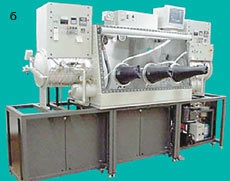
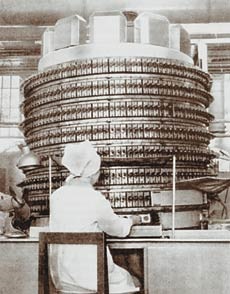
Principalul factor pe care inginerii trebuiau să îl ia în considerare erau condițiile speciale în care funcționează lampa: acestea sunt temperaturi ridicate și vid.
După selectarea materialelor, detaliile acestora trebuie să fie astfel formate. De multe ori, aceleași metode de prelucrare au fost utilizate pentru acest lucru ca și în alte ramuri ale construcției de mașini și a instrumentelor. Adevărat, încercat, de exemplu, fără lustruire mecanică - după ce în stratul de suprafață există mulți contaminanți. Ca o alternativă, am folosit lustruirea chimică sau electrochimică, precum și șlefuirea. Mai devreme decât oriunde, în producția de tuburi radio, metode electrofizice de prelucrare dimensională au găsit aplicații: electroeroziune și ultrasonică.
Marea majoritate a pieselor metalice lămpi obținute prin deformare plastică. - Flexibil (efectuarea, grătare, sunt înfășurate ca spirale pe traversei), stantare (fragmente anozii), etc. Ca rezultat al structurii materialului modificat - a apărut solicitări mecanice care, ulterior, ar putea denatura forma și dimensiunile pieselor. Reducerea stresului și refacerea structurii metalului ajută la recoacere - menținerea temperaturii înalte și răcirea lentă.
Ce este comun între radio și sticla de șampanie?
Atunci când se deschide o sticlă de șampanie sau apă spumante, se formează bule de gaz: în timp ce presiunea scade, solubilitatea gazelor din lichid scade. La fel se întâmplă și cu încălzirea. În metale, din care sunt fabricate tuburi radio, se dizolvă și gaze, iar pentru a menține un vid bun în lampa finită, piesele sunt recoace.
Atmosfera din cuptorul de recoacere trebuie să fie foarte curată, numai în acest caz impuritățile să părăsească suprafața, în loc să o satureze. La prima vedere, se pare că ar fi optime să se răcească părți și blancuri într-un vid. Dar obținerea unui vid înalt într-un cuptor mare, umplute cu detalii murdare (prin electronica electronică), nu este ușor și scump. În locul unui vid pentru recoacere, atmosfera de hidrogen, care în același timp a restaurat filmele de oxid, a fost foarte potrivită. Adevărat, hidrogenul penetrează în unele metale. Dar, de regulă, nu au acordat atenție acestui lucru: atunci când procesează lampa deja colectată, hidrogenul a părăsit relativ ușor părțile și a fost pompat cu pompe. Nu puteți arde metalele în hidrogen care absorb în mod activ hidrogenul, de exemplu titanul, ele devin fragile. Astfel de detalii au fost recoace în argon și, uneori, în amestecuri de gaze inerte și de reducere.
În timpul recoacerii, azotul, carbonul și oxigenul au fost îndepărtate din metale. Apa si dioxidul de carbon format pe suprafata - atomii de hidrogen si carbon care difuzeaza din adancimea metalului interactioneaza cu oxizii. Carbonul conținut în piesele de oțel nu a reacționat cu hidrogen la aceste temperaturi și au fost recoace în "hidrogen umed" - un amestec de hidrogen și vapori de apă. Din sticlă și ceramică, vaporii de apă și dioxidul de carbon sunt, de asemenea, eliberați în timpul recoacerii, dar se dizolvă în această formă în dielectrici.
Temperatura, durata procesului, compoziția gazului, viteza debitului, cantitatea, materialul, localizarea produselor încărcate - toate influențează rezultatul, de multe ori într-un mod imprevizibil. Uneori, în timpul recoacerii, contaminările au fost transferate de la o parte la alta; În ciuda presiunii excesive în cuptor, gazele au pătruns din atmosferă; Lămpile, colectate din părțile atent curățate, s-au dovedit a fi mai rele decât cele unde părțile erau mai murdare. Aceste și alte zeci de puzzle-uri, încercări reușite și nereușite de a le rezolva au fost munca zilnică a tehnologilor.
Cu timpul, misterul lămpilor de căsătorie cu detalii prea bine curățate ar putea fi descoperit. Sa dovedit că, cu o curățare deosebit de temeinică, suprafața pieselor devine activă din punct de vedere chimic și este imediat oxidat atunci când este extrasă din cuptor. Pentru produsele relativ murdare, pe suprafață există deja o peliculă de oxid care îi protejează de contaminarea ulterioară.
FĂRĂ ACOPERIRI NU SUNT NECESARE
Un alt aspect extrem de important în producerea tuburilor radio a fost aplicarea acoperirilor. Pe mobilier, acoperirile sunt aplicate frumos, pe părțile mașinii - pentru a le proteja de coroziune, pentru a crește durabilitatea, pentru a îmbunătăți aspectul. Adică părțile și fără acoperiri nu își pierd eficiența. În tuburile electronice, acoperirile, de regulă, au efectuat exact funcția de lucru. Astfel, oxidul de calciu mărește emisivitatea catodului. Aceleași proprietăți sunt posedate de oxizi ai altor metale alcalino-pământoase, în special bariu și toriu. În acest sens, proiectarea catodurilor sa schimbat: un fir de încălzire a fost plasat în interiorul unui cilindru metalic îngust, cu un strat emițător aplicat pe suprafața sa exterioară, acoperit, la rândul său, cu un film izolator.
Becurile cu catozi încălzite s-au dovedit a fi de multe ori mai eficiente și durabile. Prin urmare, în tehnologia tuburilor electronice, uneori era mai logic să nu vorbim despre acoperirea pe părți, ci despre detalii care există doar ca bază pentru acoperire. De exemplu, pe ecranele tuburilor catodice, fosforii au fost aplicați (și acum au fost aplicați) - fără ei nu veți obține o imagine vizibilă.
Aplicate și, în general, de neînțeles la procese. De exemplu, izolatoarele de mica de lămpi au fost acoperite cu particule de oxid de magneziu și oxid de aluminiu pentru a face suprafața dur. Izolator pe izolator, mai mult pentru a da o rugozitate? Lucru este că, datorită pieselor metalice la temperaturi înalte lămpi se evaporă parțial, și nu poate împiedica particulele metalice să fie depuse pe izolatori, creând un film continuu - se poate produce un scurtcircuit. Și așa vor cădea doar pe marginile suprafeței izolatoare, iar depresiunile vor rămâne curate.
În general, există foarte multe metode de acoperire. De exemplu, pentru a ochiurilor de plasă nu emit electroni (datorită încălzirii termice a catodului adiacente sau secundar), ele strat metalic aplicat galvanică având o funcție înaltă de lucru - aur, argint, titan, aliaje de staniu-nichel, și altele.
Totuși, în tehnologia dispozitivelor electrovacuate pentru formarea acoperirilor pe părți, se aplică adesea un strat de pulbere și apoi este sinterizat. Particulele pulberii și substratului se coalizează unul cu celălalt datorită difuziei reciproce. Gradul de sinterizare este de obicei scăzut, iar stratul de acoperire este poros. Porozitatea nu interferează cu funcționarea lămpii și, uneori, chiar utilă. Structură similară cu un burete, o acoperire poroasă are o suprafață foarte mare, prin care, de exemplu, crește capacitatea getter de emisie cu catod sau capacitatea de absorbție - substanță specială plasată în becul și adsorbante gazele rămase după pompare.
SUDURA SAU ÎNCĂRCARE?
Piesele finite - catozi cu un strat de emisie, înfășurate pe încălzitoare cu ochiuri jug cu un strat izolator, ștanțate dintr-o foaie sau anozi din cupru solide, izolatori din mică sau ceramică preforme flacoane și concluzii - a fost plasat în cutii speciale, numit un desicator cu atmosfera deshidratată și fără praf , și a fost posibilă începerea asamblării.
În lămpi, piesele sunt imobile (nu trebuie să se miște, altfel toți parametrii "plutesc"), astfel încât au fost conectați prin sudare, lipire și aterizări staționare. Adevărat, la început unele lămpi puternice au fost făcute pliate, și au lucrat cu o constantă pompare din pompe de vid (dar acest lucru nu a durat foarte mult timp).
Principala problemă a tehnologilor a fost aceea că au avut de suferit și lipit cele mai diverse materiale: metale cu metale, sticlă cu metal, ceramică cu metal. În plus, în timpul funcționării, elementele de lampă sunt încălzite și dacă materialele care urmează să fie îmbinate au coeficienți diferiți de dilatare termică, în articulație pot apărea tensiuni mecanice, ceea ce duce la distrugerea lor. Componentele metalice ale lămpilor de joasă tensiune au fost conectate de obicei prin sudare electrică prin contact cu puncte; în producerea lămpilor cu putere mare, s-a folosit sudarea cu arc cu argon, ceea ce a conferit o cusătura etanșă la vid și, prin urmare, a permis sudarea detaliilor cochiliei.
La sudare, materialele celor două părți sudate se topesc. Dacă unul dintre materiale rămâne solid, acest proces se numește lipire reflow. Acesta este modul în care becul de sticlă al lămpii a fost conectat la bornele metalice, iar sticla sa topit. Apropo, pentru concluzii, a fost inventat un aliaj special de fier cu nichel (28%) și cobalt (18%). Se numește covar și are un coeficient de dilatare termică aproape de sticlă. Pentru a evita solicitările termice la joncțiunea cablurilor cu electrozii de lampă, care sunt realizați din materiale cu coeficienți foarte diferiți de dilatare termică, firele subțiri și flexibile intermediare au jucat rolul amortizoarelor.
Când lipire ceramică și metal, în contrast, se topește metalul, și este adesea folosit așa-numita „lipire activă“, între părțile din ceramică și metal pavare folie de titan, atunci acest set este comprimat și încălzit. Datorită difuziei, a apărut o zonă de tranziție și materialele au fost bine conectate. În fine, ceramica de metal (cu toate acestea, sticla la sticla) pot fi conectate prin lipire, dar lipiri metal și „glazura“ - o sticlă specială cu punct de topire scăzut.
Și ce trucuri a trebuit să treacă pentru a conecta, de exemplu, un safir cu sticlă sau cuarț cu sticlă! Cuarțul se extinde cu o creștere a temperaturii cu un ordin de mărime mai mică decât sticla, iar tehnologii trebuiau să dezvolte o serie de aproximativ zece pahare cu un coeficient de creștere a temperaturii în scădere treptată. Procesul de lipire a fost următorul: primul sticlă a fost sudată pe cuarț, apoi a fost turnat al doilea pahar pe el și așa mai departe pe sticla obișnuită: a fost obținut un tort de puf.
Noi spunem atât de multe detalii despre tehnologia pentru a face clar cât de multe probleme, uneori cele mai neașteptate, există inginerii și modul în care, uneori, cu grație face cu ei mintea umană.
LUCRAREA LEMNULUI TRAINATĂ MAI MULT
Dar aici lampa este colectată, este timpul să pompeze aerul din ea și, în același timp, să curățați și să degazați în cele din urmă piesele. În acest scop, fără oprirea pompării, s-au aplicat tensiuni de lucru la electrozi. Cu ajutorul unei astfel de tehnici, numită antrenament, a fost posibilă rezolvarea simultană a mai multor probleme.
În primul rând, activarea catodul sa produs: emisiv practic pur acoperire mai ușor de aplicat la un carbonați de metal și au activat încălzire în oxizi, eliberarea dioxidului de carbon îndepărtat cu o pompă de vid.
În al doilea rând, particule mici de praf ar putea rămâne pe electrozii. Câmpul electric le-a rupt de pe locurile lor și le-a dus la un electrod mai încărcat. După ce s-au dispersat în câmp, ei, ca meteoriții, au lovit suprafața și s-au evaporat.
În cele din urmă, pe suprafața anodului, care nu este niciodată absolut plată, au existat proeminențe ascuțite. Puterea câmpului era maximă, iar punctul a fost supus unei bombardări intense de către electroni. Metalul din aceste locuri a fost încălzit până la temperatura de evaporare, proeminențele au fost automat eliminate și vaporii de metal au fost evacuați. (În acest caz, în lampa finit, pentru s-ar produce anumite defalcare electrică.) În cele din urmă pe peretele cilindrului pulverizat un strat subțire de getter metal și poate doar unsolder tub de sticlă (tub de evacuare) care conectează lampa la sistemul extractor. După aceea, baza a fost fixată pe balon și lipită la capetele picioarelor.
În cele din urmă, lămpile etichetate sunt ambalate în cutii de carton - și la fabrica de radio. Și acolo, în care numai dispozitivele pe care nu se încadrează: în aparatele de radio de uz casnic pentru a difuza emițătoare, de radio portabile, de televiziune, de automatizare, și mai târziu - în primele calculatoare. La începutul secolului al XX-lea a produs dispozitive electronice zeci de milioane pe an, iar viitorul parea luminos. Cu toate acestea, în laboratoarele fizice, sa născut deja un "gravidigger" de tuburi radio. Ei au devenit stabilite în 1947 de oamenii de știință americani William Shockley și John. Bardin tranzistor semiconductoare. Noul dispozitiv are aceeași funcție ca trioda cu vid electric, dar a fost foarte mic, durabil și rentabil, deoarece nu are nevoie de energie pentru încălzirea catodului.
Articole similare
Trimiteți-le prietenilor: