aplicate cusături cu un singur strat, deoarece sudarea în mai multe straturi poate cauza fisuri. Cusăturile lungi sunt sudate în secțiuni, într-o manieră inversă. La sudarea dispozitivului, mișcarea liberă a marginilor trebuie asigurată sub influența deformărilor termice. În mod avantajos, îmbinările cap la cap și colțuri sunt aplicate pe cusătura exterioară, evitând suprapunerea și sudarea prin presare. Grosimea de metal de 2 mm sudate cap la cap, fără aditivi, prin plasarea azbestul inferior sau grafit pentru a preveni scurgerea metalului sudat: la o grosime de 3 mm, folosite în formă de V conice margini cu un unghi de deschidere de 90 ° și tocire de cel puțin 1,5-2 mm (1 / 5 foi grosime); la grosime de peste 10 mm. Formarea în formă de X și sudarea sunt efectuate simultan din două părți într-o poziție verticală cu două arzătoare. Înainte de a suda conductele, pentru a evita tranzițiile bruște, pre-extrageți țevile sau aprindeți țevile.
Înainte de sudare, marginile sunt curățate cu o luciu metalic sau gravate într-o soluție de acid azotic, urmată de spălarea în apă.
Distribuția căldurii flacării este reglată astfel încât firul să se topească mai devreme, iar metalul topit acoperă muchiile aduse în stare de "încețoșare".
Tija de umplere trebuie să fie un fir de cupru sau cupru pur (electrolitic) care conține până la 0,2% fosfor și până la 0,15-0,30% siliciu, care sunt deoxidanți. Diametrul firului este egal cu:
Nu se utilizează fire cu diametrul mai mare de 8 mm. Pentru a deoxida cuprul în timpul sudării și îndepărtarea oxizilor din zgură, utilizați fluxurile indicate mai sus. Fluxul nr. 4 cu fosfat acid de sodiu este utilizat pentru sudarea cu sârmă care nu conține deoxidanți - siliciu, fosfor etc.
Sudarea cuprului poate fi efectuată și cu ajutorul fluxului gazos BM-1 (vezi § 2). În acest caz, vârful arzătorului este utilizat cu un număr mai mare decât la sudarea cu o pulbere de flux, astfel încât să nu se reducă viteza de încălzire și sudare.
Ca rezultat, calitatea sudării este mai mare decât la sudarea cu fluxuri pulverulente.
Dacă metalul îmbinării sudate necesită o rezistență sporită și o ductilitate, cusătura sudată este forjată: cu o grosime de până la 6 mm în frig și mai sus în starea încălzită la 500-600 ° C. Îngroșarea existentă a cusăturii înainte de forjare este tăiată pentru a evita formarea fisurilor în timpul forjării. În timpul forjării, măcinarea boabelor și distrugerea peliculelor de oxid de cupru la limitele granulelor apar, ceea ce crește rezistența și plasticitatea metalului de sudură. Pentru a crește vâscozitatea îmbinării sudate, metalul de sudură și zona de sudură sunt tratate termic prin încălzire la 550-600 ° C, urmată de răcirea rapidă în apă.
Pentru sudarea cu gaz, lipirea și sudarea cuprului și a aliajelor sale (alama, bronz, etc.) pot fi dezvoltate pentru a aplica VNIIAvtogenom metodă de sudură gazoflyusovoy, în care un flux sub formă de pulbere este aspirat și acetilenă este alimentat direct în flacăra arzătorului prin intermediul unei instalații speciale KGF-2-66. Instalarea de KGF-2-66 este disponibil comercial și constă dintr-un arzător de sudură, uscător (pentru sudarea acetilenă de la generator) și flyusopitatelya un lucru și un flux rezervor de rezervă. Rezervorul este proiectat pentru 4,6 kg de flux, viteza fluxului de 70 g / g 3. 50-2800 Acetilena dm curgere 3 / h, la o presiune acetilena - nu mai mică de 0,1 kgf / cm2 de presiune de oxigen în timpul sudurii este 3,5-4 , 5 kgf / cm 2. Unitatea cântărește 40 kg.
Ca rezultat al sudării cu gaz a cuprului, sudură și îmbinare au următoarele proprietăți mecanice:
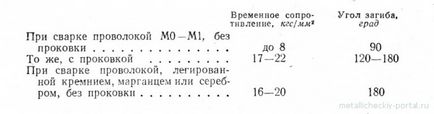
Articole similare
-
Tehnologia de sudare a cuprului și a aliajelor sale, sudură și sudor
-
Sudarea cuprului și a aliajelor sale - sudarea diferitelor metale
Trimiteți-le prietenilor: