În cele mai moderne uzura echipamentelor supuse unor suprafețe de frecare piese de îmbinare (de exemplu, dinții angrenajului, ghidaje și slide-uri, arbori de motoare de col uterin, suprafața interioară a cilindrului motoarelor cu combustie internă și altele asemenea. D.), astfel încât suprafețele de contact de frecare ale pieselor trebuie să fie mai rezistente decât întreaga parte, la acțiunea de temperaturi ridicate, frecare, coroziune etc.
Există diverse moduri de întărire a suprafeței pieselor, creșterea rezistenței lor la coroziune și reducerea frecării suprafețelor de frecare. Acestea includ: .. tratament Superficial termic, dopare, care îndeplinesc cerințele necesare, acoperiri galvanice de suprafața suprafeței de acoperire a piesei anticorozivă a piesei de aliaje de sudură etc. O metodă de piese de aliere de suprafață sau elemente este alierea electricã, care este însoțită de diverse transformări fizice și chimice stratul de piesă prelucrată. Aceasta îmbunătățește rezistența la uzură și duritate, rezistență la căldură, rezistența la coroziune a suprafețelor pieselor și pentru a reduce coeficientul de frecare, precum și pentru a repara și de a restabili dimensiunile pieselor rupte, dându-i un nou strat de proprietăți de suprafață.
Esența procesului de dopare cu electrospark constă în transferarea materialului EI care îndeplinește anumite cerințe la suprafața piesei de prelucrat a piesei cu descărcare electrică prin scânteie. Această metodă asigură o aderență puternică a materialului de aliere la suprafața piesei; este simplu de implementat.
În cazul dopajului prin electrospark, legile și procesele descrise în Ch. I, dar ca mediu de lucru se utilizează aer sau o atmosferă neoxidantă (argon, heliu, hidrogen). Particulele de anod topite scoase în spațiul interelectrode nu sunt efectuate de mediul de lucru, ci se precipită pe suprafața catodului. Ca orice alt proces tehnologic, aliajul cu electrospark are propriile caracteristici, care sunt studiate cu atenție. Procesul de dopaj cu electrospark poate fi reprezentat în următoarea formă.
Dacă electrozii, unul dintre care legiruemaya piesă (catod), iar celălalt - metal aliere (anodul) pentru a aplica un impuls de tensiune și pentru a reduce electrozii până evacuarea scânteie între anod și catod de curgere al curentului de impulsuri de înaltă densitate. În consecință, în punctul de descărcare a scântei de pe suprafața electrozilor (în principal la anod), metalul este încălzit și parțial evaporat. Picăturile de metal topit de la anodul se îndreaptă spre suprafața catodului sub influența unui câmp electromagnetic. După terminarea impulsului curent, mișcarea nu se oprește și picăturile de metal ajung pe suprafața catodului. La atingerea suprafeței catodului, particulele de anod topit sunt introduse în gaura topită pe suprafața catodului și se amestecă cu catod metalic și parțial depus pe marginea găurii și sudate la acesta. Dacă mutăm anodul de-a lungul unei linii, obținem o serie de găuri cu o compoziție modificată a metalului, adică cu un nou aliaj și o structură. Pentru a obține o suprafață întărită relativ netedă, anodul trebuie mutat în raport cu catodul în timpul întreruperii între impulsuri, care are o durată egală. 0,01 c, nu mai mult de 1/4 din diametrul puțului. În acest caz, amestecarea necesară și întrepătrunderii metalului topit ambii electrozi una față de alta și de a îmbunătăți calitatea suprafeței prelucrate.
În plus față de amestecarea pur mecanică a particulelor de metal topit ale ambelor electrozi sub influența temperaturilor ridicate și a presiunii care se dezvoltă în canalul de descărcare, apar procesele de difuzie în straturile superficiale ale electrozilor. Procesul de dopaj are loc într-un mediu gazos, astfel încât particulele topite pe calea lor interacționează cu acest mediu și formează un strat de armare care diferă în proprietățile fizico-chimice de proprietățile aliajelor și aliajelor metalice.
O proprietate foarte valoroasă a dopajului cu electrospark este că asigură o legătură foarte puternică între stratul întărit și metalul aliat. Studiile au intarit piese sub sarcini alternante și temperaturile arată că stratul intarit nu se exfoliază, chiar și în cazul carburii de materiale de acoperire (de exemplu, carbură de tungsten sau carbură de cimentate). Acest lucru se explică prin faptul că între stratul întărit și metalul aliat există o legătură de difuzie. Prin difuzie se înțelege amestecarea sau penetrarea unei substanțe în alta datorită mișcării termice a moleculelor substanțelor ce urmează a fi contactate.
Ca material de aliere, sunt utilizați diferiți compuși de carbură și borură de metale refractare, care sunt obținuți, de regulă, prin metoda cermetului. Compușii de carbură și borură au activitate chimică scăzută și, prin urmare, atunci când sunt aplicați, nu impun cerințe ridicate asupra mediului de lucru. Acestea formează o acoperire bună, dar cu o calitate relativ scăzută a suprafeței și, prin urmare, părțile care lucrează la frecare trebuie măcinate. Părțile dopate cu carburi și boruri au o rezistență mare la uzură și duritate.
Pentru aliere mai puțin frecvent utilizate: tungsten, molibden, reniu și crom. Dacă este necesar, elementele de pe elementul sau elementele aplica strat antifricțiune care reduce coeficientul de frecare a suprafețelor care crește durabilitatea și fiabilitatea pieselor utilizate pentru doparea staniu, plumb, bismut, indiu, grafit. Aceste materiale sunt ușor oxidate și, prin urmare, dopajul se efectuează în gaze neutre.
Rezistența la coroziune a componentei poate fi mărită făcând dopat cu grafit, siliciu, aluminiu sau ferocrom.
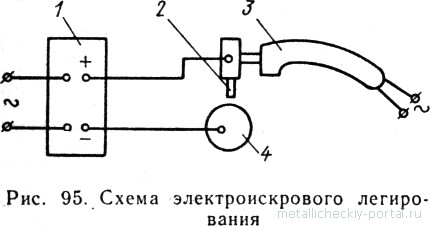
Echipamente pentru aliere prin electrospark. În Fig. 95 prezintă schema instalației pentru aliere electrică prin scânteie electrică; acesta include: un generator de impulsuri 1, un vibrator electromagnetic 3, un electrod dopant 2 și un electrod dopat 4.
Pentru o punere în aplicare stabilă a procesului de dopaj este necesar un contact periodic cu o anumită frecvență a electrodului dopat 2 cu un component electrod dopat 4. Acest contact este asigurat de vibratorul electromagnetic 3 (există și alte modele de vibratoare). Cele mai bune rezultate sunt obținute experimental în intervalul frecvențelor de contact de la 100 la 400 Hz. Creșterea frecvenței în acest interval vă permite să măriți performanța procesului. O creștere suplimentară a frecvenței accentuează semnificativ calitatea suprafeței.
Contactarea electrodul cu legiruemym Alierea metalic (piesa) se realizează prin aceea că electrodul de dopaj este fixat pe armătura electromagnet sau cap rotativ (în acest ultim caz, o multitudine de electrozi fixate la cap, dar la unghiuri diferite).
În Fig. 96 prezintă cel mai simplu design al organului de lucru cu un electromagnet. Electrodul de dopaj 1 este fixat la suportul electrodului 2, la care tensiunea de proces a impulsului de la generator este alimentată de către firul 5. Sursa de oscilație este un electromagnet 4. Pentru a excita electrod oscilații instalate pe acestea de inserție triunghiular armătură feromagnetică 11, iar electrodul de la un capăt al său este suspendat liber pe puntea 10. Forța de tragere a electromagnetului este șurub reglabil 3. Puterea este furnizată sârma electromagnet 6 de la o sursă de alimentare specială. Întregul sistem este suspendat cu ajutorul brațului 7 de mânerul 9 și este închis de carcasa 8.
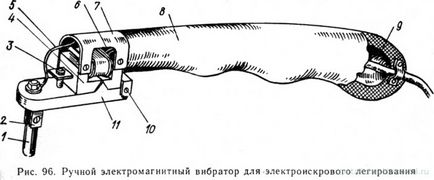
Principiul acțiunii organului de lucru cu un electromagnet (există și alte denumiri: excitator sau vibrator) se bazează pe atracția periodică a corpurilor feromagnetice plasate într-un câmp magnetic alternativ. Sub acțiunea unui curent alternativ, a condus la un electromagnet, o inserție fermoagnetică a armăturii începe să-l atragă. Când tensiunea scade (sinusoidul trece prin valoarea zero), suportul electrodului revine la poziția sa inițială sub acțiunea arcului. Electrodul va oscila la dublul frecvenței rețelei, adică cu o frecvență de 100 Hz. Dacă este necesară obținerea unei frecvențe mai mari de 100 Hz, atunci sunt utilizate surse de alimentare speciale.
Contactarea periodică a electrodului de aliere cu componenta poate fi obținută prin rotirea capetelor multi-electrod. Au fost elaborate diverse modele de capete multi-electrod pentru electrozi elastici și de aliere rigidă (în ultimul caz, electrodul este fixat pe corp cu un element elastic flexibil).
Capul rotativ multi-electrod este alcătuit dintr-un suport multi-electrod, perii de transport cu curent, o cuplă elastică; Un motor electric este utilizat pentru a roti suportul multi-electrod, dar pot fi utilizate și turbine pneumatice. Toate elementele sunt montate într-o carcasă din plastic, care se conectează la mâner. Întregul element de lucru este închis cu un capac de protecție. Procesul de dopaj cu un cap rotativ multi-electrod este oarecum diferit față de cel care lucrează cu un electrod vibrat. Când se produce contact tangențial cu piesa „patare“ a metalului topit aliere pe suprafața piesei de prelucrat, astfel reducând rugozitatea suprafeței de dopaj. Trebuie remarcat faptul că, cu ajutorul unui cap rotativ multi-electrod, este ușor de mecanizat procesul de aliere. În prezent, au fost deja dezvoltate facilități mecanizate de aliere.
Generatoare de impulsuri pentru aliere prin electrospark. Pentru procesul de aliere prin electrospark, au fost proiectate și fabricate generatoare speciale de semiconductoare de impulsuri unipolare, dar și alte tipuri de generatoare (de exemplu, generatoare de relaxare) sunt utilizate și în întreprinderi.
Instalația experimentală a Institutului de Fizică Aplicată al Academiei de Științe a SSR Moldovenească este produsă în serii mici de instalații de aliere, ale căror principale caracteristici tehnice sunt prezentate în tabelul nr. 18.
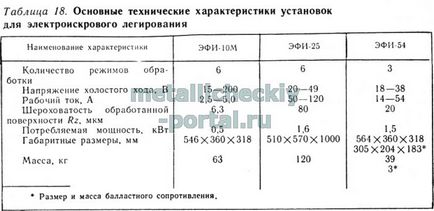
Modelul desktop EFI-54 este echipat cu două vibratoare electromagnetice de mână (mari și mici) și un cap rotativ multi-electrod pentru execuția manuală. Unitatea este destinată depozitării metalelor prețioase pe suprafața pieselor de echipament electric pentru a îmbunătăți proprietățile lor de comutare.
Unitatea EFI-25 are un vibrator electromagnetic de mână; Se utilizează pentru alierea unor părți mari de mașini, precum și pentru refacerea dimensiunilor pieselor uzate.
Instalarea EFI-10M este realizată în versiunea desktop și este echipată cu un vibrator electromagnetic de mână. Se utilizează pentru alierea și refacerea dimensiunilor pieselor uzate ale mașinii.
Tehnologia de aliere prin electrospark. Caracteristici tehnologice scânteie procesul de aliere, ca în EEE, depind în mare măsură de regimurile de tratament electric selectat, t. E. Cantitatea de energie eliberată în distanța dintre electrozi și a frecvenței de repetiție a impulsurilor. Intensitatea procesului scânteii aliere, adică. E. Cantitatea de material care urmează să fie transferată pe suprafața care trebuie tratată pe unitatea de timp, aceasta depinde de combinația dintre un material de electrod și materialul aliere și legiruemogo.
Temperatura încălzirii electrozilor are o mare influență asupra procesului de dopaj, prin urmare, se utilizează moduri de prelucrare abrupte cu energie înaltă în puls când masa părții este mai mare de 0,5 kg.
Ca impuls de intrare de energie electrică este alierea împărțit în mod condiționat finisaj și dur. Dacă este necesar pentru a obține suprafețe de înaltă calitate și filmul depus este mic, tratamentul se efectuează în operația de finisare. Moduri rugoase cu energie ridicată de impulsuri este utilizat când rugozitate permisibil semnificative de suprafață și materialul legiruemy nu este predispus la fisurare, iar reactivitatea materialului aliere este mic.
Selectarea regimului de dopaj pentru diferite combinații de materiale realizate în mod empiric, în funcție de cerințele fizico-chimice pentru suprafața tratată, ei rugozitatea suprafeței, porozitatea și grosimea stratului aplicat. Stabilitatea procedeului de dopaj manual depinde în mare măsură de calificarea operatorului, deoarece modul stabilit poate fi ușor distorsionat prin selectarea incorectă a presiunii electrodului de aliere pe partea respectivă. Pentru a asigura stabilitatea procesului de dopaj, este necesar să se monitorizeze mărimea curentului de funcționare și să se mențină presiunea electrodului de aliere în limitele specificate. Odată cu creșterea energiei pulsului (funcționare curentă) crește grosimea stratului depus crește adâncimea efectului termic și calitatea suprafeței deteriorată a aliajului par prizhogi este rupt și continuitatea acoperirii.
Grosimea stratului aplicat cu un strat electrospark este mică și diferită pentru diferite combinații de materiale dopate și aliate și pentru diferite regimuri de acoperire. Acesta variază de la câteva micrometri într-un mod curat la 1-2 mm - pe dur.
Uniformitatea stratului de acoperire depinde de uniformitatea deplasării electrodului de aliere de-a lungul suprafeței aliate a piesei de prelucrat și de stabilitatea procesului de dopaj.
Sub continuitatea (densitatea) stratului se înțelege absența în stratul întărit al cochililor și al diferitelor microvasse. Se diminuează cu o acoperire neuniformă, când pe suprafață există filme de oxid și o rugozitate semnificativă a suprafeței întărite. Rugozitatea de suprafață a suprafeței dopate nu trebuie să depășească Rz = 6,3 μm. Atunci când aliajul este dopat, se asigură o continuitate ridicată a stratului de acoperire și, pe măsură ce crește energia impulsurilor, scade și crește numărul de cochilii.
Suprafețele după dopaj au aceeași structură ca și în EEE. Rugozitatea suprafeței depinde de energia impulsurilor și de rezistența la eroziune a materialului dopat și aliat. Cu cât rezistența la eroziune a materialelor este mai mare și cu atât energia impulsurilor este mai mică, cu atât este mai bună calitatea suprafeței tratate. Grosimea minimă a suprafeței întărite este în Rz = 2,5-4 μm.
Pentru alierii scânteie, pentru a conferi elementelor de suprafață ale unei părți sau a proprietăților fizico-chimice detalii întregi de suprafață dorite, folosind diferite formulări de aliaje dure, de exemplu, VC-2, VC-3, T15K6, T30K4, diborura de titan, carburile de crom, titan și niobiu, aliaje de CB și SNGM; si metale - tungsten, crom, molibden, cadmiu, beriliu, argint, aur, și altele.
Alegerea regimului de dopaj necesar se efectuează atunci când eșantioanele sunt prelucrate cu materialul de aliere selectat. Probele au fost cântărite înainte și dopaj la intervale scurte (una - trei minute) pentru a produce procesul de dopaj repetate de cântărire pentru a determina creșterea în greutate și grosimea stratului de dopare și timpul de dopaj necesar. Calitatea suprafeței de aliere și continuitatea acesteia sunt controlate vizual cu o lupă de o creștere de șase ori.
În cazul în care partea care este supus doparea părți dintr-un aliaj omogen, se recomandă să se construiască un tabel sau un grafic de creștere în greutate în straturi de aliere specifice, în funcție de timpul de dopaj pentru diferite moduri și timpul de procesare optimă în fiecare mod. Practic, calitatea aliajului este garantată de respectarea exactă a regimului dopajului electric și a timpului de dopaj.
Anterior, o listă de materiale utilizate în aliere. Cu toate acestea, în practică, să se ocupe de această combinație legiruemogo și material de dopaj, care în anumite condiții, să ofere calitatea de acoperire necesară, dar foarte multe ori materialul alierea nu este depus. În funcție de condițiile specifice de dopaj, se folosesc diferite metode tehnologice pentru a asigura rezultatele finale necesare. De exemplu, atunci când se aliază cu tungsten, anodul și catodul sunt adesea sudate, rezultând o suprafață neuniformă și accidentală. Eliminați sudarea poate fi pre-dopată cu carbon în fiecare centimetru pătrat al suprafeței timp de 1 minut (pentru instalarea EFI-10M).
Este necesar să se aplice un strat de tranziție atunci când materialul anod selectat nu este depus pe metalul dopat. De exemplu, prin doparea aliaje de aluminiu carbură de wolfram aplicat primul strat de nichel și apoi un strat de nichel - carbură de tungsten. Atunci când se aliază, nu se recomandă să se efectueze mai multe treceri de-a lungul aceluiași loc, deoarece după ce ajunge la o anumită grosime a stratului de aliere, câștigul de greutate scade și depunerea începe. În moduri diferite, numărul de treceri maxime variază între patru și șase.
În timpul aliajului, este necesar să se monitorizeze temperatura încălzirii anodice și să se prevină supraîncălzirea acesteia.
Articole similare
-
Câți nu vă doare înainte de operațiunea pda - littleone 2018-2018
-
Cum de a fixa un urechile fără o operațiune în mai multe moduri
Trimiteți-le prietenilor: