REDUCEREA COSTURILOR DE ENERGIE LA PRODUCȚIA COȘULUI
Intensitatea energetică a cocsului metalurgic este de 1170 - 1180 kg. t / t de cocs. Aproximativ 200 kg. este consumat în timpul producției, care este aproximativ de două ori mai mare decât atunci când primește o tonă de încărcare aglomerată. Cu toate acestea, având în vedere distribuția proporției acestor materiale în amestec (aproximativ 1.7-1.8 țunderul și peleți și cocs de 0,5 tone per 1 tonă de fontă) rol energetic în obținerea de cocs în consumul de energie de fier este mai mic decât costul de preparare a minereului de fier.
Principalele modalități de a reduce costurile de combustibil și de energie în producerea cocsului sunt asociate cu încălzirea încărcăturii de cărbune și cu călirea uscată a cocsului. De obicei, cărbunele încărcate în cuptorul de cocs au un conținut de umiditate de 6 până la 12%. Când căldura este încălzită la 150 - 200 ° C, devine aproape uscată. Utilizarea cărbunelui încălzit crește simultan productivitatea cuptoarelor de cocs și îmbunătățește calitatea cocsului. În ceea ce privește încălzirea, intensitatea energetică a cocsului este redusă cu 5 până la 15 kg. t / t. În general, metodele de încălzire a cărbunelui nu au fost încă dezvoltate. Perspectiva este încălzirea și uscarea cărbunelui zdrobit în pat fluidizat. Curățirea uscată a cocsului permite reducerea intensității sale energetice cu 40-50 kg. t / t. Instalațiile de răcire uscată a cocsului au fost dezvoltate pentru prima dată în URSS, iar lucrul principal este extinderea. aplicațiile lor. În prezent, numai 15-20% din cuptoarele cu cocs sunt echipate cu aceste unități.
Economisirea cocsului în furnale.
În intensitatea energetică; fontă brută și fracțiunea de cocs de mai puțin RES de combustibil gaz natural (200 - 250 kg în t / t de fontă brută ..) au o medie de 57 de - 62%, taxa 21 - 23%, oxigen 3,5% -4.5, aer 2 - 2,5% din explozie. Particularitatea utilizării combustibilului în furnal este că 65 până la 70% din energia sa este cheltuită pentru reducerea fierului din minereu. De exemplu, reacția de reducere indirectă cu coeficienți stoechiometrice, în conformitate cu condițiile de echilibru, la 700 ° C (Fe echilibru cu CO / CO2 = 1,5).
FeO + 2,5CO = Fe + CO2 + 1,5CO
rezultă că pe kg de fier se consumă 0,536 kg de carbon. Prin urmare, nu este posibilă reducerea semnificativă a intensității energetice a fontei. Când se suflă diferiți aditivi de combustibil în furnale, obiectivul principal este de a economisi cocsul redus prin utilizarea combustibililor cu deficit mai mic - gaz natural, păcură, praf de cărbune etc.
Etapa inferioară a transferului de căldură sau zona de reducere directă a fierului este factorul determinant în consumul de cocs. Creșterea capacității de reducere a gazelor prin introducerea unui combustibil cu hidrocarburi este asociată cu o creștere a concentrației de CO și H2. În aceeași direcție, îmbogățirea exploziei cu oxigen și utilizarea aglomeratelor și peletelor fluxate acționează. Hidrogenul crește în mod semnificativ rata de recuperare a materialului de minereu. Odată cu creșterea conținutului de reducere a gazelor și a presiunii acestora, gradul de reducere indirectă a fierului crește, ceea ce duce de obicei la o reducere a consumului de cocs. Cu toate acestea, efectul combustibilului suflat și alți factori au un efect mixt asupra funcționării cuptorului și economisirea cocsului. Între cantitatea de combustibil injectat, debitul de oxigen, temperatura de încălzire și umiditatea aerului blast trebuie stabilite anumite raporturi în care condițiile sunt optime ale cuptorului. Acestea corespund unei anumite stări de temperatură a stadiului inferior al schimbului de căldură al cuptorului și regimului său gaz-dinamic. De exemplu, teoretic și practic este dovedit, că cel mai mare beneficiu economic se realizează cu ajutorul unei explozii combinate dacă 1 m3 de oxigen suflate 1,1 - 1,2 m 3 de gaze naturale, 0,8 -1.0 petrol sau cărbune kg praf. Consumul curent de gaze naturale și oxigen este de 100-120 m 3 / t. aer de înaltă temperatură explozie este de aproximativ 1100 ° C, programat ascensiunea treptată până la 1200 ° C (în unele cazuri, folosind duza bulk 1300-1400 ° C). Reducerea maximă preconizată a consumului de cocs datorită optimizării parametrilor de explozie va fi de aproximativ 100 kg / t, i. E. Consumul de cocs nu va scădea, în medie, la peste 400 kg / t.
Injecția fierbinte de reducere a gazelor, de exemplu, obținut prin tratarea (spălarea gazului superior din CO2) conversia gazelor naturale și a altor combustibili este prezis ar trebui să conducă la o scădere suplimentară a consumului de cocs (Figura 8.2.) (Până la 300 - 350 kg / m sau mai puțin) și crește productivitatea cuptoarelor. Când se utilizează gazul superior purificat se presupune a elimina aproape complet utilizarea gazelor naturale tot mai rare și de a reduce costurile de producție reduse de fier.
Cerințele principale pentru gazul de reducere: concentrația maximă de CO și H2 în acesta cu conținutul minim de CO2. H2O, CH4 și funingine. Gazul reducător poate fi obținut prin conversia combustibilului de hidrocarburi și gazeificarea cărbunelui cu oxigen, dioxid de carbon și abur. Unii indicatori ai proceselor de conversie a gazelor naturale sunt prezentate în Tabelul. 8.1 și 8.2. Conversia de oxigen pentru costurile de capital și costurile de operare este cea mai economică. Acest lucru se explică prin simplitatea designului plantei și a lipsei de catalizatori.
Tabelul 8.1. Indicatori ai diferitelor procese de conversie a gazelor naturale (pe 1000 m 3 de gaz transformat) de gaze naturale, m 3.
Procesele de conversie a aburului și a dioxidului de carbon sunt mult mai dificil de menținut și necesită instalarea unor echipamente greoaie, care nu sunt întotdeauna compensate de proprietățile de reducere mai mari ale gazelor produse.
Eficacitatea creșterii potențialului de recuperare a pelvisului superior prin conversia gazului natural depinde în mare măsură de conținutul de azot din acesta, adică și de la îmbogățirea exploziei cu cuptor cu oxigen.
La nivelul modern de curățare a atmosferelor controlate, spălarea gazului de top din CO2 poate fi efectuată prin metoda adsorbției-desorbție utilizând o soluție apoasă de monoetanolamină (MEA). Acest proces, conform unor surse, este considerat relativ ieftin, permițând creșterea potențialului de recuperare a gazelor de eșapament. Cu toate acestea, pentru a realiza prelucrarea gazului de vârf utilizând o astfel de tehnologie, vor fi necesare suprafețe considerabile (aproximativ 10 hectare pe un cuptor de furnal). În plus, metoda de curățare a gazelor folosind MEA se caracterizează prin intensitatea energetică ridicată și, cel mai important, poluarea semnificativă a mediului cu vapori și aerosoli de MEA (MPCp.s = 0,5 mg / m 3).
Dezvoltarea tehnologiei membranei, plasma și catalizatori îmbunătățite și procese catalitice în viitor, probabil, va reduce drastic dimensiunea plantelor de top de tratare a gazelor pentru reutilizare în furnale. De exemplu, chiar și în prezent Institutul Belarus Politehnic pentru producerea de dioxid de carbon (utilizat în industria alimentară, inginerie sudură, petrochimice și alte industrii) a dezvoltat o metodă economică și ecologică a gazelor de ardere de purificare de CO 2 cu adsorbanți solizi - zeoliți sintetici utilizați în modul de termopsevdoozhizhennogo pat fluidizat și un sistem de zeolit adsorber circulant - un striper care poate fi utilizat pentru purificarea gazelor de ardere.
utilizare Calificarea în furnale de diferite tipuri de conversie endotermic de gaze naturale a arătat că utilizarea gazului reducător la cald (1100 - 1300 ° C), comparativ cu gazele naturale reduce consumul de cocs foame este de 1,2 - 1,5 ori.
Costurile suplimentare de capital pentru sistemul de spălare al IEA și încălzirea gazului de furnal dintr-un cuptor cu o capacitate de 3,5 până la 4,0 milioane de tone pe an sunt de aproximativ 11 milioane de ruble; Costul complexului de furnal este astfel majorat cu 16%. Costul de spălare a dioxidului de carbon este de aproximativ 1,3 - 1,5 ruble pe tona de fontă.
Au fost propuse o varietate de scheme de conversie a diferitelor combustibili și de spălare a gazului de top din CO2 (H2O). Deseori, spălarea cu gaz top este combinată cu spălarea produselor de conversie a altor combustibili bogați în CO și H2. introdusă în fluxul circulant al gazului de vârf. De asemenea, este recomandabil să se îmbogățească (până la 10%) gazul spălat cu gaz natural. O schemă posibilă pentru curățarea gazului superior este prezentată în Fig. 8.2. Evident, atunci când se utilizează gaz top ca agent reducător la cald, eliberarea consumatorilor din fabrică ar trebui redusă, ceea ce va necesita înlocuirea acestuia cu gaz natural. Cu toate cuptoarele KIT pentru încălzirea gazului natural este semnificativ mai mare decât explozia, fluxul de gaze naturale prin instalația, în general, utilizând gaze reducătoare fierbinte crește echivalentă cu reducerea consumului de cocs, ținând cont de schimbările din gazele injectate de căldură fizică. Conserva gazelor naturale, care nu mai este acum fi considerat un combustibil ușor disponibile, poate fi realizat cu ajutorul unui gaz de produse de reducere la cald sau a altor cărbuni noncoking de conversie a energiei. În acest caz, problema reducerii consumului de cocs ar fi rezolvată simultan cu problema reducerii consumului de gaze naturale. Testele industriale în această direcție au fost deja efectuate în mai multe țări.
Cele mai bune rezultate sunt obținute prin suflare cu abur oxigen conversie produs de cărbune sau derivat în pat fluidizat dens. Se remarcă faptul că gazeificarea cărbunelui gestiona simultan pentru a trece în zgură până la 90% sau mai mult de sulf conținută în combustibil, ceea ce face ca un astfel de proces este valoros și ecologic foarte metalurgic curat. Multe studii evidențiază eficiența creșterii temperaturii gazelor reducătoare la cald la 1500 ° C și chiar mai ridicate. Temperaturile ridicate injectat gaz permite nu numai pentru a reduce consumul de cocs, dar, de asemenea, duce la o oarecare reducere (până la 5%) din consumul de energie din fier.
După cum sa menționat deja, utilizarea oxigenului și a gazelor reducătoare suflate este interdependentă. În mod natural, rezultatele maxime la înlocuirea cocsului cu alți combustibili pot fi așteptate când se utilizează un oxigen tehnic ca oxidant. Odată cu trecerea de la rece la cald reducerea gazelor, reducerea consumului specific de gaz pe unitate de oxigen în funcție de bilanțul termic gazele Gornova trebuie crescută. Din estimări rezultă că toate acestea împreună pot duce la o reducere a consumului de cocs în cuptoare la 150-200 kg. t / t și pentru creșterea productivității acestora. Aparent, reducerea în continuare a consumului de cocs nu este posibilă din cauza reducerii acțiunii de scurgere a taxa cocs“în explozie, ceea ce va duce la o reducere inacceptabilă a permeabilității sale de gaz. Sunt interesate scheme combinate pentru utilizarea energiei gazului de vârf. .. În general, energia din gazul superior cuptor cu un debit specific de aproximativ 500 kg de cocs t t / m este aproximativ 260 - 280 kg au. t / t. Aproximativ 85% dintre acestea sunt energia chimică, 10% - căldură fizică, 5% - energia potențială a presiunii gazului. O schemă posibilă pentru utilizarea combinată a gazului de vârf este prezentată în Fig. 8.3. O trăsătură caracteristică a schemei de mai sus: arderea gazului de sus într-un încălzitor de regenerare, la presiune ridicată, folosind pentru acționarea turbinei turbocompresorului și gazul generator, blast recuperarea gazului de furnal în elektrogazogeneratore folosind cărbune. Utilizarea energiei electrice pentru încălzirea gazului de sus permite reducerea ridica temperatura la 1500 ° C și complet să renunțe la utilizarea gazelor naturale, înlocuindu-l cu un cărbune ușor disponibile.
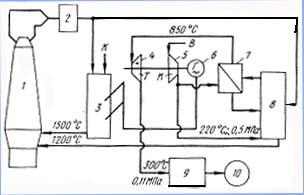
Fig. 8.3. Schema de instalare a utilizării combinate a energiei gazelor de vârf:
1 - furnal;
2 - aparate pentru purificarea gazului uscat;
4 - turbină cu gaz;
7 - încălzitor de aer recuperativ;
8 - încălzitor de aer regenerativ;
9 - utilizarea căldurii de joasă valoare;
10 - coș de fum;
O presiune ridicată de furnal produse de ardere a gazului face posibilă construirea unui încălzitor de aer explozie de 3 - 5 ori mai mică decât în cazul funcționării normale și reduce formarea N0x în timpul arderii. Ca în majoritatea aplicațiilor. procese combinate, principalul dezavantaj este reprezentat prin circuitul de complexitatea SRE utilizarea energiei în produse principale magazin de producție și utilizarea energiei în mai multe etape a gazului de sus. Principalul avantaj al procesului de raportare combinat - aproape dublânduYse coeficientului termic și exergetic al disposability producției de furnal. În general, utilizarea combinată a gazului de sus a plantelor duce la o redistribuire a amestecului carburant, aproape fără a afecta consumul total de combustibil.
Pre-reducere a minereului de fier este, de asemenea, una dintre cele mai eficiente metode de reducere a consumului de cocs. Astfel, potrivit VNIIMTa aplicarea unei pelete de furnal cu 40% metalizare de 40% reduce consumul de cocs cu 13 - 15%, cu o metalizare de 80% - 25 - 30%. Astfel, consumul de energie de fier este redus cu nu mai puțin de 1,0 - 1,5%, costurile reduse sunt reduse cu 2-2.5 rub / t.
Utilizarea de granule de metal (grad total de metalizare de 35 - 40%) poate reduce semnificativ consumul de gaze naturale și de oxigen sau de a elimina utilizarea lor în procesul de furnal. Oxigenul eliberat și gazele naturale pot fi mai economic să fie folosite pentru a produce pelete reducere de gaz și metalizare. Metale și zinc, prezente în multe minerale de fier și materiile prime aglomerate (în special cu adăugarea la ea de nămol de domeniu și otelariile) și se acumulează în volumul furnalului, duce la domeniul deteriorarea fuziunii: reducerea căptușirea viață, defalcare a cuptorului și creșterea consumului de cocs . Materialele de cuptor de grad scăzut de oxidare, resturi și metalisat peleți facilitează îndepărtarea metalelor alcaline și zinc cu gazele de ardere.
Pentru a estima modificarea consumului de cocs de la diferiți factori, se utilizează următoarele valori specifice aproximative ale economisirii cocsului (dacă se ia 500 kg / t ca consum de cocs de bază), kg / t:
Injectarea a 1 m 3 de gaze naturale. 0.7-.9.
Creșterea temperaturii bruiei cu 100 ° С. 7,5-25.
Creșteți conținutul de fier în încărcare cu 1%. 7.5-15.
Metalizarea încărcăturii cu 10%. 25-40.
1 kg de zinc. 15-30.
1 kg de metale alcaline. 5-10.
100 kg de calcar. 15-25.
Reducerea conținutului de mangan în fontă cu 1%. 10-15.
Valoarea medie a minereului de fier la ± 0,3%. 3-5.
Reducerea conținutului de sulf în cocs cu 0,1%. 4 până la 7,5.
Creșterea conținutului de sulf în fontă cu 0,01%. 5-25.
Reducerea conținutului de siliciu din fontă cu 1%. 25-75.
Scăderea conținutului de cocs de cenușă cu 1%. 5-7.
- Dezvoltarea metalelor non-cocs / N.A. Tulin, V.S. Kudryavtsev, S.A. Pchelkin și alții - M. Metalurgia, 1987. - 327 p.
- Tehnologie fără deșeuri în industrie / B.N. Laskorin, B.V. Gromov, A.P. Tsygankov, V.N. Senin - M. Stroiizdat, 1986. - 158 p.
Trimiteți-le prietenilor: