Lipire în vid și într-o atmosferă reducătoare
Când metalul este încălzit la temperaturi ridicate în condiții normale, oxigenul din aer își oxidează suprafața, formând scala. Prezența oxizilor face dificilă menținerea procesului de lipire. Pentru a le îndepărta și pentru a curăța suprafața la lipirea în aer, trebuie utilizate fluxuri speciale. Cu toate acestea, lipirea cu fluxuri, permițând obținerea unei conexiuni puternice, nu asigură protecția întregii suprafețe a părții de oxidare; astfel încât, după lipire, trebuie să curățați piesele de flux și scară. Pentru a evita acest lucru, se utilizează metode de izolare a articolelor încălzite din mediul aerian, permițând efectuarea unor procese de lipire neoxidante. Acestea includ lipirea în vid și lipirea într-o atmosferă reducătoare.
Lipire în vid. După cum sa menționat mai sus, unul dintre avantajele lipirii cu frecvență înaltă este capacitatea de lipire într-un vid. Avantajul lipirii în vid este acela că atunci când este încălzit într-un mediu în care nu există oxigen, nu există oxidare a metalului și pentru a obține o lipire de înaltă calitate nu este necesar să se utilizeze un flux. Cu modul corect de încălzire într-un lot de piese și o anumită întârziere, puteți fi siguri că calitatea lipirii va fi aceeași pentru toate părțile.
Primul dispozitiv de lipit în vid este o masă circulară, cu o suprafață de cupru lustruit pe care poate fi fixat la lipit elementul pregătit. Partea a fost acoperită cu un capac din sticlă, care se potrivea perfect marginilor sale lustruite pe suprafața mesei. Pentru o mai bună etanșare, suprafața mesei a fost lubrifiată cu vaselină tehnică. Aerul a fost pompat de sub capac prin gaura din masă. Cu o descărcare de aproximativ 10 ~ 3 mm Hg. Art. care a fost realizat în câteva secunde, partea a fost gata pentru lipire.
Situat deasupra capacului de sticlă, inductorul, atunci când generatorul a fost pornit, a transmis energia de înaltă frecvență către piesa sudată la fel de intensă ca atunci când a fost lipită în aer. Pe un astfel de dispozitiv primitiv în laborator prof. VP Vologdin a făcut primele experimente privind lipirea pieselor și uneltelor de tăiere în cupru cu aliaje de cupru și argint.
Oarecum mai târziu, a fost creată și o mașină automată pentru lipirea bujiilor de combustie internă (figura 1). În slotul special pe placa rotativă masivă din cupru, răcit cu apă, piese instalate, care sunt capace închise top sticlă sudate. Prin rotirea spațiul de masă care se află sub capacul nou instalat împerecheat cu un sistem special de canale cu o pompă de vid, și cu condiția că există o primă DATEM preparativă și vid înalt. Masa cu detalii, cu ajutorul unui sistem special de acționare, a făcut mișcare de rotație, periodic, la intervale regulate, întorcându-se sub un unghi. Într-o anumită poziție, capacul era acoperit cu un inductor inelar și, în același timp, generatorul era pornit. Partea a început instantaneu să se coste. După încălzirea la temperatura dorită și se topesc de lipire inductor ascendentă, încălzirea a fost oprită și masa mutat în poziția următoare, după care încălzirea este începută următoarele elemente. Astfel, detaliile cozii apropie inductor, în care o parte din energia necesară pentru a li se topească de lipire și de lipire preparare. După încălzire, piesele au fost răcite, transferând căldură într-o masă de cupru, răcită intens de apă. La capătul spațiului de lipit sub capacul de ceva timp nu este conectat la aerul din jur, ca pentru a îndepărta capacul înainte de partea sa răcit la o temperatură de 100-150 ° C, suprafața oxidează și se închide la culoare. Detaliile, răcite în vid, au o suprafață strălucitoare, de parcă ar fi fost lustruite. Calitatea lipirii pieselor în vid este extrem de ridicată.
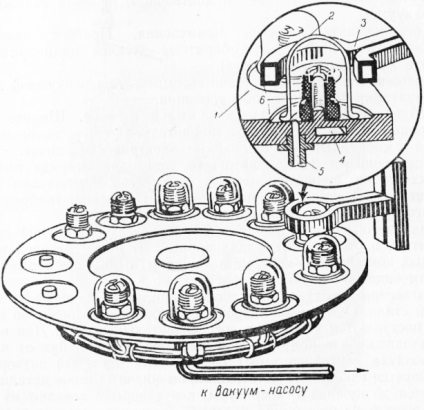
Fig. 1. Diagramă de mașină-unelte pentru lipirea pieselor în vid: 1 - tabel de cupru; 2 - un capac din sticlă; 3 - inductor; 4 canale pentru răcirea cu apă a mesei; 5 - canalul de pompare a aerului; v - piese de lipit
În ciuda unui număr de aspecte pozitive ale procesului de lipire cu frecvență în vid, domeniul aplicării sale este încă foarte limitat până în prezent.
Pentru motivele care împiedică utilizarea sa în industrie, este necesar să se atribuie:
1) productivitatea relativ scăzută a procesului datorată încălzirii prin piesă a pieselor și o perioadă lungă de răcire a acestora în vid;
2) un domeniu de aplicare limitat. Procesul este potrivit, în principal, pentru lipirea pieselor cilindrice de dimensiuni mici în producția de masă;
3) complexitatea creării de mașini automate de lipire în vid și de funcționare a echipamentelor sub vid.
Lipire într-un mediu reducător. Procesul de lipire a cuprului într-un mediu reducător, care se realizează în cuptoare electrice special echipate, este cunoscut.
Deficiențele sale esențiale, în prezența unui număr de aspecte pozitive, sunt costul ridicat al echipamentului și lipsa acestuia. Cuptoarele în care are loc procesul de lipire necesită o perioadă lungă de încălzire și răcire.
Având în vedere că cuptoarele speciale cu un mediu reducător sunt rare, în unele cazuri se realizează lipirea pieselor în recipiente speciale, care sunt încărcate în cuptoare termice convenționale cu temperatură ridicată.
Containerele sunt cutii fabricate din oțel rezistent la căldură. Acestea au tuburi sudate, prin care, în timpul lipirii, gazele reducătoare intră și părăsesc. Pentru a izola piesele din container în timpul lipirii de oxigen în aer, recipientul are o închidere specială cu nisip sau este acoperit cu lut. După ce perioada de încălzire a pieselor este la temperatura dorită, recipientele sunt scoase din cuptor și răcite, continuând să furnizeze mediul reducător până când părțile s-au răcit.
Această metodă de lipire este foarte imperfectă, deoarece durează mult timp și permite un număr foarte mic de piese care trebuie să treacă la un consum mare de energie.
Mai mult proces productiv se brazare încălzirea în recipiente cu curenți de înaltă frecvență (Fig. 2). Această specie de lipit numai să fie în mod convențional numit de înaltă frecvență, deoarece, spre deosebire de ceea ce se observă pentru toate celelalte metode de încălzire de înaltă frecvență, aici curenții cu greu sunt induse în partea sine și containerul încălzit, care are, la rândul său, transferă căldura la elementul prin conductivitatea termică a mediului reducător. Ai pierdut unul dintre avantajele de încălzire de înaltă frecvență - capacitatea de a încălzi numai zona de piese necesare.
Ciclul de lipire a pieselor dintr-un container cu încălzire de înaltă frecvență poate fi redus de câteva ori în comparație cu ciclul de lipire în cuptoare. Acest lucru ne permite să folosim ca aliaje de lipit nu numai cupru, ci și alama. Cu metodele existente de lipire într-un mediu reducător, alama nu a putut fi utilizată ca un lipitor, deoarece încălzirea prelungită le-a afectat în mod negativ proprietățile.
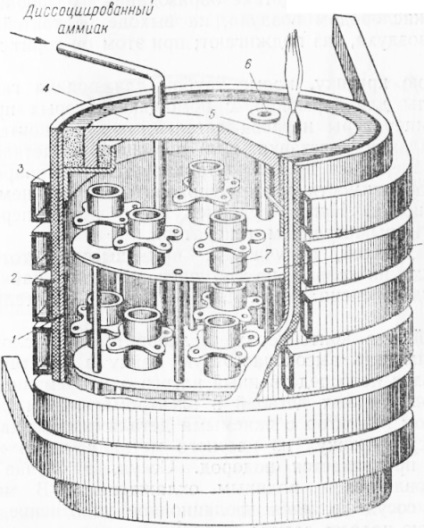
Fig. 2. Diagrama containerului pentru brazare de înaltă frecvență într-un mediu reducător cu încălzire indirectă a pieselor: 1 - corpul recipientului; 2 straturi de izolație termică; 3 - inductor; 4 - capacul recipientului; 5 - un tub pentru alimentarea și îndepărtarea unui mediu reducător; 6 - priză pentru termocupluri; 7 - parte sudată; 8 - stand
Container cu un sistem de încălzire de înaltă frecvență este realizată prin sudarea din tablă de oțel rezistent la căldură ca un butoi, care este instalat pe un suport izolant termic. Containerul este plasat într-un inductor cu mai multe ture. Între inductor și container, este pus un strat termoizolant pentru a reduce pierderea de energie la radiație. Partea inferioară a containerului este realizată cu mai multe ondulații pentru ao proteja de distrugere datorată solicitărilor termice în timpul încălzirii și răcirii multiple. Prin capacul masiv superior se introduc și se elimină gaze reducătoare, cel mai bun din care este amoniacul disociat.
În timpul încălzirii pentru lipirea și răcirea recipientului, gazul trebuie să curgă continuu în acesta. Pentru a exclude posibilitatea unei explozii în încăpere datorită formării unui amestec exploziv de hidrogen cu oxigen de aer, la ieșirea din recipient, după expulzarea aerului, gazul este aprins; în timp ce arde flacără gălbui.
În capacul superior, pe lângă conductele de alimentare cu gaz, este necesară sudarea capacelor termocuplurilor, prin care se controlează temperatura de încălzire a pieselor; Pe partea inferioară a containerului este amplasat un suport special pentru a plasa piesele. Încălzirea pereților recipientului este controlată întotdeauna de un termocuplu care, dacă este necesar, poate controla pornirea și oprirea unității. Încălzirea se face în mod convenabil prin pornirea și oprirea periodică a generatorului.
Calitatea pieselor obținute prin lipirea cu frecvență înaltă în recipiente nu este inferioară calității pieselor de lipit realizate în cuptoare speciale cu o atmosferă de reducere.
Pe lângă lipirea în recipiente, în condiții de laborator, este ușor și simplu să se folosească un dispozitiv de lipire de înaltă frecvență într-un mediu reducător, folosind încălzirea directă simultan a uneia sau a mai multor părți similare în câmpul electromagnetic al inductorului. În acest caz, inductorul cu părți sudate este plasat într-un vas special - o carcasă din metal neferoasă, prin care se trece prin hidrogen în timpul lipirii. Vasul, dacă este necesar, este fabricat cu răcire cu apă. La locul de intrare al inductorului, se face o izolație izolată în vas, care protejează cavitatea interioară a vasului de penetrarea aerului și inductorul de la închiderea terminalelor. Părțile din inductor sunt încărcate printr-un orificiu care, înainte de trecerea gazului, este etanșat ermetic cu un capac cu fereastră de inspecție (Figura 3).
Gazul este umplut și manipulat cu gaz în același mod ca atunci când este folosit pentru lipirea recipientelor cu un mediu reducător. Încălzirea pieselor în timpul lipirii trebuie efectuată pe modul consumat cu o anumită întârziere, obținută experimental. Alimentarea cu gaz este oprită după răcirea pieselor la o temperatură sub 100-120 ° C, după care pot fi înlocuite cu următoarele. În acest procedeu se poate folosi hidrogen, care se obține în condiții de laborator în aparatul Kipp prin acțiunea acizilor pe zinc, urmată de purificarea și îndepărtarea umidității. Debitul de gaz și presiunea în vas pot fi nesemnificative, dar trebuie să fie suficiente pentru a menține continuu combustia gazului la ieșire. Pe tubul de ieșire ar trebui să fie pus pe un vârf de sticlă, umplând cu trompete de cupru. Scopul său este de a preveni izbucnirea hidrogenului în vas și, prin urmare, să asigure un mediu de lucru sigur. Un dezavantaj semnificativ al hidrogenului ca mediu reducător este capacitatea sa de a forma amestecuri explozive cu oxigenul aerului, ceea ce necesită multă atenție și respectarea exactă a instrucțiunilor de manipulare a hidrogenului.
În ciuda productivității scăzute și a capacităților limitate, lipirea cu încălzire directă a pieselor este un proces mult mai perfect decât lipirea prin încălzirea pieselor în recipiente.
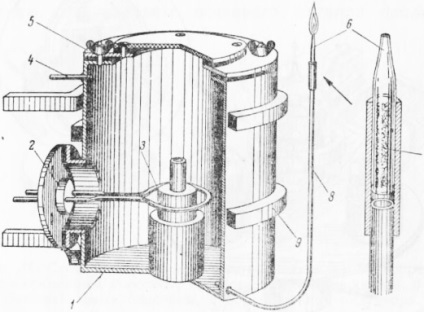
Fig. 3. Diagramă a dispozitivului pentru brazare de înaltă frecvență într-un mediu reducător cu încălzire directă a pieselor: 1 - un vas; 2 - etanșare izolantă; 3 - inductor cu o parte sudată; 4 - un tub pentru alimentare cu gaz; 5 - capacul navei; 6 - vârful de siguranță; 7 - chipsuri de cupru; 8 - un tub pentru îndepărtarea gazului; 9 - tubul de răcire
Din păcate, până acum, sudarea cu frecvență înaltă a pieselor într-un vid și un mediu reducător nu a găsit o aplicare largă, deși aceste procese sunt procese tehnologice progresive care merită o atenție sporită.
La dispozitivele de acest tip pot fi produse în atmosferă de gaz neutru, cum ar fi sudura argon. Argon protejează piese în timpul încălzirii de oxidare, creează condiții mai favorabile pentru udarea metalul de bază și Wicking de lipire în golurile sale. Este de dorit să se utilizeze argon, conținând cantitatea minimă de impurități, în special oxigen. Brazare în argon, mai bine lipit în aer, dar mai rău de lipit în hidrogen, deoarece necesită o anumită cantitate de flux și oferă conexiune mai puțin frumoasă. Argon este mai dens decât aerul, el nu arde si nu intretine arderea, deci este convenabil să se ocupe în timpul lipirii. De asemenea, este posibil să se efectueze cu ușurință lipit în părți fine sub capace de sticlă cu argon, similară cu cea produsă în cazul de lipire cu vid (Fig. 4). Un astfel de proces este adecvat să se aplice atunci când părțile au cavități interioare care necesită o protecție împotriva oxidării în timpul lipirii. În acest caz, alimentarea cu gaz poate fi un dispozitiv special de distribuție, aranjate în placa turnantă prin orificiul de sub piesa de prelucrat prin lipire, și apoi fluxul de gaz prin ciorap, la partea superioară a capacului de sticlă.
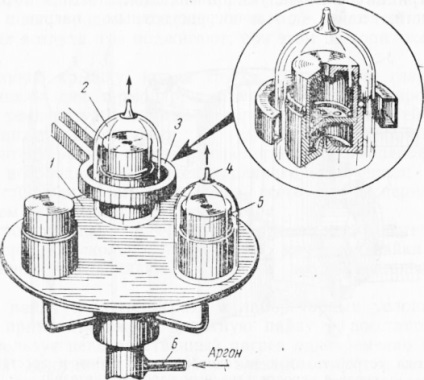
Fig. 4. Diagrama dispozitivului pentru lipirea pieselor în argon: 1 - tabel de cupru; 2 - un capac din sticlă; 3 - inductor; 4 - capac cap cu o priză de gaz; 5 - piese sudate; 6 - un tub pentru curățarea gazului
În aceleași scopuri, atunci când se realizează brazarea unor tipuri de piese în aer, este posibilă arderea argonului prin cavitățile interne ale pieselor, de exemplu, în timpul lipirii la înaltă frecvență a conductelor de combustibil de înaltă presiune responsabile. Dacă condițiile de lucru și construcția părții permit, cu măsuri de precauție adecvate, se poate folosi hidrogen în loc de argon, care asigură o protecție mai fiabilă împotriva oxidării suprafeței interioare a piesei.
Citește mai mult:
Articole similare:
Articole similare
Trimiteți-le prietenilor: