Prelucrarea prin tăiere este o metodă universală de procesare dimensională. Metoda permite prelucrarea suprafețelor de piese de diferite forme și mărimi cu precizie ridicată din cele mai utilizate materiale de construcție.
Are un consum redus de energie și performanță ridicată. Ca rezultat, prelucrarea prin tăiere este principalul proces de prelucrare dimensională a pieselor care sunt cele mai utilizate în industrie.
Esență și scheme de metode de procesare
Prelucrare - un proces de primire elementele necesare formă geometrică, precizie dimensională, rugozitatea suprafeței și poziția relativă de suprafețele de tăiere mecanice cu alocația tehnologică a piesei de prelucrat scule de tăiere în formă de așchii de material (Figura 1.1.).
Elementul principal de tăiere al oricărei scule este panta de tăiere (Figura 1.1, a). Duritatea și rezistența acestuia ar trebui să depășească în mod semnificativ duritatea și rezistența materialului prelucrat, asigurându-i proprietățile de tăiere. O forță de tăiere egală cu rezistența materialului la tăiere este aplicată sculei și mișcarea relativă la piesa de prelucrat este raportată la o viteză # 957; Sub influența aplicată tăierea pană în piesa de prelucrat și forța, distrugerea materialului prelucrat, taie o așchii de suprafață a piesei de prelucrat. Așchiile formate ca urmare a unor deformări intensive de compresie materialului elastoplastic, aceasta duce la distrugerea tăișului și forfecare în zona de stres maxim de forfecare la un unghi # 966 ;. valoare # 966; depinde de parametrii de tăiere și de proprietățile materialului prelucrat. Este
30 ° față de direcția de deplasare a sculei.
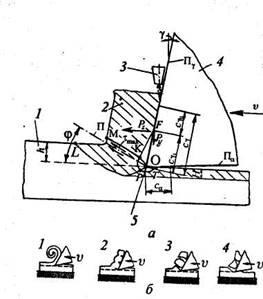
Aspectul rumegușului caracterizează procesele de deformare și distrugere a materialului care apar în timpul tăierii. Există patru tipuri posibile de chipsuri formate: drenaj, îmbinare, element și rupturi ale fracturii (Fig.1.1, b).
Fig. 1.1. Schema condiționată a procesului de tăiere:
a - 1 - material prelucrat; 2 - rumeguș; 3 - furnizarea de agenți de răcire lubrifianți; 4 - pană de tăiere; 5 - muchie de tăiere; # 966; - unghiul de forfecare, care caracterizează poziția planului de forfecare convențional (П) față de planul de tăiere; # 947; - unghiul principal al panoului de tăiere; Pz este forța de tăiere; Py este forța presiunii normale a sculei pe material; C # 947; u. C # 947; l - lungimea contactelor din plastic și elastic; C # 947; Ca este lungimea zonelor de interacțiune de contact de-a lungul suprafețelor din față și din spate ale sculei; LOM - regiunea deformării elastoplastice principale în timpul formării așchiilor; FKPT - zona de deformare plastic-elastic-plastic secundar de metal; h - adâncimea tăieturii; H este grosimea zonei de deformare plastică (munca grea) a metalului.
În timpul procesului de tăiere, pivotul de tăiere, care se confruntă cu frecare intensă, intră în contact cu materialul cipului și suprafața tratată în zonele de contact. Pentru a reduce forțele de frecare și a încălzi scula, se aplică răcirea forțată a zonei de tăiere prin medii de lubrifiere-răcire (SOS) prin alimentarea lor în zona de tăiere cu dispozitive speciale.
Piesele și uneltele sunt fixate în mașini sau dispozitive speciale. Mașina, scula, scula și piesa formează un sistem de alimentare (SIDA), transmiterea forței și mișcarea de tăiere de la unitatea mașinii la scula și piesele de tăiere.
Schemele reale ale diferitelor metode de tăiere, unealta utilizată, precum și tipurile de mișcare a sculei și a piesei de prelucrat în timpul procesării sunt prezentate în Fig. 1.2. În funcție de tipul de scule utilizate, metodele de prelucrare sunt împărțite în lamă și abrazive.
Fig. 1.2. Scheme de metode de tăiere:
a - întoarcere; b - foraj; c - măcinare; d - plantare; d - broșare; e - măcinare; ж - honuire; h - superfinisare; Dr este mișcarea principală de tăiere; Ds este mișcarea de alimentare; Suprafață prelucrată cu suprafață roșie; R - suprafața de tăiere; ROP - suprafața tratată; 1 - instrument de strunjire; 2 - burghiu; 3 - un frezat; 4 - instrument de planificare; 5 - broșare; 6 - roată abrazivă; 7 - hon; 8 - bare; 9 - capul.
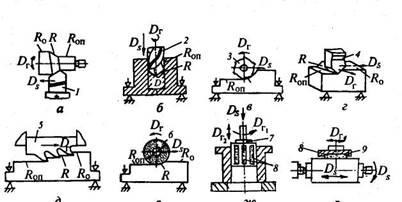
O trăsătură distinctivă a prelucrării de ultimă oră este disponibilitatea marginii de prelucrare instrument ostroyrezhuschey definit formă geometrică și abraziune - prezența boabelor orientate diferit ale sculei de tăiere abrazivă, fiecare dintre acestea reprezentând un microcline.
Fig. 1.3. Proiectare și elemente de unelte de tăiat lame:
a - unelte de strunjire; b - tăietori; c - exerciții;
1 - marginea de taiere principală; 2 - suprafața principală din spate; 3 - partea superioară a lamei; 4 - suprafața spate auxiliară a lamei; 5 - marginea de tăiere auxiliară; 6 - suprafața frontală; 7 - partea de fixare a sculei.
Luați în considerare proiectarea uneltelor cu lamă utilizate la tăiere (Figura 1.3). Uneltele constau dintr-o piesă de lucru care include lamele de tăiere care formează suprafețele lor, muchiile tăietoare și o piesă de fixare destinată montării și fixării în piesele de lucru ale mașinii.
Principalele metode de prelucrare a lamei sunt strunjirea, găurirea, frezarea, așezarea și șlefuirea. Prelucrarea abrazivă include procesele de măcinare, honuire și superfinisare. Clasificarea metodelor de prelucrare se bazează pe tipul de instrument utilizat și pe cinematica mișcărilor. Astfel, ca un instrument in timpul pornirii este folosit freze de strung, forare - burghiului, frezare - freze, rabotare - rabotare taietoare, când se trage - broșă, când slefuire - abrazive, honuire - Hones și la SUPERFINISH - bare abrazive. Orice metodă de procesare include două mișcări (Figura 1.2.): Principalul lucru este mișcarea de tăiere Dr - și mișcarea auxiliară - mișcarea de alimentare Ds. Mișcarea principală asigură îndepărtarea metalului, iar mișcarea auxiliară asigură următoarea secțiune netratată a piesei de prelucrat în zona de prelucrare. Aceste mișcări sunt efectuate prin deplasarea piesei sau a uneia. Prin urmare, atunci când se evaluează mișcarea sculei în toate procesele de tăiere, este convenabil să se considere piesa totală ca un martor fix (Figura 1.4).

Fig. 1.4. Scheme pentru determinarea vitezei maxime de tăiere a sculei # 965; forma suprafeței de tăiere R și adâncimea de tăiere h în timpul prelucrării:
a - întoarcere; b - foraj; in - frezare; r - plantare; prin tragere; e-honing; g - superfinisare.
Apoi, viteza totală de deplasare (ve) a unui punct arbitrar al marginii de frezare este însumată din viteza mișcării principale (v) și viteza de avans (vs):
Suprafața de tăiere R este suprafața pe care o descrie marginea de tăiere sau cereale atunci când efectuează mișcarea totală, inclusiv mișcarea principală și mișcarea de alimentare. La strunjire, forare, frezare, slefuire a suprafetei de taiere - linia spatiala, atunci cand se rostogoleaza si trage - plat, coincide cu suprafata miscarii principale; Când se lucrează și se finalizează, ele coincid cu suprafețele mișcării principale.
Suprafețele Ro și Ro sunt numite, respectiv, suprafața piesei de prelucrat a piesei de prelucrat și suprafața prelucrată a prelucrării (vezi Figura 1.2).
În procesele de strunjire, găurire, frezare și măcinare, mișcarea principală și mișcarea de alimentare sunt realizate simultan, iar în planificarea, honuirea, mișcarea de alimentare este efectuată după mișcarea principală.
2. Parametrii procesului tehnologic de tăiere
Parametrii principali ai modului de tăiere includ viteza mișcării principale de tăiere, viteza de avans și adâncimea tăierii.
Viteza mișcării principale de tăiere (sau a vitezei de tăiere) este determinată de viteza maximă liniară a mișcării principale a marginii de tăiere a sculei. Această viteză este exprimată în m / s.
În cazul în care tăierea principală mișcarea de rotație, ca și în strunjire, găurire, frezare și măcinare, viteza de tăiere va fi determinată de viteza liniară a îndepărtat principal mișcare de axa de rotație a punctelor de margine de taiere - viteza liniară maximă a mișcării principale (vezi Figura 1.4 ..):
unde D este diametrul maxim al suprafeței piesei de prelucrat a piesei de prelucrat, care determină poziția punctului de tăiere cel mai îndepărtat de axa de rotație, m; # 969; - viteza unghiulară, rad / s.
Exprimarea vitezei unghiulare # 969; prin viteza arborelui mașinii, obținem:
Atunci când se plantează și se trage, viteza de tăiere v este determinată de viteza mașinii de tăiere și de tragere în timpul tăierii în raport cu piesa de prelucrat.
La găurirea și superfinisarea, viteza de tăiere se determină ținând seama de deplasarea axială (vezi figura 1.4, e, g) a sculei.
Viteza de tăiere are cel mai mare impact asupra productivității procesului, durabilității instrumentului și calității suprafeței tratate.
Rata de alimentare a unui instrument este determinată de viteza sa vs. În calculele tehnologice ale parametrilor regimului de strunjire, forare, frezare și șlefuire, conceptul de alimentare a piesei de prelucrat. Pentru o rotație se utilizează și se exprimă în mm / rev. Alimentarea pe revoluție corespunde numeric cu mișcarea sculei în timpul unei singure revizuiri:
Când se plantează, feed-ul este determinat de cursa instrumentului. Când se mănâncă, avansul poate fi indicat prin cursa sau cursa dublă a sculei. Alimentarea per dinte în timpul frezării este determinată de numărul de dinți Z al sculei și de alimentarea pe revoluție:
Adâncimea tăierii A este determinată de distanța de-a lungul normalului de la suprafața prelucrată a piesei de prelucrat la piesa de lucru, mm. Adâncimea tăierii este stabilită pentru fiecare cursă de lucru a sculei. La întoarcerea unei suprafețe cilindrice, adâncimea de tăiere este definită ca jumătatea diferenței dintre diametre la z: după prelucrare:
unde d este diametrul suprafeței tratate a piesei de prelucrat, mm. Cantitatea de hrană și adâncimea tăierii determină productivitatea procesului și au o mare influență asupra calității suprafeței care trebuie tratată.
Parametrii procesului includ geometria instrumentului de tăiere, forța de tăiere, capacitatea de procesare și durata de viață a sculei.
Parametrii geometrici ai sculei de tăiere sunt determinați de unghiurile formate prin intersecția suprafețelor lamei, precum și de poziția suprafețelor lamelor de tăiere față de suprafața prelucrată și direcția mișcării principale. Acești parametri sunt identici pentru diferite tipuri de unelte, ceea ce ne permite să le luăm în considerare utilizând exemplul unui instrument utilizat pentru întoarcere.
Unghiurile de tăiere de-a lungul suprafețelor din față și din spate sunt măsurate în anumite planuri de coordonate. În Fig. 2.1a prezintă planurile de coordonate la rotire, iar Fig. 2.1, b colturile sculei din statica.
Colțul frontal principal # 947; - unghiul dintre suprafața frontală a lamei și planul perpendicular pe planul tăierii; colțul din spate principal # 945; - unghiul dintre suprafața posterioară a lamei și planul de tăiere; unghiul de ascuțire # 946; - Unghiul dintre suprafețele din față și din spate. Din principiul construirii unghiurilor, rezultă că
# 945; + # 946; + # 947; = π / 2.
Unghiul de înclinare al marginii de tăiere X este unghiul în planul de tăiere dintre muchia de tăiere și planul principal.
Unghiuri în plan: unghiul principal în plan # 966; - unghiul din planul principal dintre calea planului de tăiere și direcția alimentării longitudinale; unghiul auxiliar în plan # 966; - Unghiul în planul principal dintre muchia de tăiere auxiliară și suprafața prelucrată.
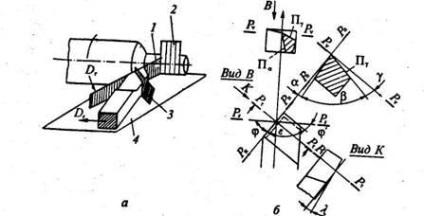
Fig. 2.1. Parametrii geometrici ai instrumentului de strunjire:
a - planuri de coordonate; b - unghiurile sculei în statica;
1 - planul de tăiere Pn; 2 - planul de lucru Ps; 3 - planul principal Pt; 4 - planul principal Pv
Parametrii geometrici ai sculei de tăiere au un efect semnificativ asupra forței de tăiere, calității suprafeței și uzurii sculei. Astfel, pe măsură ce crește unghiul y, scula se taie mai ușor în material, forțele de tăiere scad, calitatea suprafeței se îmbunătățește, însă uzura sculei crește. Prezența unui unghi a reduce frecarea sculei pe suprafața de tăiere, reducându-și uzura, dar creșterea excesivă slăbește marginea de tăiere, contribuind la distrugerea acesteia sub sarcini de impact.
Forțele de tăiere P sunt forțele care acționează asupra sculei de tăiere în procesul de deformare elastoplastică și distrugerea așchiilor tăiate.
Forțele de tracțiune conduc la vârful lamei sau la punctul muchiei tăietoare și sunt reprezentate grafic de-a lungul axelor coordonate ale sistemului de coordonate dreptunghiulare xyz (Figura 2.2). În acest sistem de coordonate, axa z este direcționată de-a lungul vitezei mișcării principale și direcția sa pozitivă corespunde direcției de acțiune a materialului care trebuie prelucrat pe sculă. Axa y este direcționată de-a lungul razei cercului mișcării principale a vârfului. Direcția sa pozitivă corespunde și direcției de acțiune a metalului pe sculă. Direcția axei x este aleasă din condiția de formare a sistemului de coordonate drept. Valoarea forței de tăiere este determinată de mai mulți factori. Se mărește cu adâncimea în creștere h a debitului și vitezei de alimentare s (secțiunea transversală a așchiilor tăiate), viteza de tăiere # 957; coborârea colțului din față # 947; instrumente de tăiere. Prin urmare, calculul forței de tăiere se realizează în conformitate cu formulele empirice stabilite pentru fiecare metodă de tratare (vezi manualele de prelucrare). De exemplu, pentru plantare această formulă are forma P = Cp h X p s Y p X n unde coeficienții Cp. Cro. Yp. n caracterizează materialul piesei de prelucrat, tăietor și tipul de prelucrare.
Puterea procesului de tăiere este determinată de produsul scalar:
Exprimând acest produs prin proiecțiile de-a lungul axelor de coordonate, obținem:
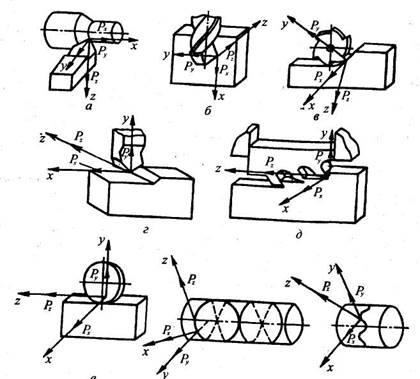
unde vx. vy. vz - proiecții pe axa coordonatelor vitezei punctului de aplicare a forțelor de tăiere rezultate. În calculele practice, se folosește dependența aproximativă N = Pz v. Această simplificare se datorează faptului că componentele Py și Px ale forței de tăiere totale sunt mici în comparație cu P2. iar viteza de avans în raport cu viteza de tăiere este de numai 1 până la 0,1%.
Fig. 2.2. Schema de acțiune a forțelor de tăiere pe marginea de tăiere a sculei într-un punct cu viteza maximă de mișcare # 957; când procesează: a - rotire; b - foraj; in - frezare; r - plantare; prin tragere; e-honing; g - superfinisare.
Capacitatea de prelucrare a tăierii este determinată de numărul pieselor fabricate pe unitate de timp: Q = \ / Tm. Timpul de fabricație pentru o parte este Tm = Tg + Tm + Tkp. unde To - timpul de prelucrare consumat de procesul de tăiere este determinat pentru fiecare proces; Тt - timpul de apropiere și retragere a sculei la prelucrarea unui detaliu; GVSp - timpul de instalare auxiliară și setările instrumentului.
Astfel, productivitatea prelucrării este determinată în principal de timpul mașinii T0. La întoarcere, min: To = La / (nso h), unde L - lungimea estimată a cursei sculei, mm; a - mărimea ajutorului pentru prelucrare, mm.
Raportul a / h caracterizează numărul necesar de treceri ale sculei atunci când se lucrează cu adâncimea de tăiere I. Prin urmare, cea mai mare productivitate va fi atunci când prelucrarea cu adâncimea de tăiere h = a, viteza maximă de avans s0 și viteza maximă de tăiere. Cu toate acestea, pe măsură ce crește productivitatea, calitatea suprafeței scade, iar uzura sculei crește. Prin urmare, atunci când se taie, sarcina este de a stabili capacitatea maximă admisă, menținând în același timp calitatea dorită a suprafeței și durata de viață a sculei.
Articole similare
Trimiteți-le prietenilor: