Converter metoda siderurgiei, care se realizează într-o operațiune autogenă (fără surse străine de costuri de energie termică) prin aerul suflat prin fierul topit a fost propus și implementat pentru prima oară un englez Bessemer, după care procesul a fost numit sau proces Bessemer Bessemer. Prin urmare, o metodă de fier topit a fost suflat într-o retortă de oțel căptușit (dinassovym) șamotă acidă. Convertorul are un spațiu vertical de lucru de formă cilindrică. În partea de jos are un detașabil, ușor de înlocuit cu diuze de fund pentru suflare de aer. Și partea superioară este prevăzută cu o gură în formă de con. Capacitatea convertoarelor Bessemer moderne ajunge la 400 de tone.
Convertorul vertical poate fi înclinat în timpul procesului, ceea ce asigură efectuarea tuturor operațiunilor tehnologice necesare: turnarea fontei originale, suflarea topiturii cu aer, prelevarea probelor, golirea produsului finit etc. Toate aceste operațiuni, cu excepția suflării topiturii, se realizează prin gât, care servesc, de asemenea, la îndepărtarea gazelor de proces din convertizor. Atunci când se curăță fierul topit, care este pătruns de fluxurile de ardere de jos în sus, oxigenul oxidează impuritățile din fontă (Si, Mn, C). Când sunt oxidate, se eliberează o cantitate considerabilă de căldură, suficientă nu numai pentru a menține topiturile în stare lichidă, ci pentru a le încălzi până la 1600 ° C înainte de a se scurge din convertizor.
Principalele dezavantaje ale procesului Bessemer sunt calitatea scăzută a oțelului produs, care este îmbogățit în timpul purjării azotului și imposibilitatea de a elimina cele mai nocive impurități, fosfor și sulf, prin această metodă. Pentru topirea fierului Bessemer este necesar ca rezervele acestor minereuri care sunt foarte pure în conținut să fie limitate. În 1878, S. Thomas în locul căptușelii cu acid a folosit principalul și a legat fosforul prin utilizarea de var. Procesul Thomas a extins foarte mult posibilitățile procesului de convertizor pentru producția de oțel. Cu toate acestea, procesul Thomas a păstrat saturația ridicată a oțelului produs cu azot. În plus, oțelul Thomas a crescut fragilitatea și tendința de îmbătrânire, o sută limitează aplicarea sa.
Procesele Bessemer și Thomas au existat aproximativ până la mijlocul acestui secol. Aceste două metode de producție a oțelului au fost înlocuite de un nou proces progresiv, numit convertorul de oxigen (procesul LD în străinătate). Pe scară industrială, a fost prima dată efectuată în Austria în 1952-1953. Caracteristicile caracteristice ale noului proces sunt utilizarea oxigenului tehnologic pentru oxidarea impurităților și alimentarea acestuia în principal pe suprafața topiturii de deasupra, cu ajutorul duzelor verticale de suflare. Până acum, procesul de transformare a oxigenului a devenit o poziție dominantă printre metodele existente de producție în masă a oțelului în toate țările lumii. Importanța practică extrem de mare a acestui proces se explică prin faptul că este adecvată pentru prelucrarea fierului brut de aproape orice compoziție și de fier vechi în cantități de până la 30% din greutatea fontei, posibilitatea de a obține o gamă largă de oțeluri. Inclusiv aliaj, performanță ridicată, flexibilitate ridicată a tehnologiei și produse de înaltă calitate.
În prezent, instalațiile de convertizor de oxigen utilizează convertoare cu o capacitate de 20 până la 450 de tone. Convertoarele de acest tip sunt în formă de pară și echipate cu un gât concentric și un fund gol. Poziția centrală a gâtului creează cea mai bună condiție pentru introducerea unei lance verticale de oxigen, îndepărtarea gazului, turnarea și turnarea resturilor și a fluxului în cavitatea convertorului. Aproximativ în partea centrală a corpului convertorului de oxigen, trunchiurile orizontale sunt fixate în înălțime, asigurând suportul convertorului și rotirea acestuia de-a lungul axului trunchiului cu 360 °, cu o frecvență de rotație de 0,01 până la 2 min¯¹ .Pe convertoare mici forță de rotație este transmisă de la dispozitivul de acționare pe un știft, în convertoare mari, cu o capacitate de mai mult de 200 de tone echipate cu unitate de două sensuri, având două motoare, fiecare știft. Căptușirea convertizoarelor de oxigen topire din oțel este realizată din cărămizi de rășinoase sau de magnezit-cromit.
Oxigenul către topitură este furnizat prin intermediul unui tub vertical, răcit cu apă, care de obicei are trei până la patru duze. Lancea este introdus în convertizor prin gât, situată capăt inferior la o distanță de 1-3 m de la suprafața topiturii furnizând astfel la o presiune de 0,9-1,4 MPa aprovizionare explozie oxidant la suprafață topit. Lungimea tunerului în convertorul modern de 300 de tone atinge 27 m. Cupa de răcire cu apă a vârfului lancei suflantă durează de la 70 la 300 topiri.
Convertorul de oxigen funcționează într-un mod în serie. Procesul începe cu umplerea resturilor de oțel în convertorul înclinat. Sunt turnate fontă lichidă suplimentară, convertorul este plasat într-o poziție verticală, se injectează în el o injecție și alimentarea cu oxigen este furnizată cu o puritate ≥ 99,5%. Simultan cu începutul curățării, se încarcă prima porțiune de fluxuri și minereu de fier. Restul acestor materiale sunt alimentate în timpul purjării cu una sau mai multe porțiuni.
Procesele de oxidare și de formare a zgurii în convertorul de oxigen sunt foarte intense, datorită temperaturilor ridicate, care în zona de reacție ating 2500 ° C și o bună circulație a metalului și amestecarea acestuia cu zgură. Oxidarea impurităților din fontă este efectuată în principal prin faza de zgură. În primul rând, în conformitate cu legea acțiunii în masă, fierul, care este prezent în topitură în cea mai mare cantitate, este oxidat de reacția
2Fe + O2 = 2FeO + 539800 kJ
FeO rezultat ca urmare a transferului de masă intens în topitură este transferat în faza de zgură și este principalul oxidant al impurităților. Oxidarea impurităților are loc la interfața metal-zgură conform reacțiilor:
Si + 2FeO = Si02 + Fe;
Mn + FeO = MnO + Fe;
2P + 5FeO = P2O5 + 5Fe;
În secțiunile în care vitezele gazului oxidant sunt nesemnificative și transferul de masă este slăbit, oxidarea directă a carbonului și impuritățile cu oxigen prin explozie este posibilă, de exemplu, în conformitate cu reacția 2C + 02 = 2CO. Eliberarea CO în oxidarea carbonului în toate cazurile contribuie la o mai bună amestecare a fazelor de metal și de zgură.
Oxidarea tuturor impurităților din fontă se realizează prin reacții exoterme de la începutul purificării. Siliconul și manganul sunt oxidate cel mai intens la începutul curățării, ceea ce se explică prin afinitatea lor ridicată la oxigen la temperaturi relativ scăzute. Concentrația ridicată în topitura de FeO contribuie la îndepărtarea fosforului. În plus, oxidarea rapidă a fosforului, precum și a siliciului datorată legării oxizilor lor de var ca răspuns la:
Si02 + 2CaO = 2CaO • Si02,
P2O5 + 4CaO = 4CaO • P2O5.
Odată cu procesul de conversie a fontei, bazicitatea zgurii crește continuu, iar în a doua jumătate a purjării ajunge la o valoare> 2,5 când sunt create condiții favorabile pentru îndepărtarea sulfului din topitura metalică. Îndepărtarea sulfului conținut în fier și oțel se realizează în funcție de reacția totală
Fe + S + CaO = FeO + CaS.
Întregul ciclu tehnologic din convertorul de oxigen durează 50-60 de minute, inclusiv suflarea oxigenului cu 18-30 de minute. La atingerea unui conținut de carbon predeterminat în explozie de oțel este oprit, convertorul podymajut lance este înclinată, și un metal special printr-o gură de evacuare în oala de turnare este turnat. După drenarea oțelului de la convertizor, o zgură este drenată prin gât. Metalul obținut în convertorul de oxigen conține o cantitate crescută de oxigen, ceea ce necesită o deoxidare obligatorie. Deoxidarea se efectuează prin adăugarea de metale mai active, cu o afinitate crescută la oxigen în cazanul sau jgheabul care transportă metalul în el din convertor. Avantajul major al oxigenului - proces de conversie, duce la fierbere rapidă în timp ce purjare topiturii, temperatura ridicată se topește posibilitatea rapidă și reglementarea acestuia, permite utilizarea sa pentru producerea de oțeluri aliate. Principala dificultate în acest caz este introducerea elementelor ușor oxidante în timpul purjării (Cr, Mn, Si). Introducerea elementelor care au o afinitate mai mică pentru oxigen (Ni, Cu, Mo)? Puteți petrece orice perioadă de topire. Aditivul este elemente de aliere ușor oxidabile frecvent realizate împreună cu dezoxidant în oala de turnare de oțel după topirea preliminară într-un cuptor special sub formă de feroaliaje (solide).
În timpul curățării fierului în convertizor, se formează un număr mare de gaze incandescente cu un grad de praf suficient de ridicat. O cantitate mare de formare de praf se datorează oxidării intense a fierului și evaporării acestuia: fumul de fier se ridică la 6-7%. Pentru a utiliza căldura fizică a gazelor și a le curăța de praf, convertoarele sunt utilizate pentru a instala cazane de căldură reziduală și instalații de colectare a prafului.
dezavantajele procesului BOF menționate mai sus au servit ca bază pentru îmbunătățirea în continuare a tehnologiei și design hardware. O comparație a avantajelor și dezavantajelor siderurgiei într-un convertor cu mai mic (de jos), iar suflatul superior a fost dezvoltat proces combinat, în care un metal este procesat de mai sus doar cu oxigen pur, iar fundul sau oxigenul din izolarea inelului de hidrocarburi sau gaz inert - azot sau argon. Pelicula protectoare diuze jeturi de oxigen de fund și de jos de la distrugere rapidă, ca urmare a expunerii la temperaturi ridicate și se topesc barbotare intens. purjarea periodică cu azot sau argon okislennost reduce zgură și metal, oxidarea lentă a manganului, creșterea gradului de îndepărtare a fosforului și sulfului în fază gazoasă, reducând astfel consumul de var. Consumul de var contribuie, de asemenea, pentru a reduce posibilitatea injectării sale directe în topitură împreună cu oxigen prin partea de jos.
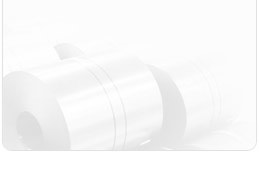
Articole similare
-
Producția, istoria spiritelor - modul în care Franța a devenit legiuitorul modei de parfum
-
Metoda convertorului pentru producția de oțel, portal metalurgic
Trimiteți-le prietenilor: