mori cu ciocane (MM) în industria materialelor utilizate pentru polizarea brută construirea și uscarea materialului cu rezistență la compresiune mai mică de 150 MPa și umiditate nu mai mult de 24% simultan - cretă, gips, argilă, azbest, carbon, etc ...
Măcinare este realizată în MM prin ciocniri de bucăți de material zdrobit sau bate ciocane sunt suspendate pivotabil pe Highspeed (80-50 m / s) a rotorului, datorită impactului bucăți de garnituri de coliziune reciproc.
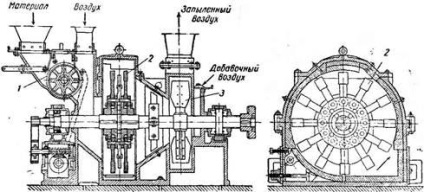
Fig. 2. Moară de ciocan (concasor) cu îndepărtarea pneumatică a materialului zdrobit:
1-alimentator; 2-mill; 3-ventilator.
În funcție de direcția de livrare a materialului și a agentului de uscare, MM sunt împărțite în tangențial și radial (Figura 3.45). În morile tangențiale, materialul care trebuie zdrobit și agentul de uscare sunt alimentate de-a lungul axei tangențial circumferenței rotorului - tangențial (Figura 3.45, a).
În materialul radial MM și agentul de uscare sunt alimentate de-a lungul rotorului (Figura 3.45, b) - radial.
Procesul de măcinare în MM se efectuează după cum urmează. Atunci când unitatea este pornită, ciocanii articulați 4 (Figura 3.45) sub acțiunea forței centrifuge ocupă poziția prezentată în Fig. 3,45 la 7 bucăți estru zdrobit 20-40 mm material de dimensiuni sunt alimentate împreună cu un agent de uscare în camera de lucru a morii, unde cad sub impactul ciocane 4. Piesele cad în împrăștiind porțiuni care lovesc căptușeala și una față de alta, și zbura din nou greva ciocane. Mai mult, materialul de măcinat intră în spațiul dintre grătarul 6 și capetele ciocanelor 4, unde materialul este zdrobit prin abraziune intensă. Materialul măcinat este descărcat în pasajul 8 ciocane și particule mici sunt trimise la un separator (tranziție sau inerțială), materialul sub formă de particule mari care se încadrează pe rotor rotativ și apoi, împreună cu materia primă ciclul se repetă. În același timp, materialul de măcinare este uscat simultan cu măcinarea cu aer încălzit la o temperatură de 300-450 ° C.
Finețea materialului este reglată prin cantitatea ciocanelor, viteza rotorului, diferența între grătarul și capetele ciocanelor, iar diferența dintre ciocane și aripi.
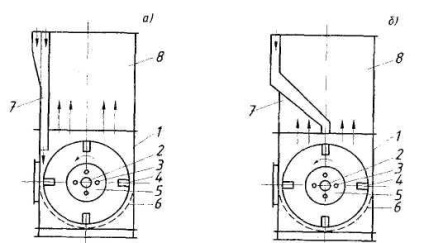
Fig. 3.45. Schemele de freze cu ciocane:
a) tangențială; b) radial; 1 - locuințe; 2 - arbore rotor; 3 - degete balamale; 4 - ciocane; 5 - discuri; b - grătar; 7 -techka; 8 - coș de fum.
Eficiența MM este caracterizată prin trei indicatori principali - productivitatea Q, puterea consumată de N, finețea procesului de măcinare R.
Consumul specific de energie 3 = N / Q pentru frezare reflectă economia procesului de măcinare și eficiența acestuia. Dependența lui N
f (Q) la R = const se numește caracteristica de lucru a morii, de-a lungul căreia intervalul de lucru MM este determinat când diferitele materiale sunt zdrobite la o anumită dimensiune (Figura 3.46).
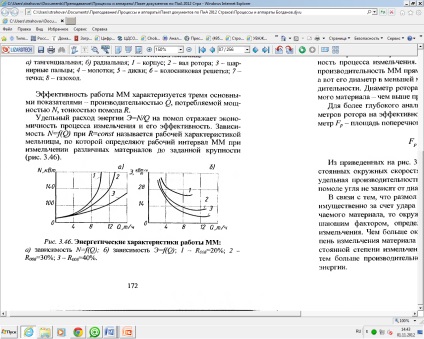
Fig. 3.46. Caracteristicile energetice ale MM:
a) dependența N = f (Q); b) dependența E = f (Q); 1 - R008 = 20%; 2 - R008 = 30%; 3 - R008 = 40%.
Din graficul prezentat în Fig. 3.46, rezultă că, pe măsură ce crește finețea măcinării, productivitatea morii scade, iar consumul de energie al mecanismului crește; cu o creștere a productivității la orice finețe de măcinare, consumul specific de energie este redus; Cu o creștere a finețe a măcinării la o ieșire constantă, consumul specific de energie crește.
Eficiența procesului de măcinare în MM este influențată în mod semnificativ de parametrii rotorului: diametrul și lungimea acestuia. Odată cu creșterea diametrului rotorului la o frecvență constantă de rotație, viteza circumferențială a bătăilor (ciocanelor) se schimbă, ca urmare a creșterii forței centrifuge și, de regulă, a eficienței procesului de măcinare. În prezent, se crede că performanța MM este direct proporțională cu lungimea rotorului, dar diametrul său afectează modificarea performanței într-o măsură mai mică. Diametrul rotorului depinde de rezistența materialului care trebuie zdrobit - cu cât rezistența este mai mare, cu atât este mai mare diametrul.
Datorită faptului că măcinarea materialului în MW se datorează în principal lovind pin (ciocan) în bucăți de material concasat, viteza rotorului periferic este un factor decisiv determina intensitatea procesului de măcinare. Cu cât viteza circumferențială este mai mare, cu atât este mai mare gradul de măcinare a materialului pe ciclu de curse unitar; la un nivel constant de măcinare, cu cât este mai mare viteza circumferențială, cu atât este mai mare productivitatea și cu atât mai puțin consumul specific de energie.
Numărul de ciocane pe rotor afectează de asemenea performanța MM. Se constată că productivitatea MM depinde de numărul de bătăi din serie de-a lungul circumferinței rotorului la o putere de 0,25. Pentru a estima influența numărului de bătăi, este setat parametrul mm = z / x, unde z este numărul total de bătăi pe rotor; x - numărul de rânduri bate de-a lungul lungimii rotorului, buc.
În timpul funcționării diferitelor dimensiuni ale MM, a fost găsit un număr rațional într-un rând, acesta fiind: un minim de 6, un maxim de 12.
Consumul specific de energie pentru măcinarea aceluiași material în morile tangențiale este cu 12-15% mai mic decât în cazul laminoarelor radiale. Acest lucru se datorează condițiilor mai bune de ventilare ale camerei de lucru. Prin urmare, atunci când alegeți tipul de morărit, este necesar să acordați prioritate MM tangențială.
Procesul de măcinare este cel mai eficient dacă batetul are muchii ascuțite. Mai mult decât atât, acest efect se manifestă într-o măsură mai mare la goluri mari, mai mult de 20 mm.
La morile disponibile în comerț este instalat un spațiu de 25-30 mm. Acest lucru se datorează necesității de a preveni accidentele cauzate de pătrunderea materialului neconstruit (metal) în camera de lucru.
Acest proces de măcinare în MM este considerat a fi rațional, în care materia primă și agentul termic sunt alimentate tangențial, iar grăsimile din separator se întorc radial pe rotor pe rotor.
Ventilarea, adică cantitatea de aer tras prin camera de lucru a morii, viteza ei are o mare influență asupra finețea măcinării materialului, a consumului specific de energie și a productivității MM. Ca caracteristica de ventilație a MM, viteza amestecului de aer se referă la secțiunea transversală a rotorului morii
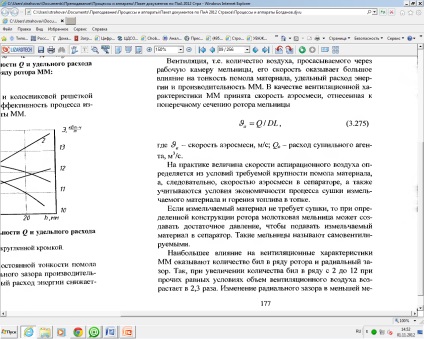
unde Viteza amestecului de aer, m / s; Qβ - consumul agentului de uscare, m 3 / s.
Cea mai mare influență asupra caracteristicilor de ventilație a MM este asigurată de numărul de bătăi din rândul rotorului și de clearance-ul radial. Astfel, cu o creștere a numărului de bătăi din seria de la 2 la 12, cu alte lucruri egale, volumul aerului de ventilație crește cu un factor de 2,3. Variația clearance-ului radial are un efect mai redus asupra volumului aerului de ventilație. Astfel, de exemplu, creșterea clearance-ului radial de 2 ori de la 4 la 8 mm mărește volumul aerului de ventilație cu 25%.
În plus, presiunea de aer dezvoltată de moară este influențată în mod semnificativ de schema de poziționare pe rotor, de unghiul de înclinare și de decalajul dintre ele. Toate celelalte lucruri fiind egale, aspectul a fost eșalonat, reducând presiunea la 25%. Reducerea decalajului dintre grinzile din rânduri și pereții de capăt ai camerei de lucru mărește caracteristicile de ventilație ale MM. Astfel, de exemplu, cu reducerea totală a decalajelor în rândul între perlele de la 35 la 15 mm, presiunea aerului dezvoltată de rotor crește cu 25%.
Schimbarea bătăii de la 20 ° (înclinată de-a lungul rotirii rotorului) la -20 ° (înclinată înapoi) reduce capul dezvoltat cu 22%.
Creșterea vitezei circumferențiale a rotorului la 15% duce la o anumită creștere a consumului de energie al unității, dar măcinarea în MM este mult mai eficientă, iar produsul finit are o compoziție mai uniformă a cerealelor.
Mărimea materialului inițial are un impact semnificativ nu numai asupra parametrilor tehnologici și energetici ai MM, ci și asupra fiabilității operaționale a pieselor de lucru ale morii.
Articole similare
Trimiteți-le prietenilor: