Sudarea bronzului. Bronzurile - este aliaje de cupru cu alte elemente, staniu, siliciu, mangan, fosfor, beriliu, etc. Prin numele lor principal element de aliere numit staniu (de la 3 la 14% staniu), silicios, fosfor, etc ...
Sudarea din bronz este utilizată în reparații, reparații ale turnării sau prelucrării, precum și în prelucrarea suprafețelor. Detaliile din bronz pot fi sudate cu preîncălzire la 350-400 ° C (produse mari 500-600 ° C) și fără ea. putere
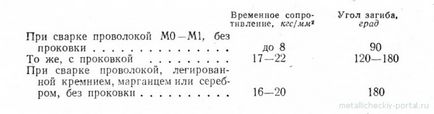
bronz la temperaturi ridicate este redus, astfel încât piesa trebuie să fie atent fixat înainte de sudare, astfel încât să nu-l deterioreze, ca urmare a șocurilor și bumps.
După sudarea pieselor de bronz din aliaj recoapte prin încălzire la 600-700 ° C și menținut la această temperatură timp de 3-5 ore. Piesele turnate de temperatura de încălzire la 200 ° C se produce la o viteză nu mai mare de 100 grade / h. Pentru piese turnate responsabile din bronzurile vysokoolovyanistyh expuse la sarcini alternante și impacturi recoacere la 750 ° C și călire ulterioară aplicate la 600-650 ° C bronz prokovyvayut laminate la rece pentru a crește densitatea și rezistența metalului de sudură.
Cu încălzire rapidă și răcire rapidă ulterioară a bronzului de staniu, incluziunile de aliaj fragil, bogat în staniu, au evoluat pe suprafața piesei, ceea ce reduce brusc rezistența piesei și poate cauza distrugerea acesteia.
Sudarea cu arc a bronzului este realizată cu un electrod metalic sau carbon în poziția inferioară.
Atunci când sudați cu un electrod de carbon, utilizați o polaritate directă de curent direct; Valoarea curentului este de 25-35 A pe 1 mm diametru al electrodului, care este luat de la 5 la 12 mm (de obicei 6-8 mm), tensiune arc 40-45 V, lungime arc 20-26 mm. La sudarea bronzurilor de aluminiu, utilizați fluxuri care sunt active în ceea ce privește oxidul de aluminiu (A12O3), de exemplu fluxul VAMI (Tabelul 29). Fluxul este acoperit cu tija de umplere, ca și cu un strat de acoperire. Pentru a elimina oxizii din baie, electrodul și bara fac mișcări zig-zag transversale. Se recomandă utilizarea preîncălzirii la 300-350 ° C pentru a îmbunătăți calitatea sudării.
Pentru sudarea bronzului de staniu se iau tije de compozitie: 8% zinc, 3% staniu, 6% plumb, 0,2% fosfor, 0,3% nichel, 0,3% fier, restul de cupru. Pentru alte bronzuri, se utilizează o tijă de aceeași compoziție ca și metalul de bază. Rezistența temporară a metalului de sudură în timpul sudării cu un electrod de carbon este: bronz staniu și siliciu - 35-40 kgf / cm 2. bronz de aluminiu - 40-45 kgf / cm2.
Sudarea bronzului cu un electrod metal este larg utilizată. Cele mai bune rezultate sunt obținute prin sudarea DC cu polaritatea inversă; valoarea curentă 30-40 a pe diametru de 1 mm al electrodului. Când utilizați curent alternativ pentru a mări stabilitatea arderii arcului, creșteți curentul la 75-80 A pe 1 mm din diametrul electrodului sau utilizați un oscilator.
Sârma de electrod este preluată în aceeași compoziție ca și metalul de bază. Pentru majoritatea marcilor de bronzuri de turnătorie, dacă este permisă de cerințele de rezistență și rezistență la coroziune, utilizați electrozi de bronz de grad Br.KMZZ-1 (3% siliciu, 1% mangan, restul - cupru). Sudarea bronzurilor de aluminiu se realizează cu electrozi de bronz care conțin 10% aluminiu și 3-5% fier. La sudarea complexului de bronz din aluminiu
Electrozii cu dopaj suplimentar cu nichel sau mangan dau rezultate bune. Manganul reduce posibilitatea fisurilor în sudură.
La bronzurile de sudare se utilizează învelișuri cu diferite compoziții (vezi Tabelul 28).
Electrozii cu dopaj suplimentar cu nichel sau mangan dau rezultate bune. Manganul reduce posibilitatea fisurilor în sudură.
La bronzurile de sudare, se folosesc straturi de acoperire cu diferite compoziții (vezi tabelul 28).
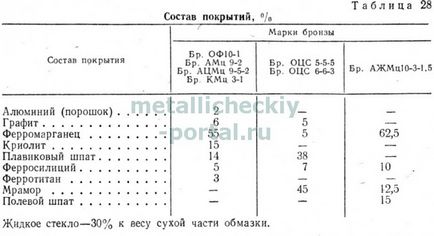
Pentru sudarea bronzurilor de nichel laminate se utilizează o acoperire din compoziție: feromangan - 28%, ferosiliciu - 41%, feldspat - 28%, magneziu - 3%. De obicei, bronzul de nichel de până la 6 mm grosime este sudat cu electrozi cu diametrul de 3,4 și 5 mm, cu un curent de 25-35 a / mm diametru electrod.
Sudarea bronzului Br.Mts5 este produsă de electrozi de cupru cu "Komsomolets-100" cu preîncălzire la 400-500 ° C.
Sudarea cu bronz se realizează fără întrerupere într-un singur strat. Electrodul este ținut aproape perpendicular pe suprafața metalului. Pentru o mai bună îndepărtare a gazelor, electrodul este realizat prin mișcări zig-zag. Pentru a obține înălțimea maximă a suprafeței, se realizează cu un loc de depunere preformat cu o înclinație de până la 15 grade față de orizontală. Modul este rafinat prin sudarea probelor. La sudarea fără încălzire se utilizează un curent mai mare.
Cu performanța corespunzătoare a bronzului de sudură cu electrozii de topire, proprietățile mecanice ale metalului de sudură sunt aproximativ egale (sau puțin mai mici) cu proprietățile metalului de bază.
Pentru bronzurile laminate de grosime mică, cele mai bune rezultate sunt obținute prin sudarea în argon cu un electrod de tungsten ne-consumabil.
Sudarea cu gaz a bronzului este utilizată pentru repararea pieselor turnate și a suprafețelor de frecare. Dacă este necesar, sudarea se face cu încălzire la 450 ° C pentru a preveni apariția fisurilor. Flacăra de sudare trebuie să fie regeneratoare,
Tratamentul termic al bronzului după sudarea cu gaz se realizează pe regimurile utilizate pentru tratarea termică a bronzului. mărcile după sudură cu arc.
În sudarea cu gaz a bronzului, rezistența îmbinării sudate se obține egală cu 80-100% din rezistența metalului de bază.
Sudarea alama. Alama este un aliaj de cupru și zinc având un punct de topire de 1060-1100 ° C. Atunci când sudarea cu arc electric este evaporarea intensă de alamă, zinc și metal topit, absorbție de hidrogen, care nu reușește să stea în timpul solidificării metalului topit, având ca rezultat formarea de bule de gaz și pori .
Hidrogenul intră în metalul lichid din acoperire sau flux.
La sudarea cu arc a alamelor cu un electrod metalic se utilizează un curent direct de polaritate directă. Sudarea se realizează în poziția inferioară cu un arc scurt. Curentul pentru un electrod de 5 mm în diametru este luat de 250-275 a. Sudarea se realizează cu o viteză de cel puțin 0,3-0,4 m / min. După sudare, cusătura este forjată și apoi recoacere la 600-650 ° C. Dacă cuprul conține mai puțin de 60% cupru, atunci este forjat la o temperatură de 650 ° C, dacă este mai mare de 60%, apoi într-o stare rece. Alama trebuie să fie sudată într-un singur strat, deoarece sudarea multistrat conduce la fisuri.
Ca fir utilizat electrod de compoziție alamă: 38,5-42,5%) zinc, 4-5% mangan, 0,5% aluminiu, 0,5 până la 1,5% fier, 1% alte impurități, restul - cupru . Acoperirea este format din 30% concentrat de minereu de mangan 30% titan, 15% feromangan, 20% cretă, 5% sulfat de potasiu, 35% apă-sticlă - greutatea pieselor de spălare uscată. Acoperirea este aplicată cu un strat de 0,2-0,3 mm. După întărirea acoperirii, se aplică un strat de flux de 0,9-1,1 mm grosime. Ca flux, se utilizează zgură de bor amestecată cu sticlă lichidă.
La sudarea alama cu un electrod de carbon, sunt utilizate aceleași fluxuri și regimuri, ca în cazul sudării cu cupru.
Rezultatele bune sunt obținute prin sudarea alamului cu un arc de carbon utilizând o sârmă LCM-40-4.5 care conține 40% zinc și 4,5% mangan. Ca flux, zgură de bor sau calcinată
Alamele sunt greu de sudat, deci de obicei sunt sudate cu sudare cu gaz. Pentru a reduce evaporarea zincului, sudarea din alamă este condusă cu o flacără de oxidare cu un exces de oxigen de 30-40%, adică 1,3-1,4 m 3 de oxigen este furnizat arzătorului pe m 3 de acetilenă. În acest caz, se formează o peliculă de oxid de zinc lichid pe suprafața bazinului de sudură, ceea ce reduce evaporarea acestuia. Excesul de oxigen oxidează partea principală a flăcării hidrogen, ca urmare a scăderii absorbției de hidrogen de către metalul lichid.
Pentru a elimina oxizii de cupru și zinc, se folosesc fluxuri de aceeași compoziție ca și în sudarea cuprului.
Ca flux, cel mai adesea se utilizează un borax calcinat, care este diluat cu apă și aplicat ca pastă pe marginea metalului. Din evaporarea zincului, un flux de 20% borax calcinat și 80% acid boric protejează bine.
Mâinile de alamă înainte de sudură sunt curățate pentru a străluci de o piele, un fișier sau o perie metalică. Dacă pe suprafață există un strat de oxizi, alamă este gravată într-o soluție de acid azotic 10% și apoi spălată cu apă fierbinte. Marginile sunt cosite în același unghi ca la sudarea oțelului. Prin urmare, puterea flacării ar trebui să fie aceeași ca la sudarea oțelului - 100-120 dm 3 / h acetilenă la 1 mm din grosimea plăcii.
Pentru a reduce evaporarea zincului și absorbția de către metal a hidrogenului, capătul miezului de flacără trebuie să fie de 2-3 ori mai mare decât metalul care trebuie sudat decât în cazul sudării oțelului. Flacăra trebuie îndreptată spre firul de sudură, care este ținut la un unghi de 90 ° față de axa piesei bucale. Capătul firului este scufundat din când în când în flux, care este de asemenea turnat în bazinul de sudură și pe marginile cusăturii. Sudarea se face rapid.
VNIIAvgenmash sa dezvoltat pentru sudarea sârmei de sârmă de umplutură din clasa LK62-05, care conține 60,5-63,5% cupru, 0,3-0,7% siliciu, restul - zinc. Silicul din sârmă este un deoxidant, care reduce oxidarea și evaporarea zincului. Ca flux, la sudarea cu acest fir, se utilizează un borax calcinat. Sudarea LK62-05 asigură curățenia bazinului sudat, o cusătura densă, neporoasă și o cantitate mică de vapori de zinc. Flacăra se oxidează cu un exces de oxigen de 30-40% în amestec.
Pentru sudarea L62 alama, JI68 și alte VNIIAvtogenmashem proiectate ca autofondant LKB062-02-004-05 sârmă de umplere care conține: 60,5-63,5% cupru, 0,15-0,2% Si, 0,03-0, 07% bor, 0,4-0,6% staniu, restul de zinc. Inclus în sârmă bor îndeplinește funcția de flux, astfel firul de sudura pierderilor de zinc din alama sunt practic absente, iar productivitatea este îmbunătățită. Utilizarea fluxului în acest caz nu este necesară.
Pentru a crește densitatea și rezistența cusăturii după sudură, uneori este falsificată, netezind armătura cu metalul de bază. Forjarea este efectuată într-o stare rece sau încălzită, în funcție de conținutul de cupru din alamă.
Pentru a face structura granulară de sudură din metal și lucrările de întărire efect de distrugere cusătură după forjare recopt la 600-650 ° C și apoi se răcește încet. Recoacerea la temperaturi de peste 650 ° C nu este permisă, deoarece la o astfel de temperatură poate duce la evaporarea parțială a zincului. Ele pot fi, de asemenea, recoaptă la o temperatură de 260-280 ° C, care nu modifică structura metalului, dar distruge tensiunile interne reziduale din alamă, care îl protejează de cracarea ulterioare.
Perechile albe de oxid de zinc eliberate în timpul sudării alamei sunt dăunătoare organismului uman. Prin urmare, atunci când sudați alamă cu fir obișnuit, ar trebui să utilizați o mască de protecție (respirator) și să instalați aspirația locală de ventilație în apropierea stației de sudură. Concentrația admisă a zincului nu trebuie să depășească 0,005 mg / dm 3.
Cele mai bune rezultate se obțin prin arc submerse sudare alama BM-1, dezvoltat VNIIAvtogenmashem și un amestec de 25% alcool metilic (SNzON) și 75% metilborata [B (CH3 0) 3]. Acetilena este trecută prin acest lichid, umplând un vas special - fluxer, unde este saturat cu vapori de flux și apoi trece la arzător. Fluxurile intră în flacăra de sudură, în care boratul de metil este ars de reacție:
Boric anhidridă B2 03 formează o flacără în acid volatil boric (H2 B03), care este depus pe articol și din nou descompus, formând anhidridă borică, care fluxurile de substanță. Alcoolul metilic conținut în lichidul de flux este complet ars în flacără, fără a da compuși dăunători procesului de sudare. Consumul de flux BM-1 pentru a obține metalul sudat de calitate bună este de aproximativ 70 g pe 1 m3 de acetilenă.
Alama sudare cu ajutorul fluxului BM-1 poate îmbunătăți dramatic performanța, ceea ce face procesul aproape inofensiv pentru sudorul produce, dens, metal pur sudură neporoase fără forjare, o rezistență temporară la 38 kgf / mm2 unghi de 180 ° îndoire, rezistență la impact 15 kgf m / cm2.
Fluxul BM-1 este potrivit pentru sudura de alamă de toate gradele, sârmă care conține și nu conține siliciu. Sarma cu flacără cu flux BM-1 poate avea un exces de oxigen de la 10 la 40%.
În cazul suprafeței de gaz a alamelor pe piesele de oțel pentru a crește rezistența lor, rezultate bune sunt obținute utilizând o flacără de propan-butan-oxigen. Suprafața se realizează cu preîncălzirea părților la 700-800 ° C, alamă LZhMts59-1-1 utilizând fluxul de la 50% borax și 50% acid boric. În același timp, arderea zincului nu depășește 2%. Rezistența la tracțiune a metalului sudat este de 36 kgf / mm 2. Unghiul de îndoire de 180 °, duritatea 7 kgf-m / cm 2. porozitate redusă și creșterea eficienței depunerilor comparativ cu sudarea cu flacără acetilenă-oxigen.
Articole similare
Trimiteți-le prietenilor: