Relația dintre presiune și temperatura de sudare pentru fierul tehnic pur
În Fig. 1 prezintă un grafic care caracterizează condițiile necesare pentru sudarea fierului tehnic pur. Axa verticală reprezintă presiunea de compresie, iar axa orizontală indică temperatura de încălzire. La presiuni și temperaturi în regiunea de sub curba ABHG, sudarea cu fier nu are loc sau este de foarte slabă calitate. Sudura calitativă a fierului poate fi efectuată numai la presiuni și temperaturi situate deasupra curbei ABVG.
Punctul T corespunde punctului de topire al fierului. În partea dreaptă a acestui punct, fierul este sudat în stare topită fără presiune, spre stânga - atunci când este încălzit într-o stare plastică, dar cu aplicarea unei presiuni corespunzătoare, care va fi cu atât mai mare cu cât temperatura de încălzire este mai mică.
Într-o stare neîncălzită (rece), sunt sudate doar metale foarte ductile, de exemplu aluminiul, și în condițiile aplicării unor presiuni specifice de compresie foarte mari.
O îmbinare sudată este numită o îmbinare permanentă a pieselor metalice obținute prin sudare.
O cusătură sudată este partea din îmbinarea sudată care este formată de îmbinarea sudată în timpul procesului de sudare și apoi de metalul solidificat.
Metalul principal este metalul, din care sunt fabricate piesele sudate. Arcul electric sau flacăra lanternei topesc simultan un electrod metalic sau o tijă de umplere în același timp cu metalul de bază, formând un metal lichid care umple cusătura. Metalul bara de umplere sau electrodul, amestecat cu porțiunea topită a metalului de bază, formează metalul de sudură. Sutura metalica in structura si structura sa difera de metalul de baza si de umplutura.
În locul încălzirii metalului primar prin sudarea arcului sau a flăcării arzătorului, se formează o cavitate umplută cu metal lichid, numită o baie de sudură.
2. Dezvoltarea sudurii și semnificația acesteia
Sudarea metalelor este una dintre cele mai remarcabile invenții rusești și a fost inițial stapânită în țara noastră, locul de naștere al multor descoperiri importante din domeniul științei și tehnologiei.
In 1802, rusul academicianul Vasile V. Petrov a atras atenția asupra faptului că există arc orbitor ardere (descărcare electrică), având o temperatură foarte ridicată între capetele lor prin trecerea unui curent electric prin două ace de carbon sau metal. El a studiat am descris acest fenomen și am subliniat și posibilitatea utilizării căldurii unui arc electric pentru a topi metalele și, prin urmare, a pus bazele sudării cu arc a metalelor.
Rezultatele experimentelor lui VV Petrov nu erau cunoscute în acel moment în străinătate, dar nu au fost folosite în Rusia. ingineri doar 80 de ani mai târziu Rusă - Nikolay Benardos și Nikolay Slavyanov aplicat deschiderea B. Petrova în practică și au dezvoltat diverse metode de metale industriale sudare electrică „arc Petrov.“
Procesul de îmbinare a pieselor metalice prin încălzirea lor locală în stare plastică sau topită se numește sudare. Sudarea poate fi efectuată fără a utiliza sau a exercita presiune pentru a comprima piesele sudate.
Toate metalele și aliajele sudate se referă la corpuri cristaline solide și constau dintr-un număr de granule separate - cristalite, interconectate prin forțe de interacțiune interatomică și intermoleculară. Pentru a conecta două particule de metal într-un singur întreg, trebuie să le apropiați atomii, astfel încât între ele să înceapă să acționeze forțele de atracție reciprocă. Acest lucru este posibil cu o distanță între atomi de aproximativ 4 • 10
8 cm (patru sute de milionimi dintr-un centimetru), ceea ce este fezabil numai în următoarele condiții:
1) aplicarea forțelor de compresie foarte mari ale pieselor fără încălzirea acestora;
2) încălzirea și compresia simultană a părților prin forțe moderate;
3) încălzirea metalului la joncțiune înainte de topire fără comprimare.
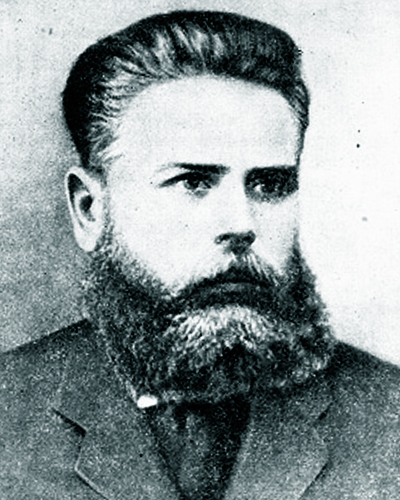
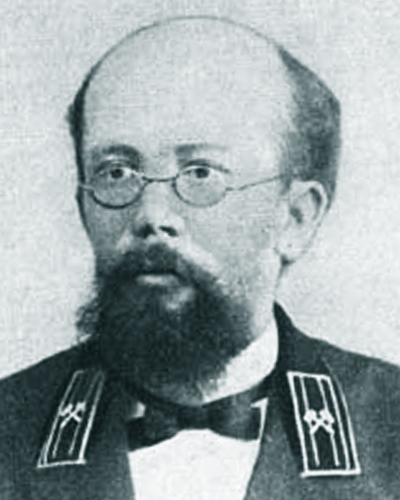
N. Benardos în 1882 a inventat o metodă de sudare cu arc folosind un electrod de carbon. În următorii ani el a dezvoltat metode de sudare cu arc de ardere între două sau mai multe electrozi; sudarea într-o atmosferă de gaz protector; contact de sudură cu puncte de contact; Au fost create numeroase modele de mașini automate de sudură. N. Benardos a brevetat în Rusia și în străinătate un număr mare de invenții diverse în domeniul echipamentelor de sudare și al proceselor de sudare.
Cu toate acestea, știința sudării și tehnicile metodelor avansate de sudură utilizate în prezent în țara noastră au fost dezvoltate în primul rând datorită lucrărilor multor oameni de știință sovietici, ingineri și lucrători inovatori de sudare. Ei au creat un număr mare de tipuri de echipamente de sudura, marci de electrozi dezvoltat procese noi si inovatoare de sudura, inclusiv foarte mecanizate și automatizate, să stăpânească tehnica de sudare a multor metale și aliaje, profund și cuprinzător a dezvoltat teoria proceselor de sudare.
În ultimii ani, sudarea de pretutindeni a înlocuit metoda de a nu conecta piese cu nituri.
Acum, sudarea este principala cale de îmbinare a pieselor în fabricarea structurilor metalice. Sudarea este utilizată pe scară largă în combinație cu turnarea, ștanțarea și laminarea specială a elementelor individuale ale pieselor de prelucrat, înlocuind aproape complet piesele turnate solide complexe și scumpe și semifabricatele din toate tipurile.
Sudarea oferă o serie de avantaje, dintre care principalele sunt prezentate mai jos:
1. economisirea de metal datorită utilizării cele mai complete a secțiunilor de lucru ale elementelor structurilor sudate, oferindu-le forma cea mai potrivită în concordanță cu sarcinile care acționează și reducând greutatea elementelor de legătură. În cazul construcțiilor sudate, greutatea metalului de sudură este de obicei de la 1 până la 2%, în timp ce în nituri greutatea niturilor și a eșarfei nu este mai mică de 4% din greutatea produsului. Sudarea produce până la 25% din economiile de metale în comparație cu un nit și, în comparație cu turnarea în unele cazuri, până la 50%.
Utilizarea sudării pe construcția clădirilor poate reduce cu 15% greutatea structurilor metalice, facilitează fabricarea și crește rigiditatea întregii structuri. În timpul construcției furnalelor, utilizarea de sudura în loc de capse permite economisirea de la 12 la 15% din metal, în construcții de ferme de ciment - 10-20%, în construcția de macarale - 15-20%.
2. Reducerea termenilor de muncă și reducerea costurilor de realizare a structurilor prin reducerea consumului de metale și reducerea ponderii forței de muncă. De exemplu, în construcția de furnale mari la uzinele metalurgice, fabricarea carcasei cuptorului din tablă de oțel prin sudare se realizează în mai puțin de două luni. Executarea unei astfel de carcase cu ajutorul unui nit necesită cel puțin șase luni.
3. Posibilitatea de a produce produse sudate de formă complexă din elemente ștanțate în loc de forjare sau turnare. Asemenea modele sunt numite ștampilate și sunt utilizate pe scară largă în industria de automobile, construcția de avioane, construcția de mașini. Cu ajutorul sudurii, este posibilă fabricarea pieselor metalice care au fost supuse diferitelor prelucrări preliminare, de exemplu sudarea secțiunilor laminate cu semifabricate ștanțate, turnate sau forjate. Puteți să sudați și metale diferite: oțeluri inoxidabile cu carbon, cupru cu oțel etc.
4. Posibilitatea unei utilizări extinse a sudării și a tăierii în timpul reparațiilor, în cazul în care aceste metode de prelucrare a metalelor vă permit să reparați repede și în mod rentabil echipamentul uzat sau în afara echipamentului și structurile distruse.
5. Reducerea costului echipamentelor tehnologice, deoarece nu este nevoie să se utilizeze mașini de foraj, perforare și mașini de nituit.
6. Grosimea îmbinărilor sudate.
7. Reducerea zgomotului industrial și îmbunătățirea condițiilor de muncă pentru lucrători.
Sudarea poate produce o îmbinare sudată cu rezistență deasupra metalului de bază. De aceea, sudarea este utilizat pe scară largă în fabricarea structurilor foarte critice care funcționează la presiuni și temperaturi ridicate, precum și dinamic (impact) încărcările - cazan de abur de înaltă presiune, poduri, avioane, structuri hidraulice, structuri din beton de armare si altele.
3. Clasificarea metodelor de sudare
Toate metodele de sudare pot fi împărțite în două grupe principale. Dacă la joncțiune părțile metalice sunt încălzite în stare plastică sau topită și apoi stoarse de o forță exterioară, în urma căreia sunt sudate, această metodă se referă la sudarea sub presiune.
În cazul în care sudarea are loc fără a aplica presiune, numai prin încălzirea metalului în locul sudării cu o sursă de căldură concentrată (arc, flacără arzător) la o stare topită cu formarea unei baze de sudură, această metodă se referă la sudarea prin fuziune.
Sunt de asemenea dezvoltate metode mecanice de sudare, care nu necesită costul energiei chimice sau electrice pentru încălzirea metalului. Acestea includ sudura la rece, efectuat datorită aplicării presiunii unității foarte ridicată la punctul de contact și pieselor de sudat precum sudarea prin frecare, atunci când se produce tije sudate de încălzire ca rezultat al frecării reciproce a capetelor pieselor sudate. Aceste metode sunt utilizate, de exemplu, pentru sudura de scule (sudare prin frecare), fire de aluminiu (sudare la rece) și în alte cazuri.
Dintre noile tehnici dezvoltate și introduse în producție în ultimii ani, este necesar să se sublinieze sudarea cu ultrasunete, presiunea în vid, sudarea cu fascicul de electroni într-o surfacing vibrodugovuyu vid, sudura cu încălzire de înaltă frecvență, sudare cu arc electric rotativ sudare cu jet de plasmă, și altele. Cu toate acestea, aceste Metodele de sudare au un scop special și domeniul de aplicare al acestora este mai limitat decât sudarea electrică cu arc sau contact; Ele sunt utilizate, de exemplu, în instrumentul pentru sudarea materialelor plastice sudarea aliajelor dure, placare straturi subțiri de metal, sudura de metal refractar și alte procese similare. Datele privind aceste metode de sudare pot fi găsite în literatură *.
Cea mai mare aplicație în industrie are metodele de sudare prin topire, folosind căldura unui arc electric de sudare.
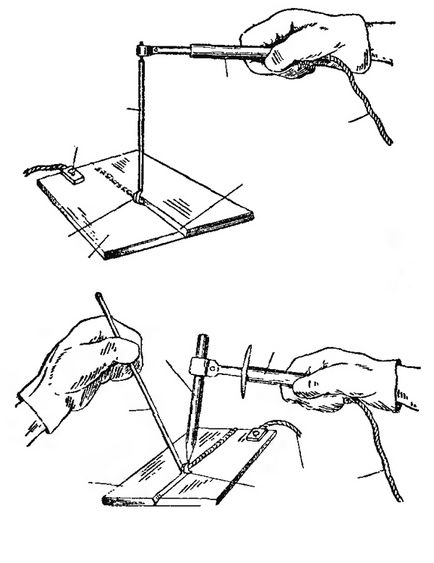
Fig. 2
Arc sudare:
a - un electrod metalic,
b - electrodul de cărbune
Cele două metode principale ale acestui tip de sudură cu arc sunt prezentate schematic în Fig. 2. La sudarea cu electrozi foi de metal 1 prin metoda G. N. Slavyanov (Fig. 2a) electrod 4 și muchia 7 a metalului de bază topit sudarea cu arc simultan 2Y care formează metalul lichid umple golul dintre piesele sudate. Pentru a îmbunătăți calitatea electrodului metalic depus este acoperit cu un daubing special, care se topește și acoperă stratul de zgură de metal lichid. Zgura este îndepărtată din parțial topit contaminanți metalici, oxigenul și alții. Și zgură protejează metalul de efectele nocive ale oxigenului și azotului ambiant. Curentul furnizat electrodului prin portelectrod un fir flexibil 5 la 6 și sudate la metal - al doilea fir prin clema 3. Această metodă este utilizată cel mai des în sudarea cu arc electric cu curent continuu și alternativ.
La sudarea unei foi de electrod de cărbune 1, prin metoda lui N. Benardos (Fig. 2b), electrod 3 nu este topit. Umplerea se realizează prin topirea barei de sudură metalică 2, introdus într-un arc de sudură 7. Curentul furnizat la electrodul prin fir 5 prin intermediul electrodului 4. Al doilea titular 6 este realizată printr-un clip atașat la metalul de bază. această metodă este rar folosit, deoarece o mai puțin convenabil, necesită utilizarea de curent continuu și nu produce întotdeauna calitatea dorită a metalului de sudură la sudarea oțelului. Această metodă este folosită în primul rând pentru sudarea cuprului, aluminiului, sudarea aliajelor dure și, uneori, la sudarea oțelului subțire.
Articole similare
Trimiteți-le prietenilor: