Echipament de producere de OSB (OSB):
Domeniul de dezvoltare și fabricare a sistemelor de presare pentru fabricarea materialelor din plăci pe bază de lemn, în condiții moderne, necesită o abordare integrată în multe domenii - tehnologie, chimie și fizică. Linile de presă moderne sunt întreprinderi de înaltă tehnologie echipate cu echipamente inovatoare. Este suficient să spunem că linia ContiRoll (metoda de presare continuă) pentru producția plăcilor OSB (OSB). costă 60-70 de milioane de euro, fără instalare, punere în funcțiune și pornire. În lume există două firme care au devenit sinonime cu presa hidraulică în fabricarea lemnului. plăci. Acestea sunt companiile germane Siempelkamp și Dieffenbacher. Presa acestor două companii a echipat marea majoritate a uzinelor mari pentru producția de OSB. atât în Europa cât și în America de Nord.
Principalele etape ale procesului de producție
Diagrama pe un exemplu de linie de firmă "Dieffenbacher":
I. sortarea si sortarea bustenilor
Primul lucru care trebuie livrat la uzină este materia primă din lemn - lemn rotund. Aspen, plop, pin, artar sunt cele mai populare rase pe care le cumpara producatorii OSB. Odată ce materiile prime au ajuns la locul unde se află instalația, aceasta este descărcată imediat cu ajutorul camioanelor, un manipulator hidraulic special conceput sau o macara cu prindere.
II. Se taie busteni pe un transportor cu lanț
O parte din lemn este pus pe bursa de materii prime, unele sunt imediat puse în producție. Mai mult, volumul necesar de materii prime pentru o anumită perioadă de timp este scufundat în bazinele de aburire, după care se frământă. Dacă lemnul este recent recoltat și dezghețat, atunci este imediat permis să se debaraseze și să se extindă în continuare pe PAL.
III. Cut-urile tăiate tăiate în bușteni scurți sunt încărcate într-o mașină de ras, care le împarte în așchii de panglică în direcția fibrei de lemn
Dimensiunea chipului este stabilită în conformitate cu procesul de procesare. Roletele au o grosime uniformă. Cele mai multe plante utilizează un amestec de așchii de dimensiuni de la 75 la 150 mm în lungime și 15-25 mm în lățime. Dar grosimea medie a chipului a scăzut de la 0,8 mm, care a fost făcută în anii 80, până la 0,6 mm astăzi. Restul chipsurilor mici și coaja servesc drept combustibil pentru sistemul energetic al instalației.
IV. Uscarea și sortarea jetoanelor obținute
Chipsurile brute după ce au fost scoase la gunoi sunt depozitate în recipiente speciale, din care sunt alimentate în porții în tamburul instalației de uscare. Conceptul de uscare a transportoarelor OSB-sluzhki a fost împrumutat din industria alimentară - tehnologia de producere a chipsurilor de cartofi. Fluxul de cip se usucă uniform și temperatura la ieșirea din uscător este scăzută. Aceasta este o circumstanță foarte importantă, deoarece cu cât este mai scăzută temperatura la ieșirea uscătorului, cu atât este mai mare siguranța la incendiu a procesului și cu atât sunt mai mici emisiile de poluanți (compuși organici volatili). După uscare, chipsurile sunt sortate pentru a separa rumegulele prea fine și prea mari din fluxul principal.
Tesăturile sortate sunt amestecate cu ceară și liant impermeabil (de obicei liant polimeric fenolic sau izocianat)
Aceste impermeabile și rezistente la influența lianților de apă fierbinte asigură rezistența internă, rigiditatea și rezistența la umiditate a panoului. Mixerul este un tambur cilindric care se rotește la o viteză predeterminată. În interiorul tamburului, parafina, rășina și alte componente de adeziv sunt alimentate prin conducte separate. Dar, indiferent de ce parafină este folosită, brută sau emulsificată, se injectează înaintea rășinii. Pentru straturile interioare și exterioare sunt utilizate cel mai adesea diferite tipuri de rășini - stratul exterior poate fi furnizat sub formă lichidă sau pulbere, în timp ce rășina stratului interior poate fi, de asemenea, fenol formaldehidă sau izocianat. Este interesant faptul că discul rotativ care distribuie rășina în interiorul mixerului a fost împrumutat de la echipamentul pentru vopsirea autoturismelor și a devenit o descoperire revoluționară în tehnologia resurfacerii cipurilor.
VI. Modelarea și stivuirea
Stația de formare are greutăți încorporate, magneți, role de prindere, precum și un sistem de tăiere cu două fețe a marginilor covorului, cu returnarea materialului excesiv de cip în coșul cu strat intermediar. Capul de orientare al bărbieritului stratului exterior este ceva foarte asemănător cu grapa de fermă. Este alcătuită dintr-o serie de discuri circulare care direcționează tărâțele care se încadrează, aliniindu-l paralel cu partea lungă a covorului. Capul de așezare orientat al stratului interior constă din role în formă de stea cu lame plate. În rotație, se aliniază tamburul paralel cu lățimea covorului, perpendicular pe direcția de deplasare a transportorului. Chipsurile din stratul de suprafață al plăcii sunt de obicei așezate de-a lungul părții lungi a panoului (pentru a conferi o rezistență la încovoiere și rigiditate mai mare pe direcția longitudinală). Două sau trei straturi interioare sunt așezate de obicei peste stratul de suprafață. Pentru a prinde incluziunile străine este un detector de metale cu role. Presarea prealabilă a covorului în producția plăcilor OSB nu este necesară. Pentru tăierea incluziunilor și a cipurilor inutilizabile, este prevăzut un buncăr special.
VII. presare
Presarea apare la temperaturi și presiuni foarte ridicate până când se formează un panou de construcție solid, dens. Sarcina presei este de a compacta covorul din PAL și de a ridica temperatura în interiorul acestuia la o valoare predeterminată. Temperatura de întărire a rășinii este cuprinsă între 170-200 ° C. Lățimea presei de bandă din oțel - 3 m, grosime - 3 mm. Benzile de oțel sunt încălzite de un cazan cu o capacitate de 8 MW cu ajutorul unui ulei termic la o temperatură de 220 ° C. În zona de compactizare din față, presiunea de presare atinge 5 N / mm2. Timpul de întărire calculat este de 9 secunde pe milimetru de grosime a plăcii. Presiunea și temperatura trebuie măsurate în decurs de 3-5 minute. Praful și aburul uzat după presare sunt îndepărtate de ventilator într-o manieră umedă.
VIII. Defecțiuni finale (finale)
După apăsare, lama fără sfârșit a plăcii se deplasează de-a lungul mesei cu role, unde se efectuează o verificare a corespondenței geometrice și a tăierii marginilor longitudinale. Pentru tăierea transversală a plăcilor de pe plăcile de lungime dorită, se utilizează un fierăstrău diagonal asociat. Răcirea plăcii are loc pe răcitoarele ventilatorului. La capătul liniei de producție folosind verificarea instrumentație grosimea corespunzătoare și greutatea dalelor și prezența în ele a fasciculelor sau alte defecte. După presare, plăcile sunt păstrate timp îndelungat în depozit pentru a permite adezivului să se întărească și să se întărească complet. În mod tipic, timpul de menținere final este de la 12 la 48 de ore.
Plăcile de format mare sunt stivuite și reîncărcate folosind un stivuitor. Pentru tăierea plăcilor într-un format standard, se utilizează un ferăstrău circular de înaltă performanță. Plăcile formate sunt introduse în mașina de frezat, unde marginile lor sunt profilate. Mulți producători din America de Nord protejează marginile plăcilor OSB de umiditate. În acest scop, înainte de ambalarea stiva de plăci, pe suprafețele sale laterale se pulverizează o vopsea puțin penetrantă, care înfundă porii și compactează capetele plăcilor.
Produsele finite sunt transferate pe linia de ambalare
Dezvoltarea tehnologiei pentru producerea plăcilor OSB. O descriere detaliată a tehnologiei standard, care este cea mai răspândită în America de Nord în producția de OSB. pe.
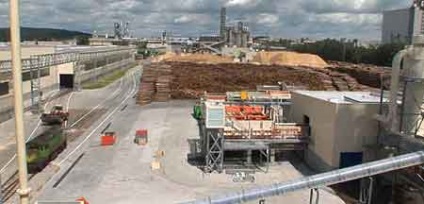
Chipsurile brute după ce au fost scoase la gunoi sunt depozitate în recipiente speciale, din care sunt alimentate în porții în tamburul instalației de uscare. Conceptul de uscare a transportoarelor.
Articole similare
Trimiteți-le prietenilor: