Pentru a curăța cerealele, de regulă, utilizați site cu găuri dreptunghiulare sau rotunde. Prin găurile dreptunghiulare trece granulația, a cărei grosime este mai mică decât lățimea gaurii, iar prin rotundă - granulația, a cărei lățime este mai mică decât diametrul gaurii (Figura 1). Cerealele, ale căror dimensiuni transversale sunt mai mari decât dimensiunile orificiului de sită, nu trec prin aceste găuri, ci se deplasează de-a lungul sita, lăsându-l. Particulele și boabele care trec prin găurile sita sunt numite pasaje și care coboară și coboară.
Grânele de grâu sunt împărțite în următoarele fracții.
Mare - o coborâre dintr-o sită cu găuri de 2,8x20 mm.
Mediul trece printr-o sită cu orificii de 2,8 x 20 mm și coboară dintr-o sită cu orificii de 2,2 * 20 mm.
Mic - un pasaj printr-o sită cu găuri de 2,2x20 mm, provenind dintr-o sită cu orificii de 1,7x20 mm.
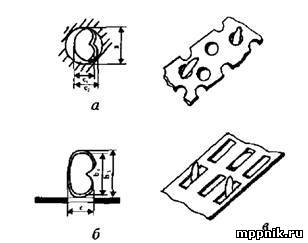
Fig. 1. Sortarea masei de cereale pe site
a - lățime; b - în grosime; c este mișcarea particulelor pe site
În mașinile de curățat cereale, se utilizează perforarea metalului (Figura 2) și, mai rar, se folosesc site metalice. Straturile de ștanțare ștanțate sunt realizate din tablă zincată galvanizată cu o grosime de 0,5-1,5 mm. Găurile din ele au o formă rotundă, dreptunghiulară și rareori triunghiulară.
Siturile cu găuri rotunde sunt caracterizate printr-un diametru și găuri alungite de lungime și lățime, de exemplu, 2,0X25 mm. Dimensiunea de lucru a găurilor este: ziua găurilor rotunde este diametrul, pentru găurile alungite - lățimea, pentru triunghiulare - partea triunghiului obișnuit. Numărul ecranului este caracterizat prin dimensiunea dimensiunii orificiului de lucru înmulțită cu zece. De exemplu, o sită cu găuri rotunde de 4,5 mm în diametru va avea numărul 45.
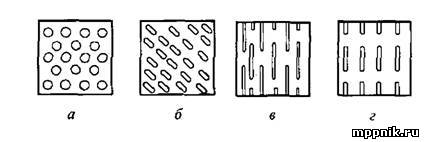
Fig. 2. Ecrane plate de perforare a mașinilor de curățat cereale
a - cu găuri rotunde; b - cu găuri ovale diagonale; v - cu orificii alungite ovale; g - cu orificii paralele-ovale
Lungimea găurilor dreptunghiulare este aleasă în funcție de lățime.
Fețele dreptunghiulare de pe ecran, de regulă, sunt aranjate în rânduri, iar cele rotunde sunt eșalonate. Cu aranjamentul eșalonat al găurilor, comparativ cu cele obișnuite, coeficientul secțiunii vii crește cu 16%. În plus, este posibil să se obțină o rezistență mai uniformă a ecranului, deoarece distanțele dintre găuri sunt identice în toate direcțiile. Atunci când se plasează găuri în rânduri, există posibilitatea ca particulele individuale de cereale, care se deplasează de-a lungul ecranului, să nu intre în găuri.
În mașinile de curățat cerealele, ecranul este instalat oblic la un unghi de 3-17 grade. Aceasta este semnificativ mai mică decât unghiul la care produsul se va deplasa pe ecran sub acțiunea gravitației. Prin urmare, pentru ca granula să se deplaseze de-a lungul ecranului, acesta este informat despre o mișcare de translație circulară reciprocă sau circulară.
În separatoarele cu mișcare alternativă se utilizează site cu găuri alungite orientate în direcția oscilațiilor, iar în ecrane cu mișcare transversală circulară se folosesc ecrane cu orificii orientate în direcții reciproc perpendiculare.
Pe site, grosimea stratului de cereale, începând de la punctul de sosire, scade treptat. S-a stabilit că stratul de granule mai gros pe o sită, cu atât sunt mai puține impuritățile separate. Prin urmare, dimensiunile găurilor în astfel de site nu sunt aceleași: în primul rând, există ecrane cu una mare și, în final, cu un diametru mai mic al găurilor.
Numărul de sită este setat în funcție de mărimea orificiului selectat în funcție de forma și mărimea cerealelor care trebuie curățate și de impuritățile care trebuie separate. Separatoarele de cereale, utilizate pentru separarea fracționării masei de cereale și de purificare a cerealelor, se recomandă să se instaleze patru rânduri de site cu ochiuri de dimensiuni (mm): diametrul primirea sită 14-16, sortarea - diametru 6-8, evacuare - diametrul 4-6 podsevnyh sită - 1,7x20 mm (pentru grâu).
Eficiența tehnologică a separatoarelor este determinată de cantitatea de adaos de buruieni conținută în cereale înainte și după mașină. Impuritățile mari ar trebui izolate complet, mici - până la 90%, impurități ușoare - până la 80%. Eficiența tehnologică a separatoarelor este influențată de cantitatea și natura impurităților din masa cerealelor, de alegerea corectă a sitelor, de distribuția uniformă a cerealelor pe lățimea ecranelor, de înclinarea ecranelor și de curățarea acestora, de încărcătura pe mașină,
Curățarea masei de cereale de la impurități care diferă în lungime. În masa de cereale există impurități care au aceeași lățime și aceeași grosime cu granulația, dar diferă de ea în lungime. Acestea includ boabe scurte (castraveți, mazare de câmp, hrișcă, boabe sparte) și cereale mai lungi decât cerealele principale (ovăz, ovăz, orz). Curățarea granulelor de pe sitele de pe aceste impurități nu dă un efect de separare ridicat.
Pentru acest tip de separare (separare după lungime), se utilizează trieri (Figura 3). Impuritățile scurte sunt izolate în mașinile de recoltat de păpuși și cele lungi în mașinile de recoltat de ovăz. Copacii pentru proiectarea principalelor organe de lucru se împart în două grupe: cilindrice și disc. Cea mai largă aplicație în mini-mori a fost trieda cilindrică.
Discurile de disc produc un singur rotor, au o performanță ridicată cu dimensiuni globale mai mici și sunt echipate cu discuri de control. În conformitate cu schema tehnologică, sunt instalate mai întâi mașinile de recoltat marionete, iar apoi - mașinile de recoltat de ovăz. Indicatorul eficacității activității trierului este gradul de separare a impurităților scurte și lungi. Curățarea este considerată eficientă dacă cel puțin 70% din impurități sunt eliberate din masa cerealelor. Următorii factori principali influențează eficiența de curățare (separarea): gradul de weediness a masei de cereale, sarcina specifică pe suprafața celulară a trireme, viteza discurilor, forma și dimensiunea celulelor. De exemplu, pe măsură ce crește viteza unităților, crește productivitatea mașinilor, dar condițiile de precipitare a fracțiilor scurte din celule se deteriorează, ceea ce duce la o scădere a eficienței. Sarcina specifică exercită un efect invers asupra eficienței de separare.
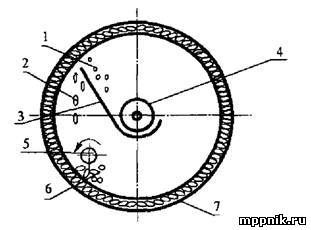
Fig. 3. Schema de separare pe lungime:
1 - particule scurte; 2-particule lungi; 3 - găleată; 4, 5 - șnec; 6 - amestec de produse; 7 - corpul mașinii
Curățarea masei cerealelor de la impurități care diferă în proprietățile aerodinamice. Mașini pentru îndepărtarea impurităților ușoare din masa cerealelor cu un debit controlat al aerului. Principalele mașini includ separatoare de aer: aspiratoare, coloane de aspirație, mașini de separare pneumatică etc.
Separatoarele pneumatice (separatoare pneumatice) sunt utilizate pentru depunerea produsului principal (cereale) din rețeaua pneumatică și separarea impurităților de la cultura principală prin proprietăți aerodinamice. Astfel de impurități includ filme florale, părți de tulpini și urechi, pleavă, semințe de buruieni, boabe fragile ale culturii principale, praf, coji, butași etc.
Separatoarele pneumatice pot fi împărțite în două grupuri cu ciclu de aer liber și cu un ciclu de aer închis.
Primul grup include coloane de aspirație, utilizate pe scară largă în fabricile de făină și separatoare pneumatice pentru mori cu transport pneumatic. Acestea din urmă sunt fabricate cu o cameră de separare și fără ea. Al doilea grup cuprinde, în principal, aspiratoare cu dublă suflare, utilizate în departamentele de curățare a cerealelor de morărit și de cereale.
Eficiența mașinilor depinde în primul rând de cât de diferite sunt proprietățile aerodinamice ale particulelor și de cea mai mare parte a cerealelor.
Caracteristicile aerodinamice determină capacitatea particulelor de a rezista la debitul de aer și depind de forma, mărimea și masa particulelor, de condițiile de suprafață etc. Cerealele sunt curățate într-o creștere verticală și mai puțin frecvent într-un flux orizontal de aer,
În fluxul vertical de aer ascendent, gravitatea G, forța P, egală cu forța de ridicare a fluxului de aer, acționează asupra fiecărei granule și impurități. Particulele de lumină, în care P este mai mare decât G, sunt purtate de fluxul de aer, iar o granulă greu, în care G este mai mare decât P, cade în jos. Dacă P = G, boabele se află într-o stare suspendată (starea de veghe). Viteza aerului care corespunde acestei stări se numește viteza de înfășurare. Diferența în vitezele de vortare a componentelor amestecului servește ca un indicator al posibilității separării lor. Cu cât este mai mare diferența dintre valorile vitezei componentelor, cu atât mai bine poate fi separat amestecul separat.
Eficiența curățării cerealelor prin debitul de aer este estimată prin cantitatea de impurități eliberate din cereale. Principalii parametri care asigură eficiența curățării cerealelor și claritatea separării sunt încărcătura specifică a cerealelor, viteza debitului de aer, gradul de înfundare a amestecului,
Curățarea masei de cereale de la impuritățile dificil de separat. În masa de cereale există impurități precum pietricele, nisip grosier, fragmente de sticlă etc., numite minerale. Dacă aceste impurități nu diferă în dimensiunile geometrice de la boabele culturii principale, acestea sunt clasificate ca fiind dificil de separat.
Mașinile de detașare din piatră sunt utilizate pentru a extrage impuritățile minerale. Baza procesului de curățare a cerealelor din impuritățile minerale în mașinile de separare a pietrelor este diferența în densitatea boabelor și a impurităților minerale, precum și diferența coeficienților lor de frecare. La prelucrarea masei de cereale pe corpurile de lucru se efectuează auto-sortarea: particulele cu densitate mai mare (impurități minerale) se deplasează în straturile inferioare, iar în straturile superioare, particulele cu o densitate mai mică (granulație) se mișcă.
Mașinile de separare a pietrelor, în funcție de designul corpului de lucru, sunt împărțite în trei grupe: cu suprafețe de lucru conice; cu suprafețe plane; cu suprafețe de plasă și suflare a aerului, care intensifică procesul de auto-sortare și, prin urmare, separarea cerealelor și a impurităților minerale. Mașinile din primele două grupuri au o mișcare circulară înainte a organelor de lucru, iar cea de-a treia - reciproc.
Eficiența mașinilor este determinată în același mod ca și eficiența separatoarelor de cereale, adică privind conținutul de impurități minerale înainte și după tratament, ar trebui să fie de cel puțin 96-99%.
Purificarea cerealelor din impurități metalomagnetice. Masa de cereale, ca și în celelalte materii prime care intră în întreprinderile de prelucrare de cereale, precum și în produsul finit poate fi impurități metallomagnetic foarte diferite în mărime, formă și origine: tramp obiecte metalice mici, particule de uzura mașinilor de lucru și a altor organe.
Pentru separarea impurităților magnetice metalice, sunt utilizate coloane magnetice și separatoare electromagnetice, în care proprietățile magnetice ale componentelor sunt utilizate ca o caracteristică de separare. În coloanele magnetice, un câmp magnetic este creat de magneți permanenți, în separatoare electromagnetice - prin electromagneți.
Instalarea protecției magnetice la întreprinderile de prelucrare a cerealelor este reglementată de reglementări în conformitate cu Regulile de organizare și întreținere a procesului tehnologic. De exemplu, în fabricile de făină este instalat în fața tuturor mașinilor cu corpuri de lucru rotative: mașini de tundere, mașini de periat, mașini cu role și, de asemenea, controlul produselor finite.
Eficiența separării magnetice este evaluată prin gradul de separare a impurității magnetice-metalice. Eficiența afectează uniformitatea distribuției produsului a câmpului magnetic aparate, viteza și grosimea stratului de produs (grosimea stratului pentru produsele Mealy nu trebuie să depășească 7 mm și 10 mm pentru cereale), purificarea magneții metodă.
Tratarea suprafeței cerealelor. Cereale, curățate de impurități, care necesită o prelucrare ulterioară, deoarece conține pe suprafața sa o cantitate mare de praf și bulgări de noroi, un număr semnificativ de microorganisme. Trei tipuri de mașini de forfecare sunt utilizate pentru a prelucra straturile superioare ale cerealelor. Utilizarea acestor mașini pentru prelucrarea cerealelor uscate face posibilă îndepărtarea parțială a barbei, a embrionului, a cochililor de sus a boabelor. Pentru morile utilizate mașină Decaparea: cilindru abraziv (Emery, așa-numita tare), oțel (moale) și un cilindru de oțel grilă fațete (Figura 4.).
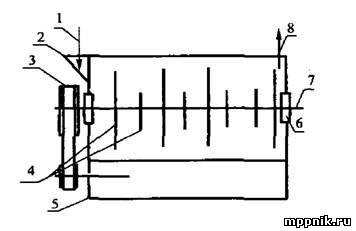
Fig. 4. Schema mașinii ceramice
1 - o conductă de ramificație primită; 2 - grilaj de siguranță; 3 - curea centurii plate; 4 - dăunători propelliformi; 5 - cilindrul din oțel; 6 - carcasa lagărului; 7-arbore; 8 - conexiune de evacuare
Mașinile cu cilindru abraziv sunt utilizate, de regulă, cu pregătirea preliminară a cerealelor pentru expunerea intensivă la acesta; mașinile cu cilindru de oțel (plasă) - în etapele ulterioare de pregătire pentru un impact mai redus asupra cerealelor, ceea ce duce la o scădere a cantității de cereale sparte. În funcție de amplasarea corpului principal de lucru, se disting mașini cu axe verticale și orizontale de rotație.
Eficiența tehnologică a curățării suprafeței de cereale în mașinile de croșetat și periere este estimată prin scăderea conținutului de cenușă al boabelor și prin creșterea numărului de boabe sparte.
A stabilit următoarele standarde de performanță: reducerea granule de cenușă pe trecere (cel puțin) 0,03-0,05% - dezghiocare mașinii cu un cilindru abraziv, 0,01-0,03% - pentru a se potrivi cu cilindrul de oțel și cu un cilindru de oțel fațete din oțel, o creștere a boabelor sparte (nu mai mult), respectiv 1-2 și 1%.
În eficiența tehnologică afectată de următorii factori: proprietăți tehnologice de cereale (. Miezului, umiditate și durabilitate al), Parametrii de lucru de bază ale organelor de mașini (viteza circumferențială a tamburului, caracteristica suprafeței de lucru, decalaj, etc.), sarcina specifică pe cereale mașinii, exprimată în kg / m2-oră
Articole similare
Trimiteți-le prietenilor: